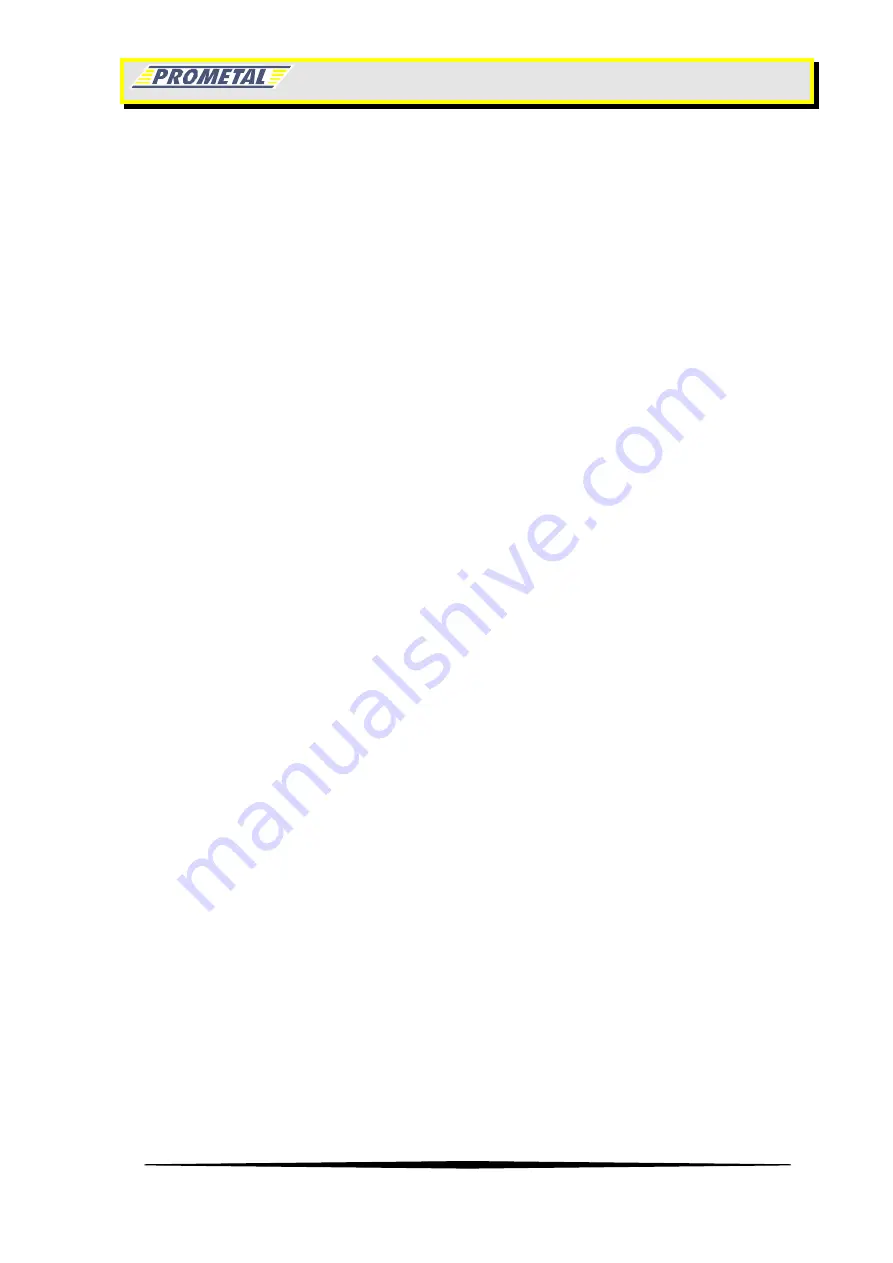
Maintenance manual Universal-1000
P R O M E T A L
18
return springs for brake shoes if these are severely worn. Brake shoes must move freely to
permit rapid release of the tamper head.
-Mould and tamper head mounting-
The hard chromium-plated columns are to be checked for damage and can be turned if
necessary (from bottom to top). Whether or not the gunmetal bearing shells need replacing
can be seen during production. In this case, there will be a gap between column and bearing
such that the tamper head can oscillate even in its upper position. Scraper rings are likewise to
be changed on replacing bearings.Check tightness of bronze wear strips on end faces of filler-
box tables. Secure loose strips; renew if damaged or severely worn. Check scraper plates of
filler-box tables and replace if necessary.
Check functioning of hopper outlets. Renew worn bolts and bronze bushings in mount. If
level indicators are fitted, check cables for damage and renew if necessary.
-Hydraulic drive-
Perform first filter change after installation/commissioning, however at the latest if the gauge
on the housing cover is in the yellow zone. This likewise applies to subsequent operation.
Eliminate any leaks. The plunger rod gaskets are to be renewed in the event of leakage at the
plunger rods of the hydraulic cylinders. Tighten loose pipe clamps, as otherwise switching
impact in the hydraulic system could overload the pipe unions and cause them to brake off.
Always keep oil cooler away from dust. It is appropriate to clean it at frequent intervals with
compressed air so as to maintain the cooling capacity. The best temperature range for
hydraulic oil is approximately 40°C - 65°C. The temperature of the hydraulic oil should never
bebelow 15°C or above 70°C, as pump damage could occur outside this range.
-Electrical system-
Make sure the electrical system has been de-energized before working on it. Switch off main
switch. Work on the electrical system is only to be performed by a qualified electrician.
Practice has shown that it is difficult to keep switch cabinets completely free from dust.
Electrical devices and switching contacts thus become dusty. It is appropriate to blow out the
electrical devices and switchgear at regular intervals with clean, dry air. Contact cleaning
spray is a good solution if devices are heavily contaminated. It is beneficial to retighten the
terminal studs during the initial period. This likewise applies to those at contactors, including
terminals which are not being used. Loose screws can drop out and cause damage. Clean
cooling fins and cooling-air slots on electric motors on a regular basis. Never use fuses with a
higher rating than those stated.
Summary of Contents for UNIVERSAL 1000
Page 19: ...Maintenance manual Universal 1000 P R O M E T A L 19 ...
Page 25: ...Maintenance manual Universal 1000 P R O M E T A L 25 Hydraulic system ...
Page 26: ...Maintenance manual Universal 1000 P R O M E T A L 26 ...
Page 52: ...Maintenance manual Universal 1000 P R O M E T A L 52 Now lower down tamper head and mould ...
Page 53: ...Maintenance manual Universal 1000 P R O M E T A L 53 Pull out cart with mould on itself ...
Page 58: ...Maintenance manual Universal 1000 P R O M E T A L 58 After adjustment is done ...
Page 65: ...Maintenance manual Universal 1000 P R O M E T A L 65 Vibrator table maintenance ...