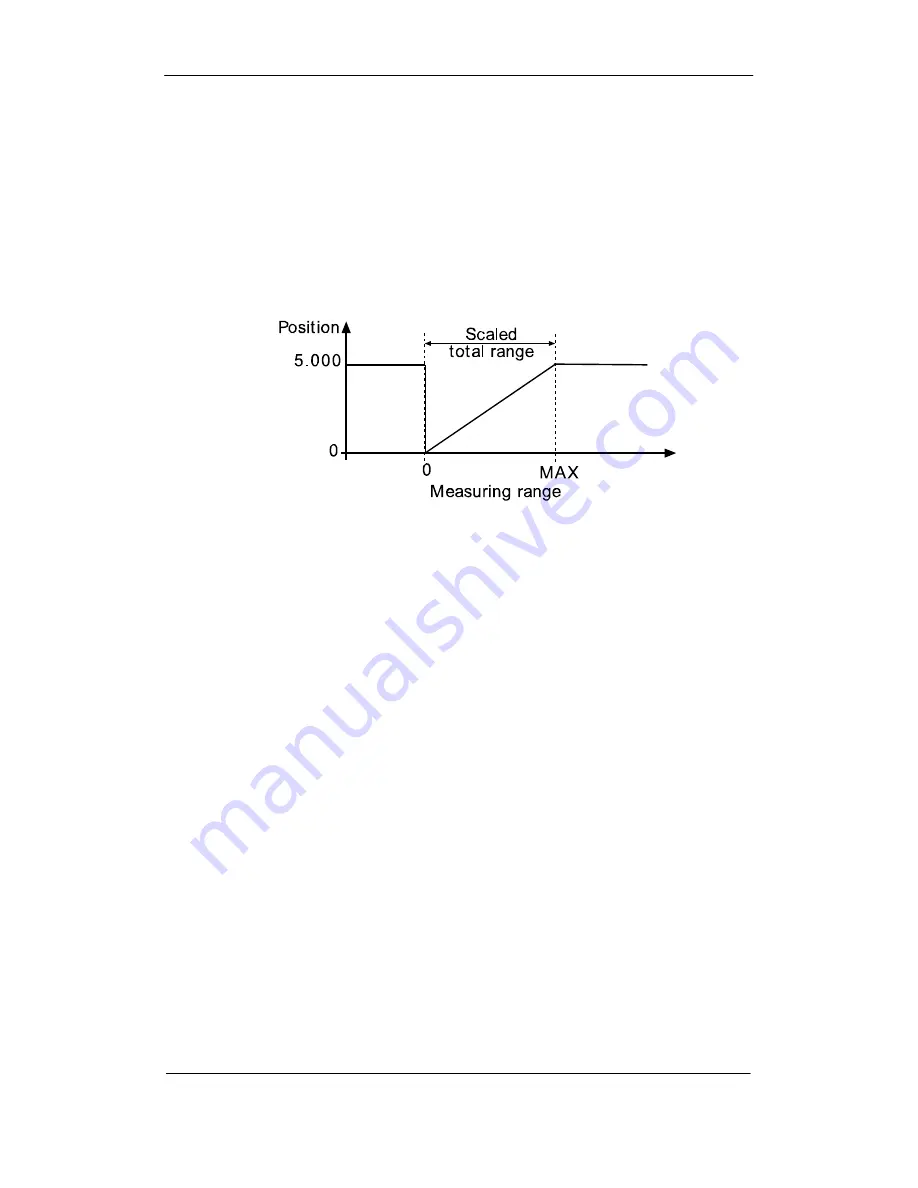
PROFIBUS USER MANUAL Leine & Linde AB
Part Id: 740590-01
25
Document Id: 740590 Ver. 01
Publication date: 2010-06-01
B. Non-cyclic operation
If the measuring range is used to limit the encoder value range to a value not equal to
the specified singleturn resolution * 2
x
, the output position value is limited within the
operating range. If the position value increases or decreases outside the measuring
range by rotating the encoder shaft beyond the maximum value or below 0, the device
outputs the total measuring range value.
Example of non-cyclic scaling:
Measuring units per revolution
= 100
Total measuring range
= 5000 (number of revolutions 50)
Picture 15 Non-cyclic scaling