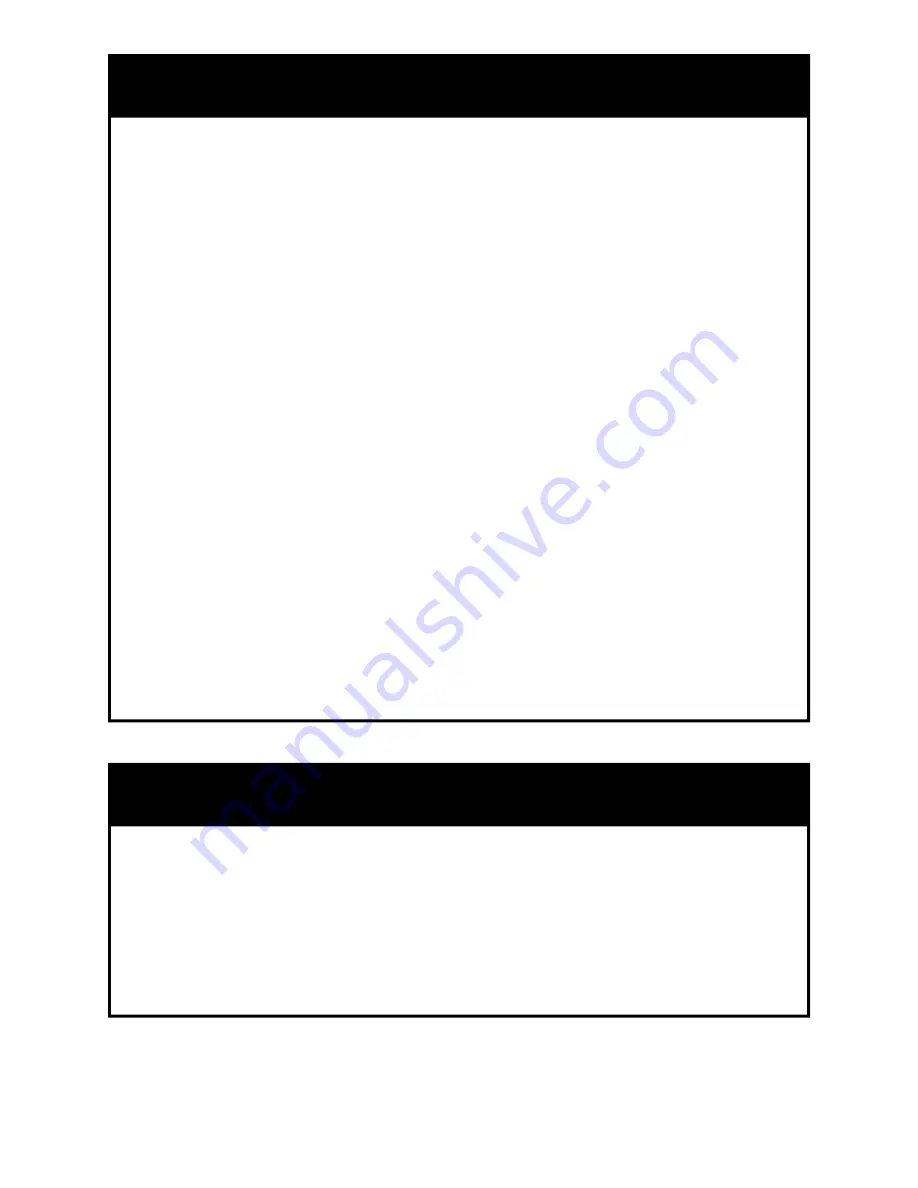
Page 12
SAFETY RELIEF VALVE
1. The safety relief valve should be piped into one of the two upper tapings in the
rear of the boiler
2. The relief valve should be installed using the hardware supplied in the trim kit
without valving between the PRV and the boiler.
3. Pipe the discharge for the safety relief valve with copper tube to within four
inches from the floor to prevent injury in the event or a pressure release. Provide
piping that is the same size as the safety relief valve outlet.
All piping must conform to state and local codes. Page 11 shows the location
and size of the boiler tappings. It is recommended to install unions and gate valves
at the inlet and outlet of the boiler, so it may be readily isolated for service.
For
Canadian
installations, a low water cut off is required if the boiler is
installed above the level of radiation. Even if the boiler is installed below the level of
radiation it is strongly recommended that a low water cut off be installed. Install
manual and/or automatic air venting devices at the high points in the system to
eliminate trapped air. The weight of all piping should be supported by suitable
hangars and floor stands, not by the boiler’s purging/expansion station. Clearance
for hot water pipes are 1 inch to combustibles.
The make-up water line must be
piped into the boiler and be fitted with a backflow preventer and a pressure-
reducing valve to reduce line pressure to 10 to 15 psi.
In the case of a gas installation, the boiler should be installed such that the
gas ignition system components are protected from water (dripping, spraying, etc.)
during appliance operation and service (circulator replacement, condensate trap,
control replacement, etc.).
If the boiler is to be used in conjunction with a chilled water system, it must be
piped with the appropriate valves to ensure the chilled medium does not enter the
boiler. If the boiler is connected to heating coils in an air handling system, where the
coils could be exposed to cold air circulation, provisions for freeze protection control
must be installed. The boiler must have flow control valves or other automatic
means to prevent gravity circulation of the boiler water during the cooling cycle.
NOTE
: If the heating system is to be filled with antifreeze, use only formulations expressly made for
hydronic heating systems (such as propylene glycol).
Do not use automotive types of antifreeze
(ethylene glycol).
Use of antifreeze will alter system output and characteristics. Consult a factory
representative for details or assistance.
5. Piping the Boiler
Summary of Contents for BIASI B10 Series B3-B9
Page 34: ...Page 34...
Page 35: ...Page 35...