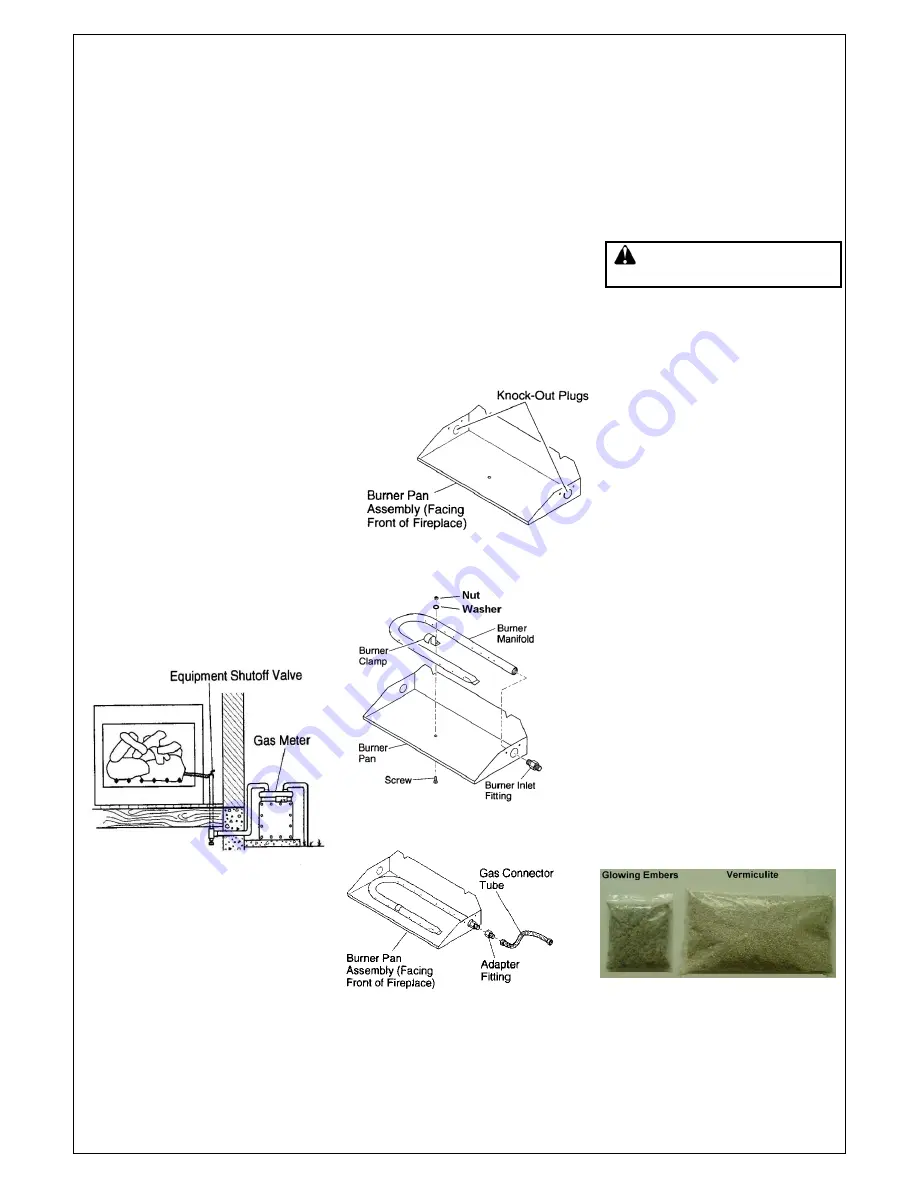
PRO-COM OWNER’S MANUAL
VENTED GAS LOGS 5 WAL21-01
Figure 8- Connecting Gas to Appliance
Figure 9- Glowing Embers and
Vermiculite
Figure 5 –Checking Gas Joints
Test Pressures Equal To or Less Than
1/2 PSIG (3.5 kPa)
1. Close equipment shutoff valve (see
Figure 5).
