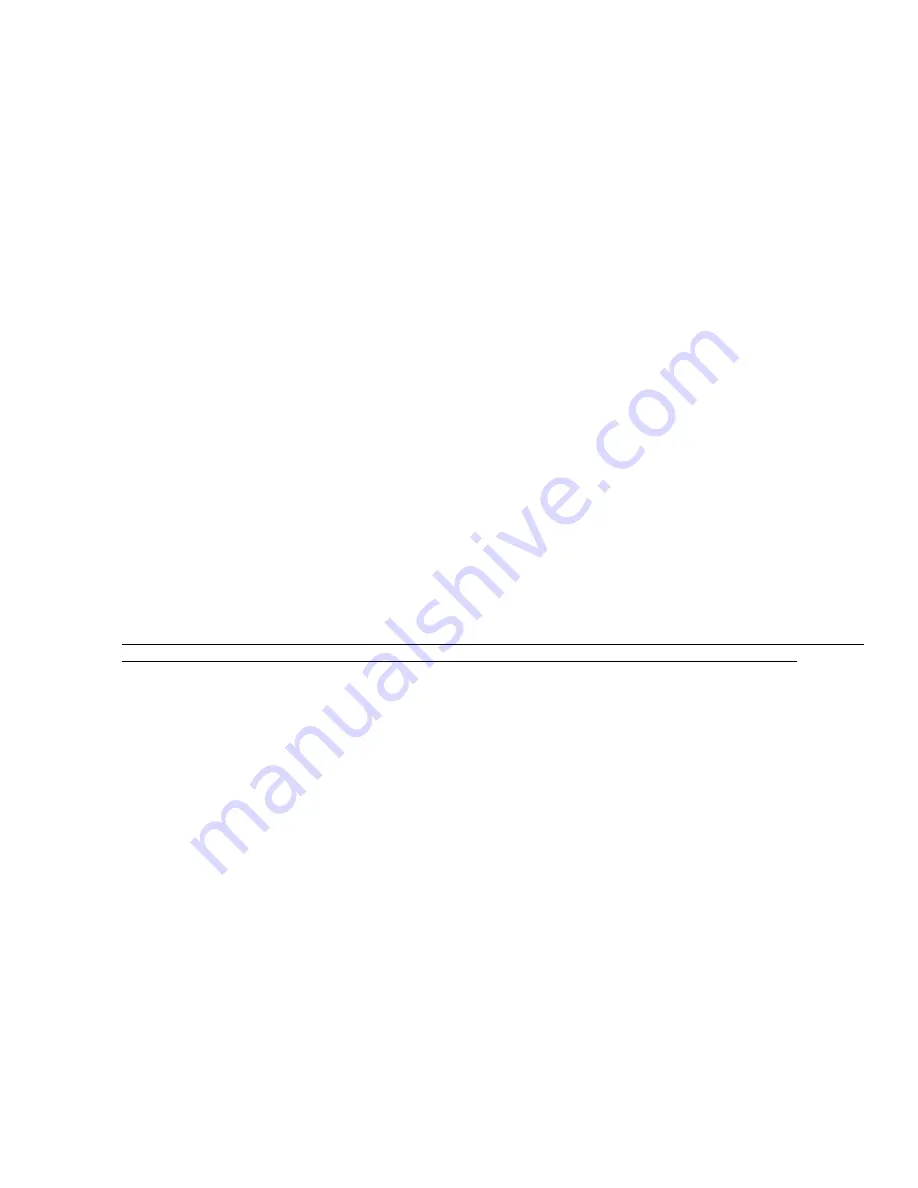
POWER VTX
®
WATER HEATER
42
PV500-68 06/16
3. Be sure all connections into the tank are tight, as leaks at tank fittings will damage the insulation.
CAUTION:
Be sure the tank is filled with water. Dry firing can cause unwarranted damage to the appliance.
4.
CAUTION:
Conduct the following gas train leakage test before start-up, at annual intervals and prior to
investigating the cause of any reported occurrences of delayed ignition.
a. Using an appropriate bubble detection solution, thoroughly coat all gas train pipe connections. If any
bubbles are detected, the leaking connection must be tightened, recoated, and rechecked to assure
stoppage of the leak.
b. Attach a manometer to measure the gas pressure at the manual gas shutoff valve located just upstream of
the gas train. Adjust gas train inlet pressure to the specified value (e.g. 10.5" W.C.), and tightly close the
gas train manual shutoff valve closest to the burner.
c. Reattach the manometer to the gas train manual shutoff valve at the burner and record the measured gas
pressure in inches of water column (W.C.). Measure gas pressure again after 15 minutes. If gas pressure
has increased 0.5" W.C. or more, the gas leak must be isolated to one or more of the operating gas valves.
(For example, a solenoid actuated gas shutoff valve.) After any leaking valve is replaced, the reassembled
gas train must be leak tested again before start-up is attempted.
5. Open the hinged, top enclosure panel cover on the appliance to expose control circuit. A wiring diagram is
attached to the back of this panel.
6. Visually check that all components are intact and no damage has occurred during transit.
7. Check all connections within the control cabinet. A loose connection could cause intermittent shutdowns.
8. The burner uses a hot surface igniter (HSI) as the ignition source. The gas control system may use a single gas
pressure regulator and valves, valve regulator combinations or multiple gas trains.
9. Connect a test meter to the ignition control to read the flame current in microamps.
NOTE
: Some flame controls read the flame signal in micro amps and some in volts DC.
10. Check the inlet gas pressure before start-up, using a manometer or a 0 to 28" W.C. pressure gauge for inlet gas
pressure. (This is the pressure measured before all components in the gas train.) This manometer must stay
connected throughout the testing, as the inlet pressure must be monitored during the firing of the burner.
Record static pressure; it must not exceed 10.5" W.C. Pressures above this could cause damage to the
diaphragm in the gas valve or pressure regulator. The inlet gas pressure must not fall below 3.5” W.C.
11. Connect a second manometer to the manifold test port at the shutoff valve closest to the burner.
12.
Turn-off main gas shutoff valve.
13.
Disable or jumper out any BMS/BAS control interface to allow independent setup and adjustment of
each water heater.
14. Turn unit on using the rocker switch on the front of the control enclosure. When the burner fails to light, the
flame control will lockout.
15.
Turn-on main gas shutoff valve.
16. The Call-for-Heat sequence should initiate and display on the touch screen.
17. If nothing happens, an error or failure message will display indicating that a control interlock or safety control did
not satisfy. Some safety devices such as the Low Water Cut-off, Gas Pressure Switches and the High
Temperature limit will require manual reset after lockout and therefore can be easily identified.
18. When the blower motor starts, the Flame Ignition Control will not be energized until positive air flow is
established and the Remote Proving Interlock, when used, has closed. If the Flame Ignition Control does not
energize, see the troubleshooting guide for help.
19. After the pre-purge, the flame control energizes the HSI for the heat up period, approximately 20 seconds. At
the end of that period the gas valve is opened for approximately 4 seconds. After the burner lights and the
primary safety control senses a flame, the burner will remain on until the call for heat is satisfied or operation is
interrupted by a safety device.