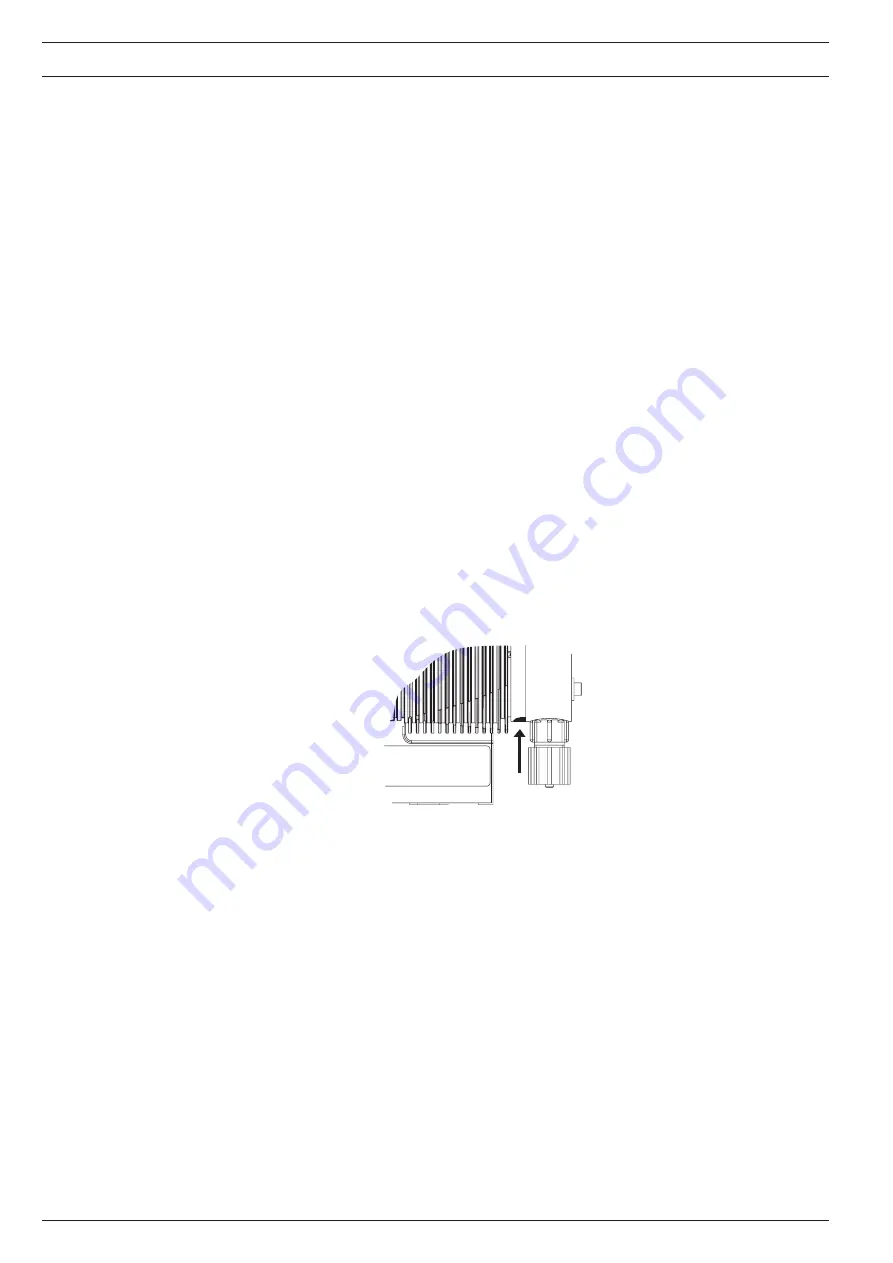
Pr
o
Minent
®
Page 28
Maintenance / Repairs
10
Maintenance
Maintenance intervals
•
Every quarter, when subject to normal usage (continuous operation - approx. 30 % )
•
Shorter intervals when subject to heavier usage (e.g. continuous operation)
Maintenance actions
Standard liquid ends:
S
Check the diaphragm for damage (see section 11)
S
Check chemical seepage at vent hole
S
Check that the discharge tubing is connected firmly to the liquid end
S
Check that discharge and suction valves are firmly fixed
S
Check that the liquid end is generally watertight (especially vent hole! See fig. 24)
S
Check for correct feed: run the gamma/ L run for a short period (press both arrow keys
together)
S
Check electrical connections for wear
S
Check that liquid end screws are fastened tightly (on coarse/fine bleeding versions, first
remove knob and cover
Screw fastening torque:
Liquid end dia. 70 mm:
2,5 to 3 Nm
Liquid end dia. 90 mm and dia. 100 mm:
4,5 to 5 Nm
GUIDELINE
•
For PP liquid end, check fastening torque every quarter!
Additionally, for liquid ends with coarse/fine bleed function and SEK type:
•
Check that the bypass tubing is connected firmly to the liquid end
•
Check that the bleed valve is firmly fixed in place
•
Examine the discharge and bypass tubing for kinks
•
Check that the coarse/fine bleed function is working correctly
Fig. 24
Vent hole
11
Repairs
GUIDELINE
Repair work that may be carried out by authorised personnel only, or on factory
premises:
•
Replacement of damaged mains cables
•
Replacement of fuses and electronic controller.
Please contact your nearest ProMinent branch or representative!
When sending the pump for repair make sure it is clean and that the liquid end has
been thoroughly rinsed out (see section 13)! If, despite careful emptying and
cleaning, safety precautions are still required for handling the gamma/ L, the
necessary information must be entered in the safety declaration!
The safety declaration is a component of the inspection/repair order.
An inspection or repair can only be carried out when a safety declaration has been
correctly and completely filled out by an authorised and qualified member of staff
from the company operating the pump.
A form is included in the appendix.