2. Pressurize supply piping system by
either using compressed air or opening
main gas valve located on or near gas
meter.
3. Check all joints from gas meter to
equipment shutoff valve (see Figure
5). Apply mixture of liquid soap and
water to gas joints. Bubbles forming
show a leak.
4.
Correct all leaks immediately.
ADDING PAN MATERIAL
1. Open the bag of ash bed material
(vermiculite) and spread it evenly
across the burner pan to the top. You
may over-flow the front and sides of the
pan to cover the entire pan and
connecting hardware. Do not cover
control system valve.
2. Open the glowing embers and evenly
cover the ash bed material (vermiculite)
in the burner pan.
Pressure Testing Gas Supply
Piping System
Test Pressures In Excess Of 1/2 PSIG
(3.5 kPa)
1. Disconnect appliance with its appliance
main gas valve (control valve) and
equipment shutoff valve from gas supply
piping system. Pressures in excess of
1/2psig will damage heater regulator.
2. Cap off open end of gas pipe where
equipment shutoff valve was connected.
3. Pressurize supply piping system by either
using compressed air or opening main
gas valve located on or near gas meter.
4. Check all joints of gas supply piping
system. Apply mixture of liquid soap and
water to gas joints. Bubbles forming show
a leak.
5. Correct all leaks immediately.
6.Reconnect log set and equipment shutoff
valve to gas supply. Check reconnected
fittings for leaks.
TESTING BURNER FOR LEAKS
1. Generously apply soapy solution to
all connections.
2. Light the burner with the shutoff
valve, no more than half open, and
holding a match slightly in front of the
pan (see Lighting Instructions, page 6).
3. Inspect all connections for bubbles,
raw gas odor, or flame from any area
other than the burner (leaks). If leaks
are detected, shut off the gas valve
immediately. Tighten, or reassemble
the loose connection(s) using pipe joint
compound until burner system is leak
free.
4. When the burner is tested and leak
free, observe the individual tongues of
flame on the burner.
Note
: The burner
design includes more ports on the
outside of the bar. Make sure that all
ports are clear and producing flame
evenly across the burner. If any ports
appear blocked, clear them by
removing the burner manifold and
reaming the ports with a modified
paper clip or other suitable tool.
5. When finished testing, turn the gas
shutoff valve OFF to extinguish all
flames.
INSTALLATION
Continued
Installation and Gas Connection
1. Place the burner pan assembly in
the center of the fireplace floor. Make
sure the front of pan faces forward.
2. Thread the gas supply fitting to the
fireplace gas supply pipe. Use thread
sealant.
3. Install adapter fitting onto the burner
inlet fitting using thread sealant on
male threads of burner inlet fitting
(see Figure 8).
4. Install the gas connector tube to the
gas supply fitting. Carefully shape
tube to attach to adapter fitting.
WARNING:
Never check
for gas leaks with open flame.
INSTALLING THE GRATE, LOGS
See Page 10-15 Logs installation
HEARTH KIT ASSEMBLY
AND INSTALLATION
Kit Assembly
Note:
The following instructions
apply to dual flame "U" style
burners. Be sure all pipe threaded
connections are tight, and have
thread compound to prevent leaks.
1. Determine which side the gas line
will be coming into the fireplace.
2. Using a hammer and screw driver,
remove knock-out plug from the side
of the pan that corresponds to the
gas line (see Figure 6).
3. Unscrew burner inlet fitting from
burner manifold (see Figure 7).
4. Place burner manifold in pan with
threaded opening facing open
knock-out plug.
5. Using thread sealant (resistant to the
action of natural gas) on larger end of
fitting, screw the burner inlet fitting
through hole and into burner manifold.
Tighten using a wrench.
6. Using burner clamp, screw, and nut
provided, assemble clamp to pan.
This will hold the burner manifold in
place.
7. If using optional control system kit,
follow instructions included with kit for
installation and operation.
Figure 6 – Knock-Out Plug Locations
Figure 7 – Installing Burner