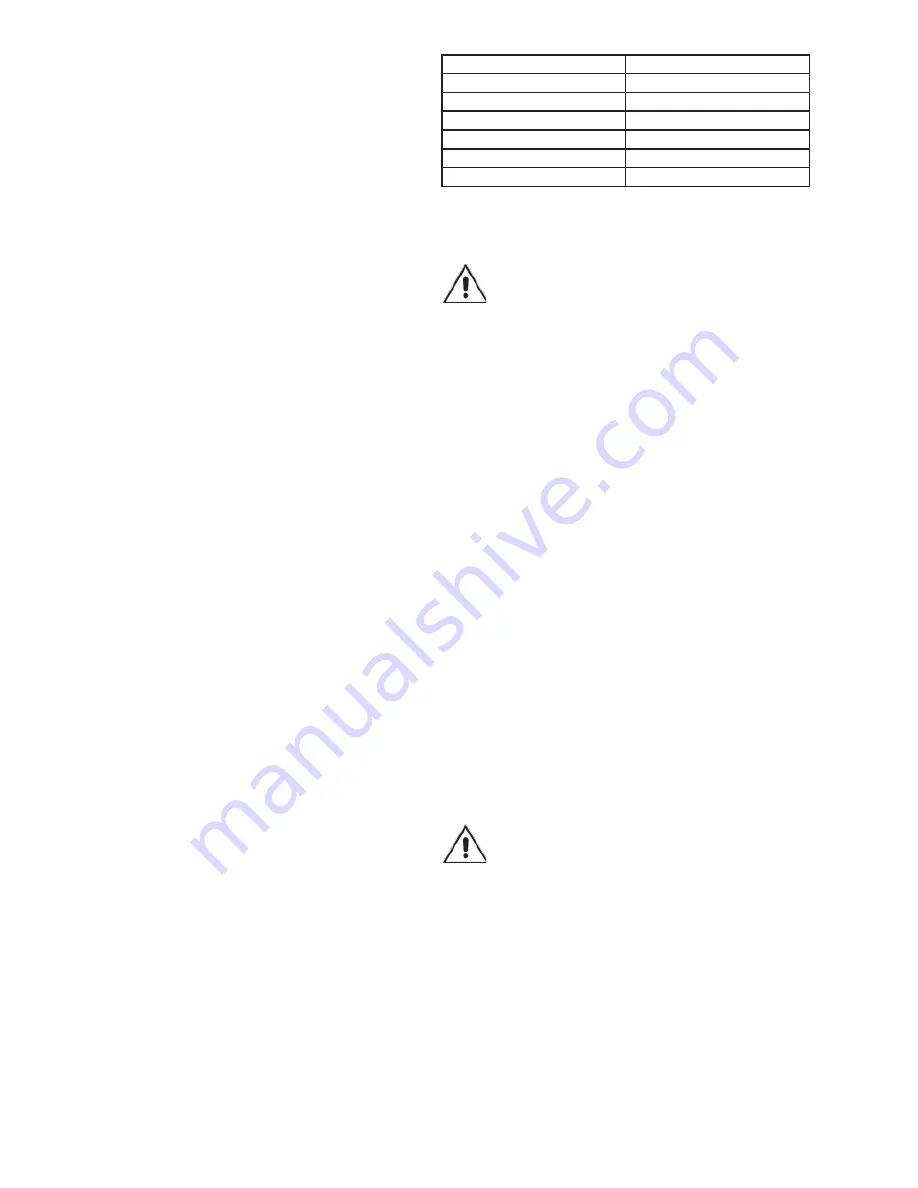
6
SECTION B: GENERAL INFORMATION
B-1) To the Purchaser:
Congratulations! You are the owner of one of the fi nest
pumps on the market today. These pumps are products
engineered and manufactured of high quality components.
Over one hundred years of pump building experience
along with a continuing quality assurance program combine
to produce a pump which will stand up to the toughest
applications.
This manual will provide helpful information concerning
installation, maintenance, and proper service guidelines.
B-2) Receiving:
Upon receiving the pump, it should be inspected for
damage or shortages. If damage has occurred, fi le a claim
immediately with the company that delivered the pump. If
the manual is removed from the packaging, do not lose or
misplace.
