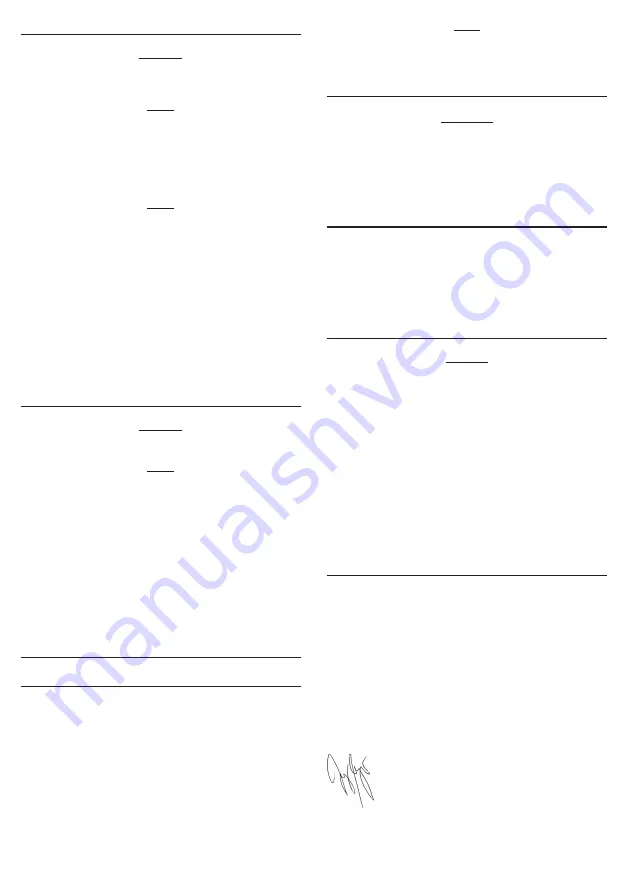
- 7 -
Set spindle speed
Caution!
Unplug drill before performing this operation! Never ope-
rate drill without protective cover.
Note:
Optimal performance results from uniform, correct speed
and not from excessive pressure.
Belt position “A” (Fig. 2)
= 1,080 rpm.
Belt position “B”
= 2,400 rpm.
Belt position “C”
= 4,500 rpm.
Note:
Once the belt is properly tensioned (between motor axle
and drill spindle), you should be able to easily re-position
it by hand. When changing speed, it is not necessary to
re-tension the belt.
1. Unscrew knurled bolt 2 (Fig. 1) and remove cover
hood 3.
2. Rotate belt pulley while pressing belt in direction of
smaller diameter until belt has been released.
3. Position belt onto smaller diameter for desired speed.
4. Rotate other belt pulley, while pulling belt onto large dia-
meter until seated properly for smooth function.
5. Install cover hood. Tighten knurled bolt 2.
Adjusting belt tension
Caution!
Unplug drill before performing this operation!
Note:
When changing drill speed, it is not necessary to re-tension
the belt.
Tension belt no tighter than necessary, i.e., tighten until
there is no more slack. An over-tensioned belt distends
over longer periods of inactivity and reduces motor output.
1. Unscrew knurled bolt 2 (Fig. 1) and remove cover
hood 3.
2. Loosen both bolts 1 (Fig. 3) by one rotation.
3. Using a screwdriver, lever out the motor to the rear
(Fig. 3) until the desired belt tension has been attained.
4. Tighten both bolts.
5. Install cover hood. Tighten knurled bolt 2 (Fig. 1).
Adjusting distance between bit and
workpiece
In addition to using the centre sleeve lift (drill lift), you can
set the TBH bench drill to the desired height via a quick-
adjustment crank mechanism (70 mm). Adjusting the drill
height does not displace the drill spindle centre mark
above the bench surface. In addition, the complete unit
can be moved to any position along the drill column.
Crank mechanism height adjustment:
1. Loosen knurled bolts 10 (Fig. 1).
2. Adjust extension arm to desired height using crank 12.
3. Tighten knurled bolts.
Note:
Tighten knurled bolts to eliminate unnecessary stress on
mechanism when drilling
Re-positioning complete extension arm
Important!
Secure extension arm against falling.
1. Release knurled bolts 10 (Fig. 1) and knurled bolt 9.
2. Move complete extension arm to desired position.
3. Re-tighten knurled bolts.
Utilising depth stop
Proceed as follows to adjust the max. drilling depth:
1. Loosen locking bolt 8 (Fig. 1).
2. Lower drill spindle until bit contacts workpiece.
3. Set desired drilling depth on dial 7 and re-tighten locking
bolt.
Maintenance
Caution!
Unplug drill before performing any maintenance
operations.
• Lubricate centre sleeve guide (Fig. 3) every 10 operating
hours using a few drops of machine oil.
• Following use, the drill must be thoroughly cleaned using
a whisk or brush to remove all swarf.
• All dirt deposits on the drill must be routinely removed
using a rag.
• During longer periods of inactivity, the drive belt must be
removed to prevent deformation and erratic function.
• If, after it has been in use for a certain time, noises are
heard on touching the tailstock quill, this indicates play in
the tailstock quill, which should be taken up by slightly
tightening the screw, 84 (see exploded drawing, page 30).
EC Declaration of Conformity
We assume sole liability for ensuring that this product con-
forms with the following EC guidelines:
• EC-EMC Guideline 89/336/EEC
• DIN EN 55014-1 / 09.2002
• DIN EN 55014-2 / 08.2002
• DIN EN 61000-3-2 / 12.2001
• DIN EN 61000-3-3 / 2002
• EC Low Voltage Guideline 73/23 EEC; 93/68 EEC
• DIN EN 61029 / 02.2001
• EC Machine Guideline 98/37 EEC
• DIN EN 61029 / 02.2001
Dipl.-Ing. Jörg Wagner
PROXXON S.A.
Equipment Safety Division
WWW.PROXXON.RO