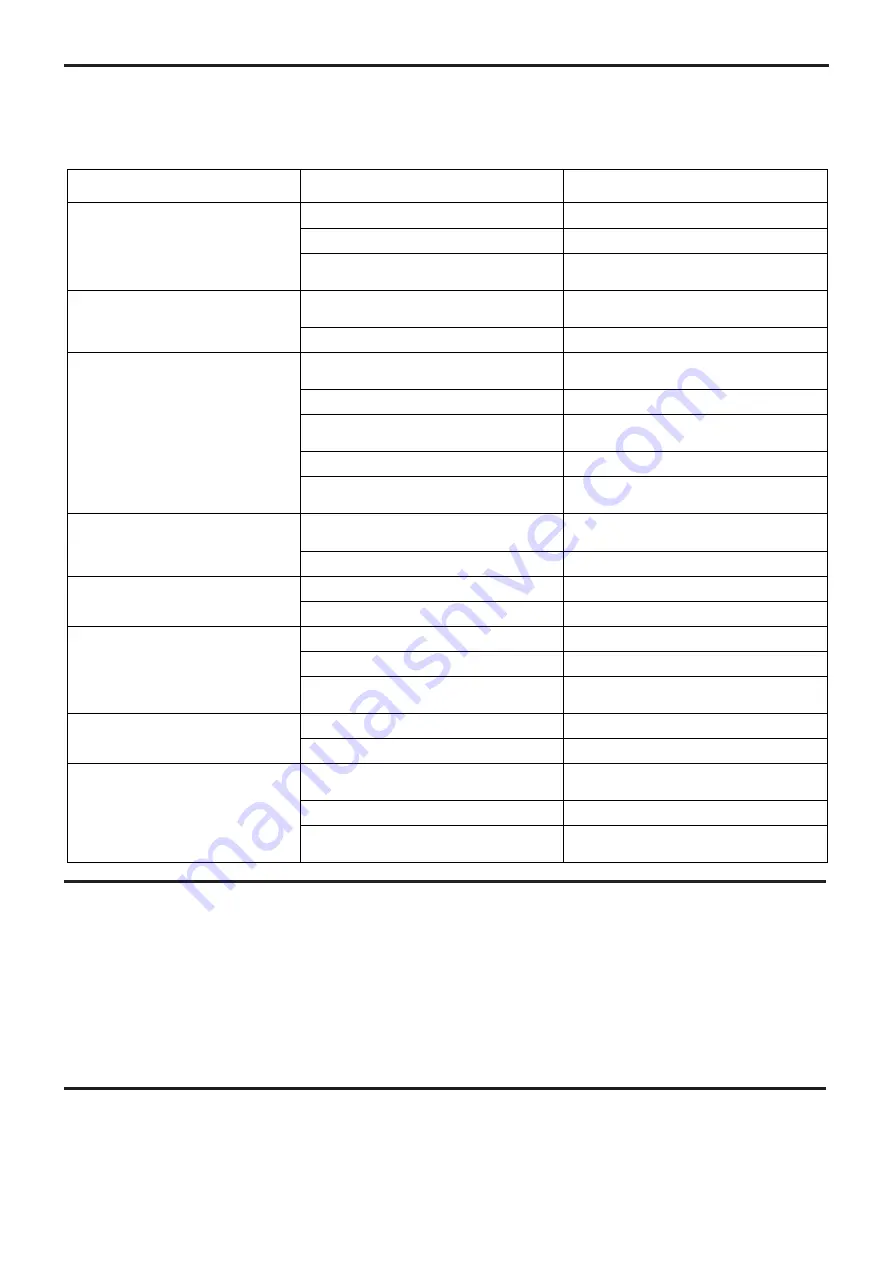
20/22
NT 1401-X00 10 18 B200 Flow Control e
7.1 Compressor
The equipment must be systematically stored in an area
sheltered from bad weather.
The equipment must bear its original protective compo-
nents until it is installed in its final application.
If installation is interrupted, put back in place the original
protective components or equivalent components.
7.2 BSC2 oil
In its unopened original container in a dry, frost-free and
light-free place.
The maximum shelf life is approx. 60 months.
7. STORAGE CONDITIONS
The compressor must be scrapped in compliance with the
regulations in force.
During this operation, particular care must be paid to the drai-
nage stages of the compressor.
8. SCRAPPING
Problem
Possible
ori
g
in
Possible
solution
1.
P
ressure
issue
T
oo
much
pressure
drop.
T
o
chec
k
pipes
diameter.
Relief
v
al
v
e
dama
g
ed.
T
o
chec
k
the
openin
g
point.
N
o
return
v
al
v
e
dama
g
ed.
T
o
chec
k
the
proper
operatin
g
of
the
N
o
return
v
al
v
e.
2.
F
lo
w
rate
issue
W
ron
g
Compressor
speed.
T
o
ad
j
ust
the
speed
b
y
ta
k
in
g
care
of
the
ran
g
e
allo
w
ed.
Relief
v
al
v
e
dama
g
ed.
T
o
chec
k
the
openin
g
point.
3
.
Abnormal
hi
g
h
temperature
Air
filter
clo
gg
ed.
T
o
clean
the
cartrid
g
e
or
to
replace
it.
Air
pressure
too
much
hi
g
h.
T
o
see
problems
1.
/
2.
Outside
temperature
too
much
hi
g
h.
T
o
respect
the
ma
x
imum
e
x
ternal
temperature
allo
w
ed.
L
ac
k
of
oil.
T
o
chec
k
the
oil
le
v
el.
Compressor
speed
too
much
lo
w
.
T
o
ad
j
ust
the
speed
b
y
ta
k
in
g
care
of
the
ran
g
e
allo
w
ed.
4.
Inlet
pressure
drop
> 7
5
mbar
(
Clo
gg
in
g
indicator
red
)
Air
filter
clo
gg
ed.
T
o
clean
the
cartrid
g
e
or
to
replace
it.
Air
inlet
hose
folded.
T
o
chec
k
the
air
inlet
hose.
5.
Compressor
doesn
’
t
operate
T
or
q
ue
limiter
dama
g
ed.
T
o
replace
the
tor
q
ue
limiter.
T
ransmission
dama
g
ed.
T
o
consult
y
our
Ser
v
ice
point.
6.
T
or
q
ue
limiter
dama
g
ed
Scre
w
Compressor
dama
g
ed.
T
o
consult
y
our
Ser
v
ice
point.
W
ron
g
motor
/
transmission
mana
g
ement.
T
o
consult
y
our
T
ruc
k
dealer.
Oil
too
much
v
iscous.
T
o
be
in
compliance
w
ith
the
MO
U
V
EX
Instructions.
7
.
Oil
lea
k
T
oo
much
oil.
T
o
chec
k
the
oil
le
v
el.
Oil
breather
clo
gg
ed.
T
o
clean
the
oil
breather.
8.
Vibrations
W
ron
g
motor
speed.
T
o
increase
the
speed
b
y
ta
k
in
g
care
of
the
ran
g
e
allo
w
ed.
T
ransmission
dama
g
ed.
T
o
chec
k
the
dri
v
in
g
shaft.
L
ac
k
of
ri
g
idit
y
of
the
chassis.
T
o
be
in
compliance
w
ith
the
T
ruc
k
Manufacturer
Instructions.
6. TROUBLESHOOTING
CAUTION :
OBSERVE ALL SAFETY WARNINGS CONTAINED IN THIS MANUAL.