B-3) Storage:
Short Term
- Prosser Pumps are manufactured for effi cient
performance following short inoperative periods in storage.
For best results, pumps can be retained in storage, as factory
assembled, in a dry atmosphere with constant temperatures
for up to six (6) months.
Long Term
- Any length of time exceeding six (6) months, but
not more than twenty four (24) months. The units should be
stored in a temperature controlled area, a roofed over walled
enclosure that provides protection from the elements (rain,
snow, wind-blown dust, etc.), and whose temperature can be
maintained b40 deg. F and +120 deg. F.
If extended high humidity is expected to be a problem, all
exposed parts should be inspected before storage and all
surfaces should then be sprayed with a rust-inhibiting oil.
Pump should be stored in its original shipping container.
On initial start up, rotate impeller by hand to assure seal
and impeller rotate freely. If it is required that the pump be
installed and tested before the long term storage begins, such
installation will be allowed provided:
1.) The pump is not installed under water for more than
one (1) month.
2.) Immediately upon satisfactory completion of the test,
the pump is removed, thoroughly dried, repacked in
the original shipping container, and placed in a
temperature controlled storage area.
B-4) Service Centers:
For the location of the nearest Prosser Service Center, check
your Prosser representative or Crane Pumps & Systems, Inc.,
Service Department in Piqua, Ohio, telephone (937) 778-8947
or Crane Pumps & Systems Canada, Bramton, Ontario,
(905) 457-6223.
SECTION C: BEFORE STARTING:
1. Fill oil reservoir to the top of the sight glass with a good
grade of hydraulic oil with anti-wear additives. Use oils
recommended below (minimum viscosity of 150SSU @ 100
Deg. F. (38 Deg. C.) or their equivalent:
SUPPLIER
GRADE
Pennzoil
Hydraulic Oil No. 46
Texaco
Rando HDAZ
Shell
Tellas Hydraulic Oils
Mobil
D.T.E. 20 Series
Chevron
EP Hydraulic Oils
Exxon
J-58 Hydraulic Oil
NOTE: WHEN USING THIS EQUIPMENT IN
ENVIRONMENTALLY SENSITIVE AREAS WE
RECOMMEND USING AN OIL SUCH AS THE
MOBIL EAL 224H.
NOTE: WHEN USING THIS EQUIPMENT IN
HIGH TEMPERATURE ENVIRONMENTS WE
RECOMMEND USING DEXRON AUTOMATIC
TRANSMISSION FLUID.
2. Fill fuel tank with clean gasoline as per engine
manufacturers recommendations. (see Engine Manual).
3. Check engine oil (See engine instruction manual for correct
oil for each climate).
4. Connect hydraulic hoses from power unit to equipment
to be powered. Be sure to completely connect the hydraulic
couplings or damage will result to the hydraulic system.
Pressure and return hoses cannot be connected incorrectly
because the couplings are incompatible. Always be sure the
connections are clean before assembling.
5. Turn control valve counter-clockwise until handle rotates
freely. This de-energizes the hydraulic system to permit easy
starting of engine and also allows you to turn off the hydraulic
system without stopping the engine.
SECTION D: STARTING PROCEDURE:
1. Start engine at low speed and allow several minutes for
warm up. (See engine manual).
2. Turn control valve clockwise until it stops. This energizes the
hydraulic system. Check operation and/or rotation of device
being powered. If correct, increase engine speed to achieve
desired output.
NOTE: IF MAXIMUM PERFORMANCE IS NOT
REQUIRED, IT IS BEST TO SLOW ENGINE SPEED
TO MEET THE NEEDED FLOW. THIS SAVES FUEL
AND EXTENDS THE LIFE OF THE EQUIPMENT.
SECTION E: STOPPING PROCEDURE:
1. To stop the power unit, decrease engine speed and
de-energize the hydraulic system.
2. To stop the engine, turn switch to the off position.
3. After initially starting the system, check the hydraulic oil level
in the reservoir. Filling the hoses initially will cause the level to
drop slightly.
Summary of Contents for PHD13G
Page 10: ...10 FIGURE 2 Model PHD13G...
Page 11: ...11 FIGURE 3 Model PHD13G FIGURE 4...
Page 14: ...14 FIGURE 5 Model PHD20G FIGURE 6...
Page 15: ...15 FIGURE 7 Model PHD20G...