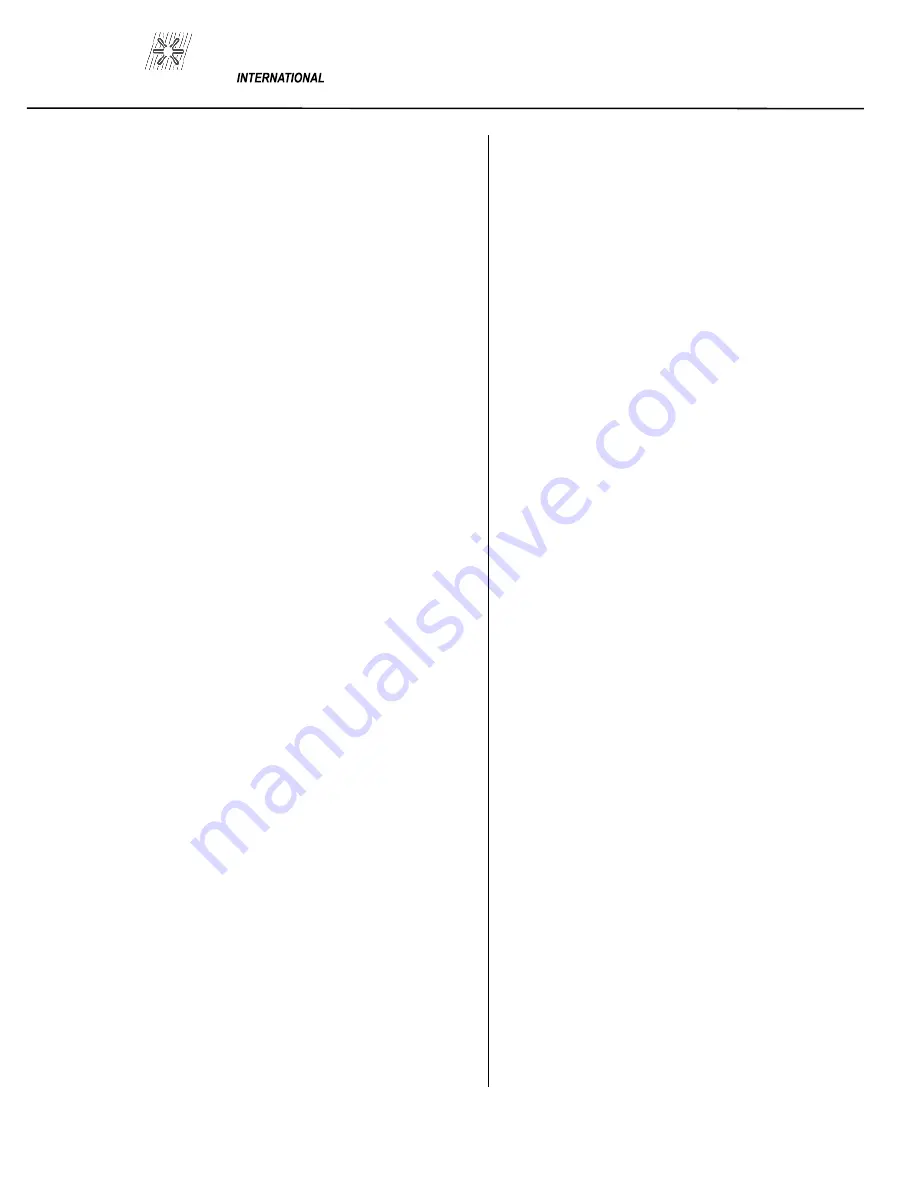
ARC 6 5 6
PRO
WEL D
1.0 INTRODUCTION
Your new stud welding equipment has been carefully con-
structed using the finest components and material available.
Used properly, this equipment will give you many years of
profitable, efficient service.
The system incorporates the latest in engineering advances for
complete, reliable end welding of mild steel, stainless steel
and aluminum fasteners.
A careful study of this manual will enable you to understand
how the welder operates to insure proper performance under
all conditions.
2.0 WARRANTY
The electrical and mechanical components of the stud
welder are thoroughly performance inspected prior to assem-
bly in the welder. The assembled welder is completely per-
formance checked. The welder is delivered to you in func-
tional electro-mechanical condition.
All parts used in the assembly of the welder and its ac-
cessories are fully warranted for a period of 1 YEAR from the
date of delivery. In addition, the welding capacitors are war-
ranted for a period of 1 YEAR from the date of delivery. The
printed circuit boards used in all proweld equipment are war-
ranted for a period of 3 years.
Under the warranty, the manufacturer reserves the right
to repair or replace, at their option, defective parts which fail
during the guarantee period. Notice of any claim for warranty
repair or replacement must be furnished to the manufacturer
by the purchaser within ten (10) days after the defect is first
discovered. The manufacturer does not assume any liability
for paying shipping cost or any labor or materials furnished
where such cost are not expressly authorized in writing.
The manufacturer does not warrant any parts or acces-
sories against failures resulting from misuse, abuse, improper
installation, maladjustment, or use not in accordance with the
operating instructions furnished by the manufacturer. The
warranty is valid only when studs are purchased from sources
approved by the manufacturer or are of identical specifica-
tions to the manufacturer’s
3.0 UNPACKING YOUR UNIT
Upon receipt of your unit, place it as close as possible to the
point of installation before unpacking it. Once the unit is un-
packed, it is recommended that you inspect it for any physical
damage that may have occurred in shipping.
Your unit has been completely assembled and inspected at
the factory. Upon receipt, the unit must be hooked up to the
recommended incoming power before welding.
Place the unit in a large enough area to provide adequate ven-
tilation. Do not restrict the air flow around the front louvers
or from the fan at the rear of the unit. Do not allow water to
enter the unit in any way.
4.0 SUGGESTED SAFETY PRECAUTIONS
In any welding operation, it is the responsibility of the welder
to observe all safety rules to insure his or her personal safety
and to protect those working in the area.
Reference is directed without endorsement or recommenda-
tion to ANSI Z49.1, Safety in Welding and Cutting, and to
AWG Publication A6,1-66, Recommended Safe Practices for
Gas-Shielded Arc Welding.
4.1 Personal Safety Precautions
1. Always treat electricity with respect. Under open circuit
conditions, the welding machines output voltage may be dan-
gerous.
2. Don’t work on live circuits or conductors. Disconnect the
main power before checking the machine or performing any
maintenance or repair operations.
3. Be sure the welding machine cabinet is properly grounded
to a good electrical ground. Consult local electrical codes.
4. Never operate a welder in the rain, or operate a welder
while standing in water. Avoid wearing wet or sweaty clothes
when welding.
5. Don’t operate with worn or poorly connected cables, and
don’t operate the weld gun with loose cable connections. In-
spect all cables frequently for insulation failures, exposed
wires, loose connections and repair as needed.
6. Don’t overload welding cables or continue to operate with
over heated cables.
7. Don’t weld near flammable materials or liquids in or near
the area, or on ducts or pipes carrying explosive gases.
8. Don’t weld on containers which have held combustible or
flammable materials, or on materials which give off flamma-
ble or toxic vapors when heated.
PAGE 1
Summary of Contents for ARC 656-575 VERSION
Page 1: ...OPERATION MAINTENANCE MANUAL 575V ERSIO N ...
Page 2: ......
Page 4: ...ARC 656 PRO WELD ...
Page 5: ...ARC 656 PRO WELD ...
Page 6: ...ARC 656 PRO WELD ...
Page 7: ...ARC 656 PRO WELD ...