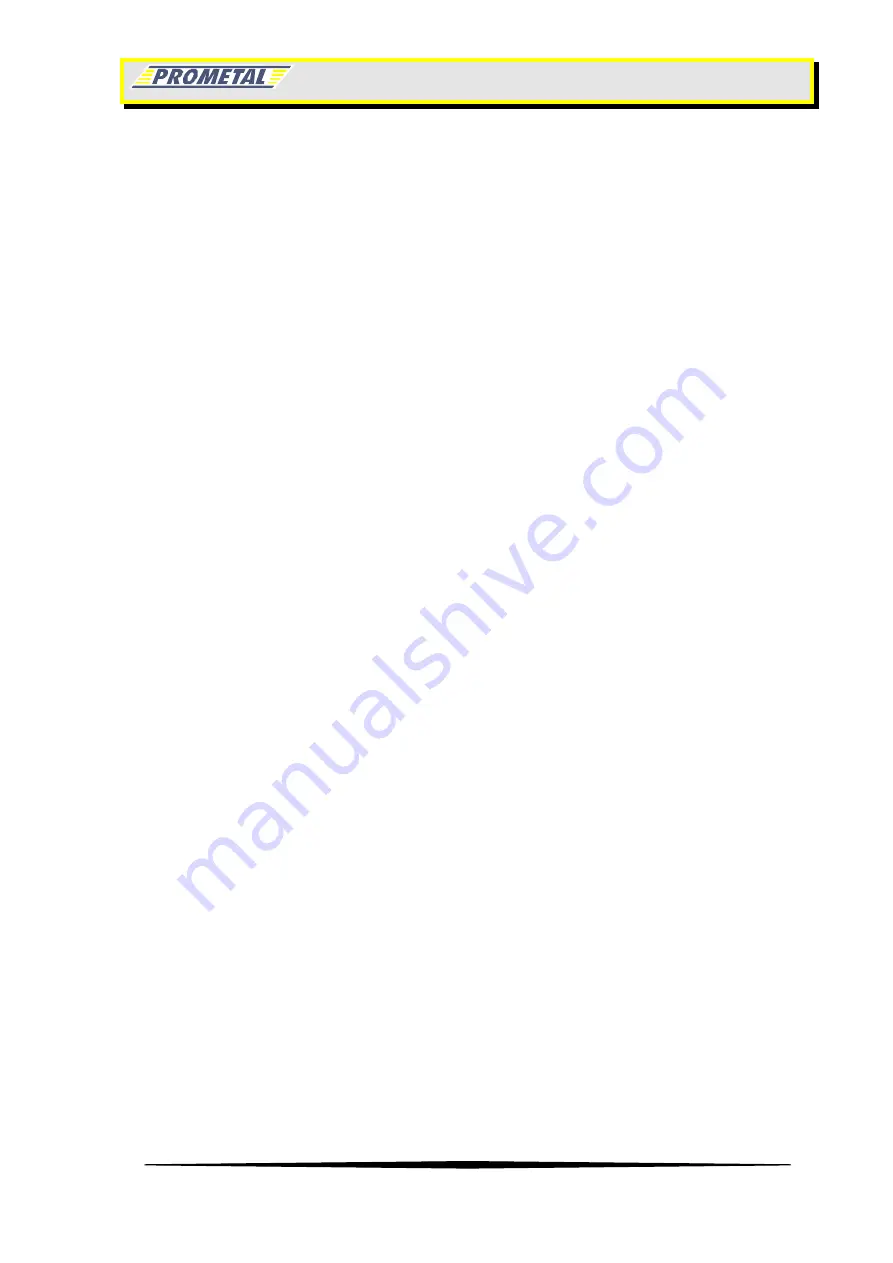
Maintenance manual Universal-1000
P R O M E T A L
29
- Foaming in tank
- Pressurized fluid
Experience has shown that errors are often made and insufficient care taken when inspecting
the pressurized fluid despite the fact that its condition is a quick and reliable pointer to the
condition of the hydraulic system.
The pressurized fluid is one of the most important elements in a hydraulic system and
performs a number of tasks. In addition to the familiar inspection items, namely:
- Level in tank
- Discoloration (milky, dark, foamy)
- Temperature in tank
which are to be constantly monitored, it is necessary to perform further checks. Assessment of
the pressurized fluid and any changes from the condition when new makes it possible to
recognise irregularities in the hydraulic system at an early stage before they can result in
machine damage.
-Maintenance of hydraulic components-
Experience has shown that 80 % of faults/damage in hydraulic oil systems are due to selection
of the wrong oil and poor oil condition
.
Pumps, valves and motors are maintenance-free. Maintenance work is therefore concentrated
on oil checks and filter element replacement. Maintenance intervals depend on the system
concerned and are governed by operating conditions and applications.
-Pressurized fluid-
- Always use filters when topping up pressurized fluid (filter mesh as for service filter).
- Bypass filtering with mobile filter unit is to be employed for additional conditioning of the
fluid fills.
- Pressurized fluid with non-monitored fills is to be replaced every 1000 - 5000 operating
hours, however at least once a year or in line with results of laboratory test. Shorter oil
change intervals are to be envisaged in the case of installation subject to high thermal load.
- Clean oil tank whenever oil is changed.
- Always use filters when filling. Filter unit must at least correspond to service filter. Mobile
manual or electrically operated pump filter units have proven to be appropriate.
Summary of Contents for UNIVERSAL 1000
Page 19: ...Maintenance manual Universal 1000 P R O M E T A L 19 ...
Page 25: ...Maintenance manual Universal 1000 P R O M E T A L 25 Hydraulic system ...
Page 26: ...Maintenance manual Universal 1000 P R O M E T A L 26 ...
Page 52: ...Maintenance manual Universal 1000 P R O M E T A L 52 Now lower down tamper head and mould ...
Page 53: ...Maintenance manual Universal 1000 P R O M E T A L 53 Pull out cart with mould on itself ...
Page 58: ...Maintenance manual Universal 1000 P R O M E T A L 58 After adjustment is done ...
Page 65: ...Maintenance manual Universal 1000 P R O M E T A L 65 Vibrator table maintenance ...