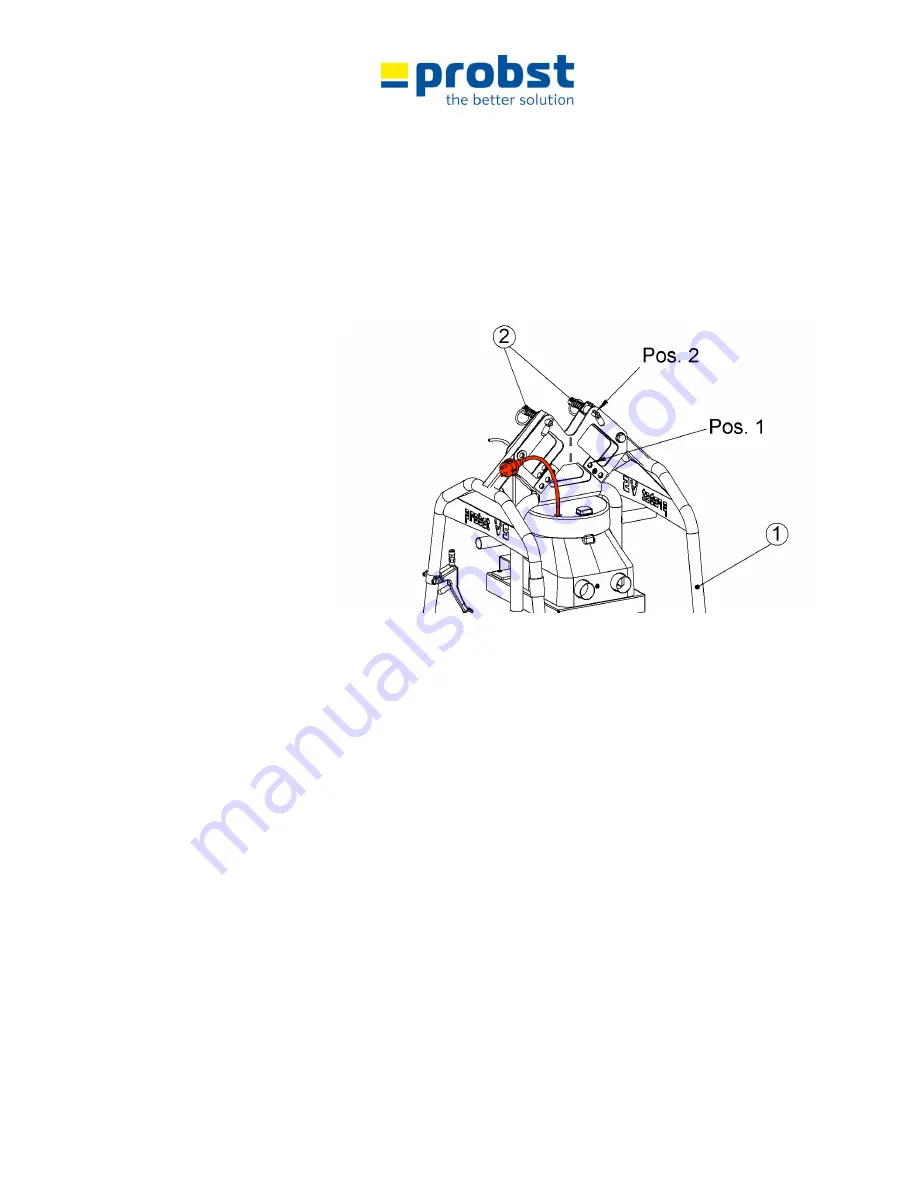
Installation
VS-140-110
V2
06/08/14
15 / 24
6.2
Switching off at the
end of the day
Before switching off the device with the push switch, allow it to run for at least 30
seconds with the venting valve open
This loosens and removes any dirt which may have been deposited on the vacuum
blower.
For
transport
, swing the operator handles (1) down as follows:
remove the spring clips (2) from the pins, pull out the pins, move the handles to the
transport position (
Pos. 2
), insert the pins and secure them with the spring clips.
This lifts the suction pad from the ground, protecting it from damage during transport.
Transport position