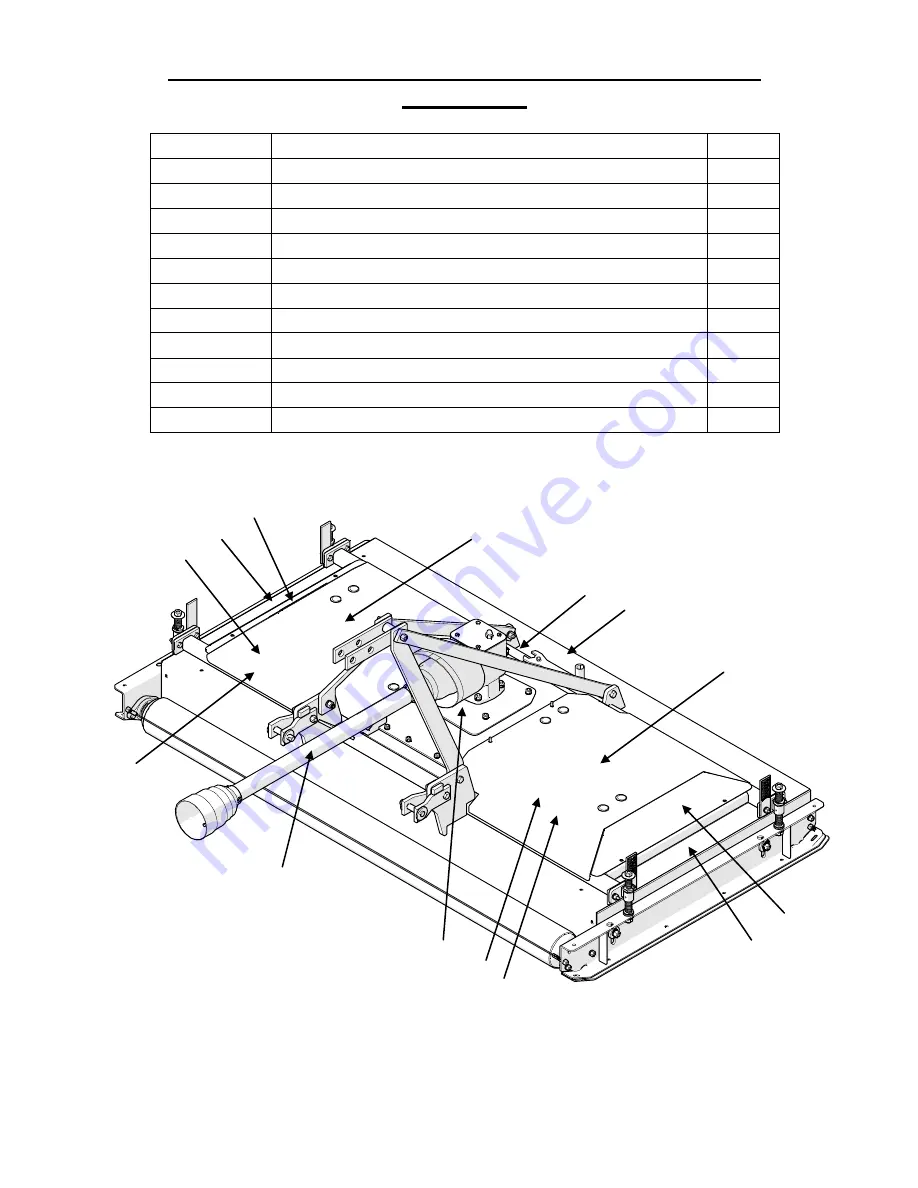
8
SAFETY & MAINTENANCE DECAL LOCATIONS ON
MACHINE
:
ITEM NO.
DESCRIPTION
QTY
1
DANGER – READ MANUAL
1
2
CAUTION – REPLACE SHIELDS
2
3
DANGER – BLADE HAZARD
3
4
WARNING – OEM PARTS
1
5
CAUTION – DISENGAGE PTO
1
6
PTO GREASING
1
7
COMPANY NAME
1
8
MOWER MODEL
2
9
DANGER – OUTER TUBE
1
10
DANGER – OUTER SHIELD
1
11
DECAL - PRO-EZ BLADE HARDWARE
1
3
3
3
6
2
2
4
1
7
8
8
5
9
10
11
Summary of Contents for SDR 65
Page 2: ......
Page 3: ...1 ...
Page 5: ...3 ...
Page 12: ...10 ITEM 9 ITEM 10 521451 521455 ITEM 11 SDR 65 ITEM 11 SDR 90 209182 209196 ...
Page 32: ...30 ...
Page 38: ...SDR 90 Parts Manual 2 1 DECK ASSEMBLY 1 1 Blade Spindle Assembly ...
Page 39: ...SDR 90 Parts Manual 3 1 2 Blade Options ...
Page 40: ...SDR 90 Parts Manual 4 1 3 Gear Box Mount ...
Page 41: ...SDR 90 Parts Manual 5 1 4 Deck Assemblies ...
Page 42: ...SDR 90 Parts Manual 6 1 5 Deck Drive ...
Page 43: ...SDR 90 Parts Manual 7 1 6 Deck Roller 2 2018 ...
Page 44: ...SDR 90 Parts Manual 8 1 7 Belt Drive Assembly Rear ...
Page 45: ...SDR 90 Parts Manual 9 2 FRAME ASSEMBLY 2 1 3 PT Hitch Linkage ...