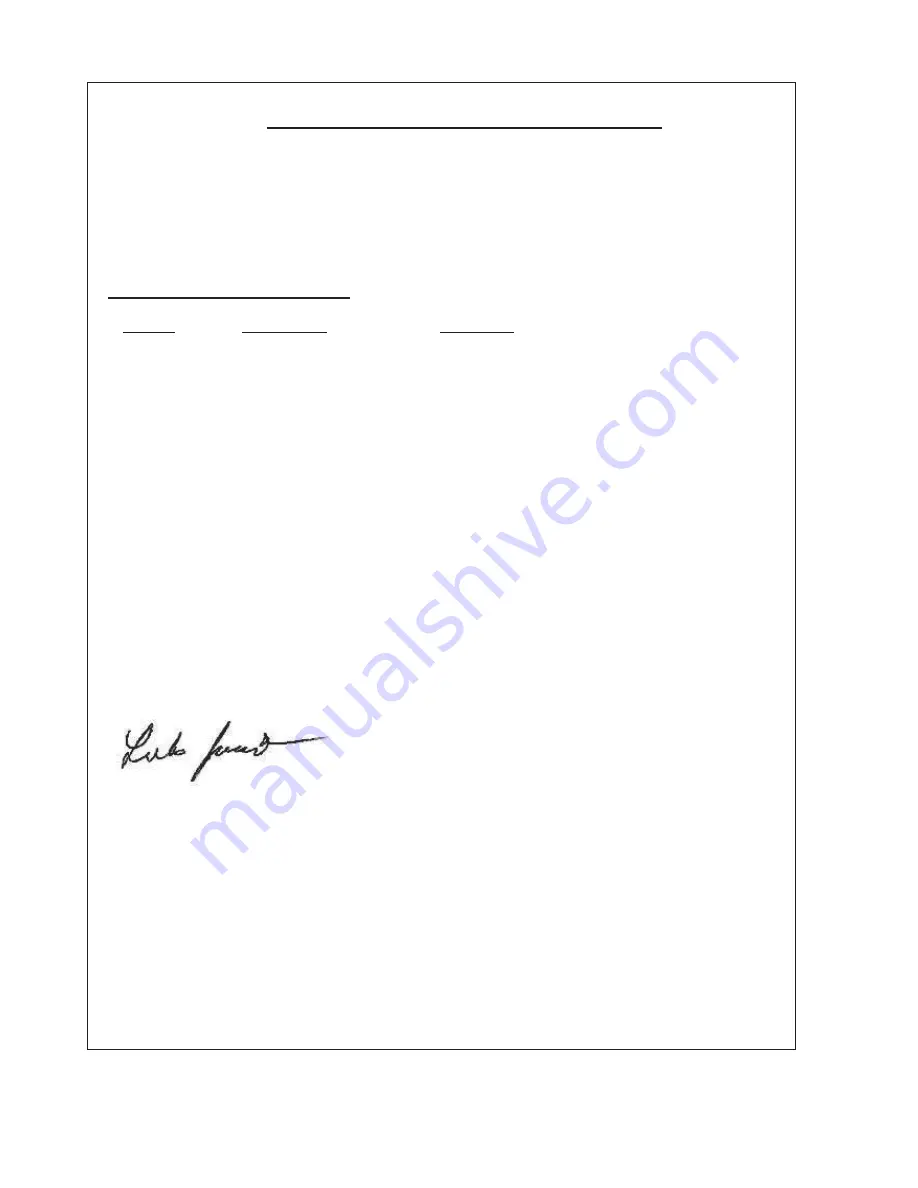
4
DECLARATION OF CONFORMITY
According to Annex 11 A of the European Community Regulation for Machines
We, Progressive Turf Equipment Inc. 137 West William Street, Box 940, Seaforth Ontario, Canada declare
under our sole responsibility that:
Progressive Rotary Finishing Mowers
Models:
Part Number
Description
TD65-2
526512D
3.66m Tri-Deck Finishing Mower
TD65
526515D
4.72m Tri-Deck Finishing Mower
TD92
529222E
6.70m Tri-Deck Finishing Mower
PF-120
601205D
3.05m Pro-Flex Contour Mower
PFR-120
601205RD
3.05m Pro-Flex Roller Contour Mower
PM-36
529236E
10.97m Pro-Max 36 Mowing System
TDR-22
526924E
6.70m Tri-Deck Roller Mower
TDR-15
528750D
4.72m Tri-Deck Roller Mower
TDR-12
528712D
3.65m Tri-Deck Roller Mower
SDR-65
531965C
165cm Three Point Hitch Roller Mower
SDR-90
531990C
228.6cm Three Point Hitch Roller Mower
are in conformity with Directive 98/37/EC of the European Parliament and of the Council of 22 June, 1998
on the approximation of the laws of the member states relating to Machinery.
The Technical Construction File is maintained at the corporate offices of Progressive Turf Equipment Inc.
at the address listed above.
Dated at Seaforth, Ontario Canada the 28
th
day of February 2013.
Luke Janmaat
President
Progressive Turf Equipment Inc.
Summary of Contents for 1212029
Page 2: ...3 ...
Page 4: ...5 ...
Page 36: ...33 ...
Page 38: ...BLADE SPINDLE ASSEMBLY 2 1 2 3 4 6 7 8 9 10 11 12 14 15 17 13 16 5 ...
Page 40: ...2 3 4 5 6 8 9 10 11 15 16 17 16 15 18 19 1 22 23 REAR DECK ASSEMBLY 21 20 12 7 14 13 24 4 ...
Page 44: ...GEARBOX MOUNT ASSEMBLY 1 3 4 5 6 7 9 10 12 11 8 2 13 8 ...
Page 46: ...3 2 4 5 13 12 14 15 10 5 16 7 11 WING ASSEMBLY 10 1 11 17 9 3 6 8 7 ...
Page 52: ...HYDRAULICS ASSEMBLY 1 2 3 4 5 18 8 9 10 11 14 11 17 16 15 14 13 9 5 12 6 7 6 19 5 10 16 20 ...
Page 54: ......
Page 56: ...20 DECK GEARBOX REAR DECK AND RIGHT DECK ...
Page 58: ...22 LEFT DECK GEARBOX ...
Page 60: ...24 4 WAY GEARBOX ASSEMBLY ...
Page 63: ...REAR DECK PTO SHAFT 27 ...
Page 64: ...28 INPUT PTO SHAFT ...
Page 65: ...INPUT PTO SHAFT B MODELS TDR 15 SERIAL 1215102B AND UP TDR 12 SERIAL 1312031B AND UP 29 ...
Page 66: ......