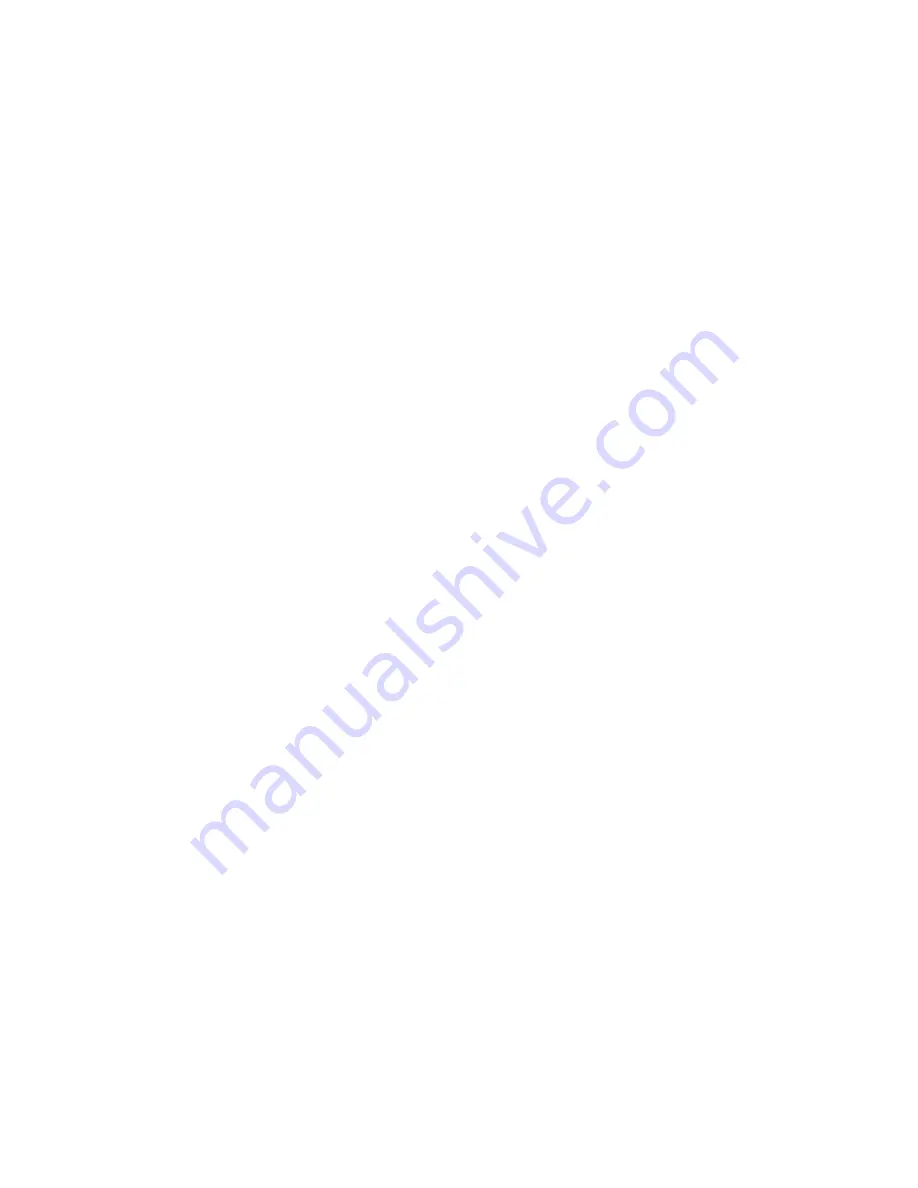
POWER VTX
®
WATER HEATER
39
PV500-68 06/16
14. SEQUENCE OF OPERATION
1. Incoming
120VAC
a. Full time power to the Fuse
b. Full time power to the Main Control Switch
2. Power
On
-
When the main control switch is turned on:
a. 120V is applied to the step-down transformer (24V)
b. 120V is applied to the L.W.C.O. terminal L1 (if used)
c. 24V and 120V is applied to the Platform Ignition Module (PIM). The circulator, blower and HSI circuits are
120V.
d. The PIM performs a processor and memory self-test to insure proper operation. The PIM confirms the
presence of a valid ID card which matches the configuration previously stored in memory. If the valid ID
card is not present, the PIM generates a diagnostic fault. The non-volatile memory is checked for an active
lockout condition. A lockout indicates the previous attempt to light was unsuccessful, or a hi-limit or other
system fault occurred. The PIM stays in lockout until a manual reset is performed.
3. Control Device Pre-check –
The following control circuits are checked for closer before the control system will
initiate a Call for Heat.
a. The PIM continuously monitors the flame status to verify no flame is present during Standby. If an
erroneous flame is detected, the PIM generates a flame error fault.
b. The Electronic Low Water Cut-Off control is a self-contained electronic device which senses the presence
of water at the top of the storage tank. When the presence of water is confirmed, the contacts close on the
ELWCO and is sensed by PIM control.
c. The High Temperature Limit is combined in a common probe body with the upper tank sensor. The PIM will
compare the high limit thermistor temperature with the upper tank thermistor temperature. If the two
temperatures are not the same, a sensor failure will result.
d. When the High Temperature Limit operation has been verified by comparison, the limit temperature will then
be confirmed to be under the maximum allowable temperature.
e. Terminals P1-P2 are closed to activate any connected remote devices
f. The circuit between Terminals C1-C2 is closed by any connected remote proving switches, enabling the
water heater to continue the sequence of operation.
4. Call For Heat -
If the operating control senses that the temperature at the upper tank sensor is below the heater
set point and the previous control interlocks and safeties are satisfied, the following sequence will begin:
a. Terminals P1-P2 are closed to activate any connected remote devices
b. The circuit between Terminals C1-C2 is closed by any connected remote proving switches, enabling the
water heater to continue the sequence of operation.
c. The High Gas Pressure and Low Gas Pressure Switch (if equipped) are energized and their monitored
pressures are proved. The individual safety circuits will close when satisfied and be sensed by the PIM
control.
d. The Airflow-Proving Switch contacts are confirmed to be open before the burner blower is energized.
e. When the burner blower is energized and air pressure is generated, Airflow switch is verified to close within
60 seconds to prove flow.
f. The ignition pre-purge delay takes place.
g. The voltage level of the 24 VAC supply input is confirmed to be above 18.0 VAC.
h. The Ignition cycle begins.