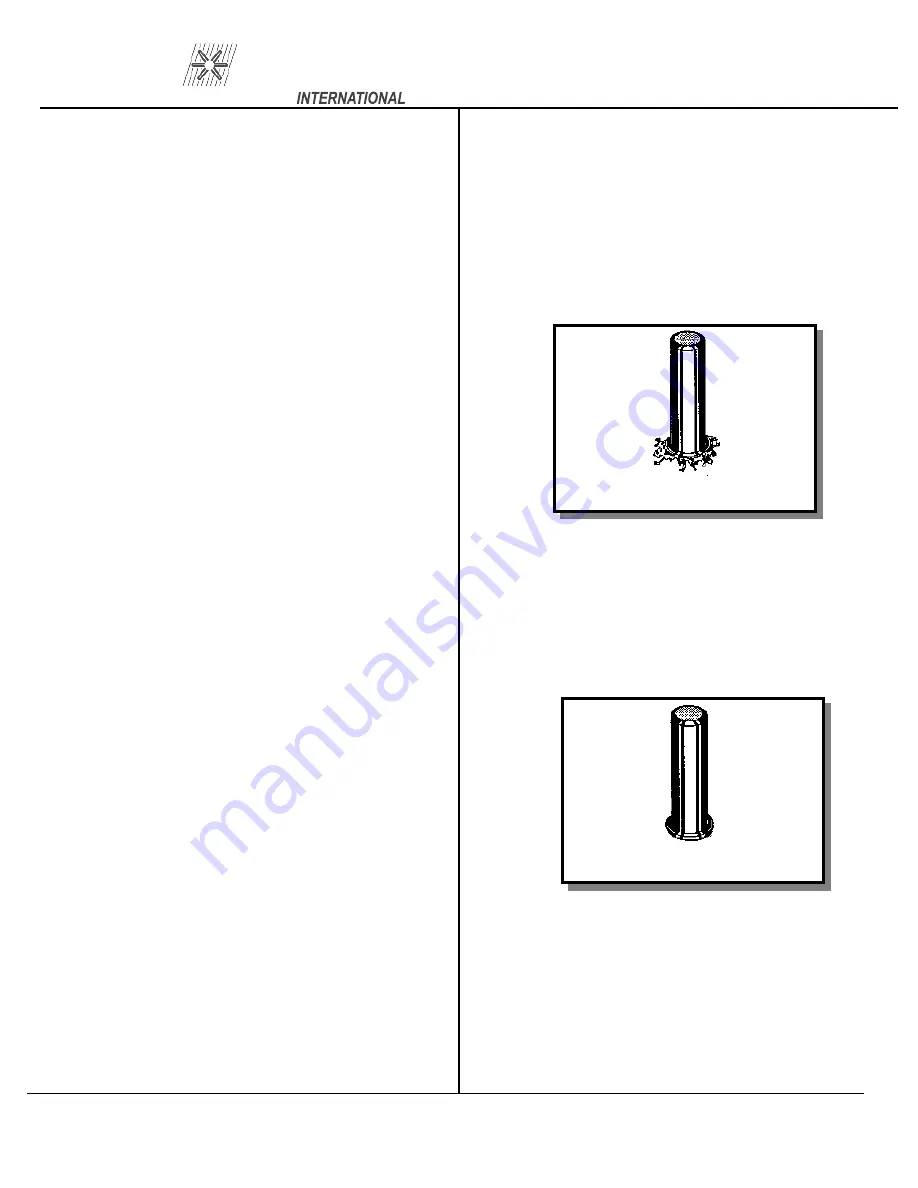
CD -2 1 2
PRO WEL D
13.0 CAUSE OF POOR OR ERRATIC
WELDS
1. Loose collet. Does not grip stud tightly.
(REPLACE) Not enough engagement of stud to col-
let. (CHANGE STOP)
2. Fault or loose ground connection. (REPAIR OR
TIGHTEN)
3. Poor surface condition of base material, excessive
oil, grease, rust, ect. (CLEAN)
4. Voltage or capacitance setting too low or too high.
(ADJUST TO DIAMETER OF STUD)
5. Broken or loose cables. (REPAIR)
6. Dirt in gun. (CLEAN)
7. Incorrect polarity. (CABLES HOOKED-UP
WRONG)
8. Use of center punch or deep scribe. (DO NOT
USE CENTER PUNCH OR DEEP SCRIBES)
9. Cables too closely coiled.
10. Arc blow is evidenced by “one side” welds. In
severe cases there will be no melting under one edge
of flange while the opposite side is gouged out or
appears excessively hot. The principle cause of arc
blow is magnetic field induced by the current flow
during the weld. It occurs most often on long, nar-
row strips of metal or near edges of sheets or plates.
In some cases, a change in grounding positions, or
two grounds on the work piece, one at each end or
edge of work, will correct the problem. For assis-
tance in severe cases, contact your local sales repre-
sentative.
11. Incorrect plunge setting. (ADJUST TO PROPER
SETTING)
12. Incorrect spring. (REPLACE WITH PROPER
SPRING)
13. Poor stud quality.
14.0 TROUBLE SHOOTING POOR
WELDS
Figure 10 Weld too Hot
Figure 11 Weld too Cold
Weld too Hot
A) Decrease voltage.
B) Decrease capacitance.
C) Increase stud protrusion.
D) Increase spring pressure.
Weld too Cold
A) Increase voltage.
B) Increase capacitance.
C) Decrease stud protrusion.
D) Decrease spring pressure.
Page 13
Summary of Contents for CD-212
Page 1: ...OPERATION MAINTENANCE MANUAL ...
Page 2: ......
Page 5: ...CD 212 PRO WELD ...
Page 6: ...CD 212 PRO WELD ...
Page 7: ...CD 212 PRO WELD ...
Page 8: ...CD 212 PRO WELD ...
Page 18: ...CD 212 PRO WELD Figure 9 Light Duty CD Gun Page 10 ...
Page 29: ......