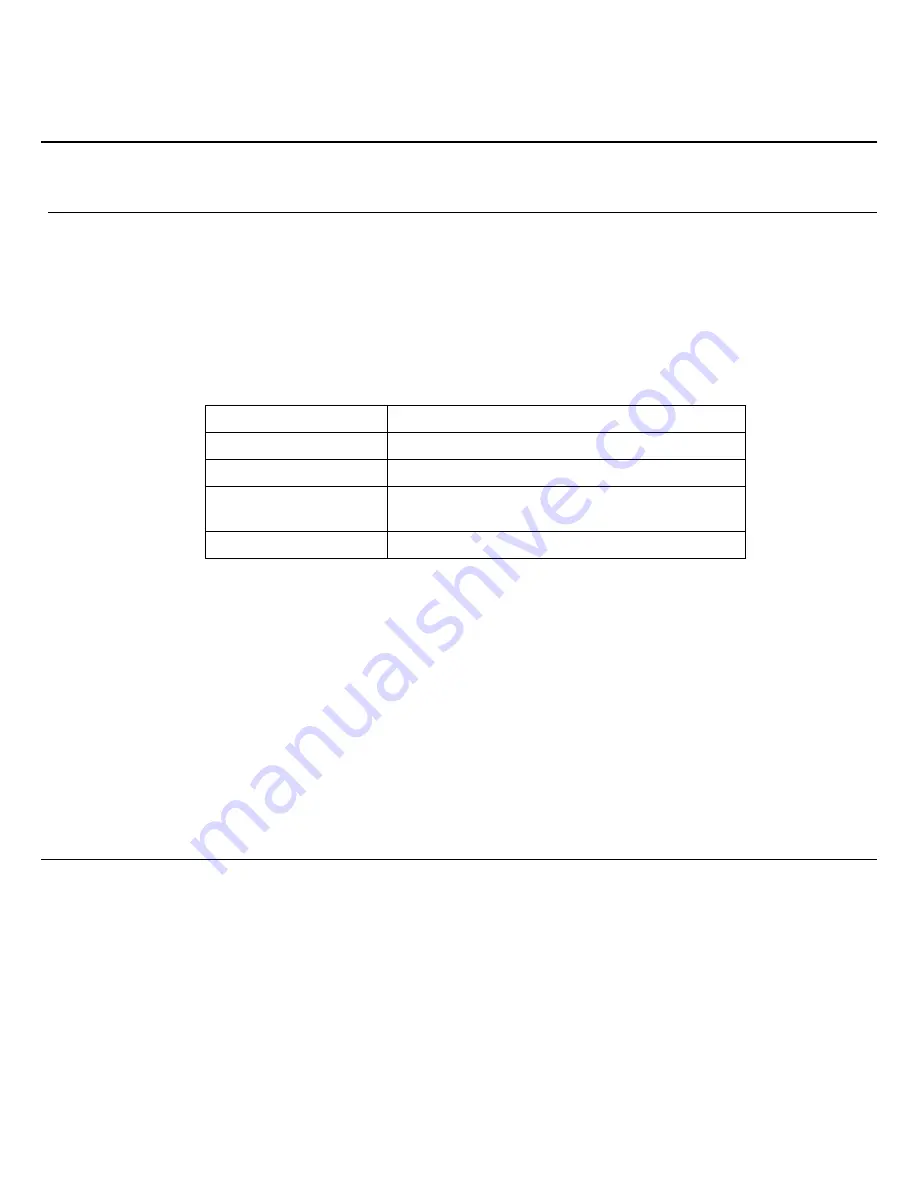
PureAire Monitoring Systems, Inc.
33
5: Maintenance & Calibration
Only qualified personnel should perform maintenance and calibration
.
5.1 Routine Maintenance Schedule
Continuous gas detection systems depended upon to measure and detect hazardous gas leaks in the
workplace requires periodic maintenance to ensure proper operation. The frequency with which this
routine maintenance is required depends on the environment, since temperature, humidity, gas
concentrations, and dust all affect system operation.
The following table is intended to serve as a general guideline for routine maintenance. The
conditions in your application, as well as your organization’s maintenance policies, will ultimately
determine the best routine maintenance schedule for your equipment.
5.1.1 Routine Visual Checks
Item
Status with No Gas Present
Local Display
Display should read “0.0”
4-20 mA Output
Output should be 4 mA
Gas Concentration
Alarm Relays
De-energized (factory default)
System Fault Relay
De-energized (factory default)
5.1.2 Recommended Routine Maintenance Schedule
Routine Visual Checks (flow, fault LED)
Quarterly
Flow rate and power status
Continually supervised. Flow is constantly
monitored and adjusted by the internal CPU
Automatic hourly system integrity verification
Replacement Sensor cell (
p/n 48002
)
Every 2 to 3 years
Sensor Calibration
Every 6 months under normal use
Pyrolizer Filament
( p/n 46003)
Replace when damaged.
Sample Inlet Filter
(p/n 23102)
Replaced when clogged
5.2 Loss of Power Indication
In the event the Air Check Carbonyl Sulfide Monitor loses VDC power, the local display will go
blank and the 4-20 mA analog output signal drops to 0 and the system status alarm relay de-
energizes.
IMPORTANT: If the instrument was in the Measure mode when power was lost, it will
automatically return to the Measure mode when power is restored.