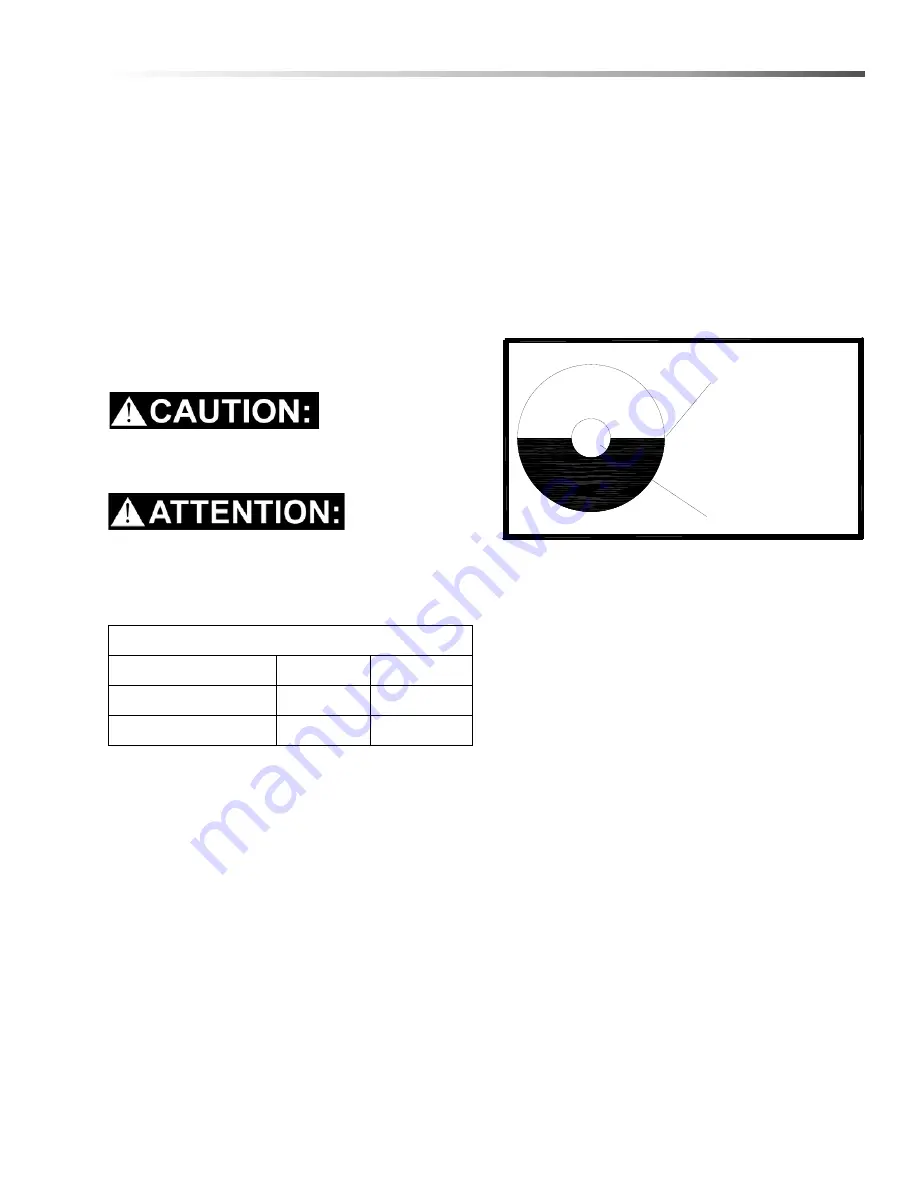
49
Maintenance
Vacuum Pump Drive Belts
To tighten the vacuum pump belts:
1.
Loosen the four bolts that hold the adjusting plate
to the frame and the 2 bolts at the back of the belt
guard.
2.
Turn the adjusting bolts until the proper belt tension
is achieved (1/4" deflection in the center of the belt,
halfway between the pulleys).
3.
Retighten all bolts previously loosened.
NOTE: When adjusting belt tension, make certain
that the engine shaft and vacuum pump shaft remain
parallel, and the belt tension is equal on both belts.
4.
Check belt alignment with straightedge.
Make certain that when you re-torque these screws,
that you use a clockwise pattern and continue until
proper torque is achieved.
S'assurer, au moment de resserrer ces vis,
d'utiliser un mouvement de rotation dans le sens
des aiguilles d'une montre et de continuer jusqu'à
ce que le couple souhaité soit atteint.
5.
Check for pulley groove wear, clean belts and
pulley grooves, check for worn belts, proper belt
tension, and pulley alignment after the first 25
hours and then again at 100 hours.
Check for belt ride in the groove.
Solution Pump
Refer to the Solution Pump Operation and Service
Manual for specific instructions.
1.
Check the crankcase oil level daily to assure the
proper level. Use the illustration as a guide when
checking the oil level. If the level has dropped,
check for the source of leakage and repair.
2.
Remove yellow filler cap with attached dipstick. Oil
level should be between marks on the dipstick or
use the sight glass located on the non-shaft side of
the pump.
3.
Change the crankcase oil with GP Pump
Crankcase Oil, after the first 50 hours of operation.
Drain and refill the crankcase oil with General
Pump Crankcase Oil every 500 hours thereafter.
Oil capacity is 40.6 ounces.
TORQUE VALUES
COMPONENT
INCH/LBS
FOOT/LBS
Engine pulley
360
30
Vacuum pump hub
300
25
RED DOT
OIL LEVEL
WITH UNIT
STOPPED &
ON LEVEL
GROUND
86411100 Manual Operators - Everest E-Idle Prochem