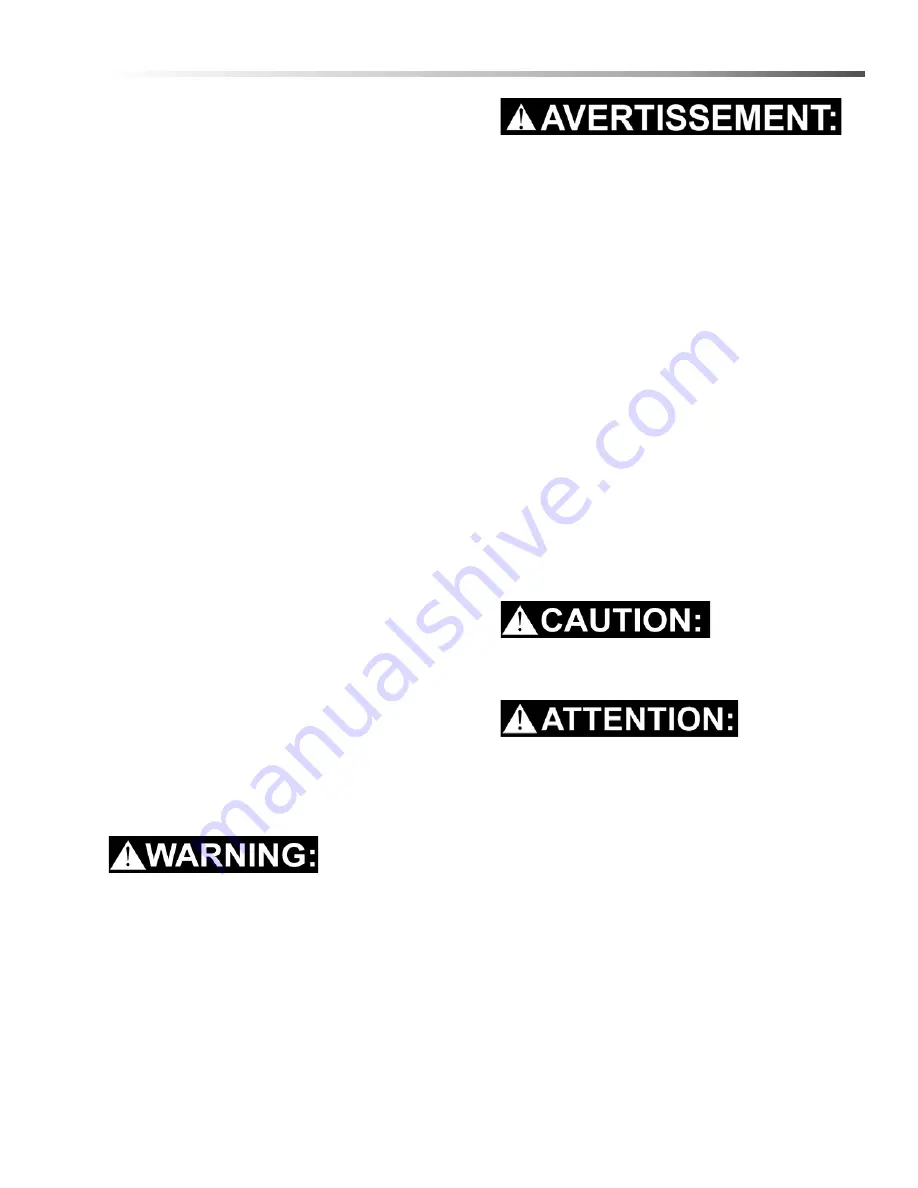
51
Maintenance
Check Valve (Outlet)
Inspect the check valve when rebuilding the chemical
pump or as needed. Remove and disassemble the
check valve. Check the Teflon seat for debris or
abnormal wear. Clean or replace seat if needed.
NOTE: Improper seating of the check valve poppet,
damaged spring, or o-rings will cause poor operation
of the chemical system.
For the procedure, see the "General Service Adjust-
ments" section in this manual for details.
Chemical Pump
Rebuild the chemical pump every 500 hours. This
involves changing the diaphragm, plastic disk, and
check valves.
For the procedure, see the "General Service Adjust-
ments" section in this manual for details.
NOTE: Inspect chemical inlet tube strainer daily.
Pressure Regulator
Lubricate the o-rings every 100 hours. Use o-ring lubri-
cant.
For the procedure, see the "General Service Adjust-
ments" section in this manual for details.
Vacuum Hoses
To assure maximum hose life, we recommend that the
hoses be washed out with clean water at the end of
each working day.
High Pressure Solution Hoses
Inspect your high pressure solution hoses for wear after
the first 100 hours of use. Inspect every 25 hours there-
after. If hoses show any signs of damage or impending
rupture, replace the hose.
DO NOT attempt to repair high pressure hoses!
Repairing high pressure hoses may result in severe
burns and serious injury!
All high pressure solution hoses must be rated for
3000 PSI at 250°F. Thermoplastic hoses do not meet
these specifications and should not be used. Severe
burns and injury may result if the hoses do not meet
these requirements. Pressure wash hoses must be
rated at 4000 PSI.
NE PAS tenter de réparer les flexibles à solution à
haute pression! Tenter de réparer des flexibles à
solution à haute pression pourrait causer des
brûlures et des blessures graves!
All high pressure solution hoses must be rated for
3000 PSI at 250°F. Thermoplastic hoses do not meet
these specifications and should not be used. Severe
burns and injury may result if the hoses do not meet
these requirements. Pressure wash hoses must be
rated at 4000 PSI.
Optional Waste Pump-Out
At the end of each work day, make certain that you remove
any debris or sediment which may be inside the waste
pump by pumping fresh water through the pump.
Engine Coolant Replacement
The coolant should be replaced every 2 years. This
coolant is an integral part of the heating system and needs
to be maintained as any other working part of the system.
We recommend that this procedure be accomplished by
the following steps.
Draining Coolant:
1.
Add 5/16" hose onto the radiator drain petcock. Turn
counter clockwise to open and drain coolant.
Be sure that used coolant is collected in a proper
container and disposed of in accordance with local
laws.
S'assurer que le liquide de refroidissement usé est
récupéré dans un contenant approprié et éliminé
conformément aux lois locales.
2.
After draining is complete, close the radiator petcock.
Replacing Coolant:
1.
Fill radiator with 50/50 anti-freeze water mix.
2.
Start unit and run on low speed.
3.
As the unit warms up, maintain a full radiator with a
50/50 mix.
4.
Open petcock slightly on helicoil to allow any trapped
air to escape. When coolant runs out of helicoil, close
petcock.
5.
Top off radiator with 50/50 coolant mix.
6.
Re-install radiator cap.
7.
Shutdown unit.
8.
Check radiator overflow bottle. Add coolant to proper
"cold" level.
86411100 Manual Operators - Everest E-Idle Prochem