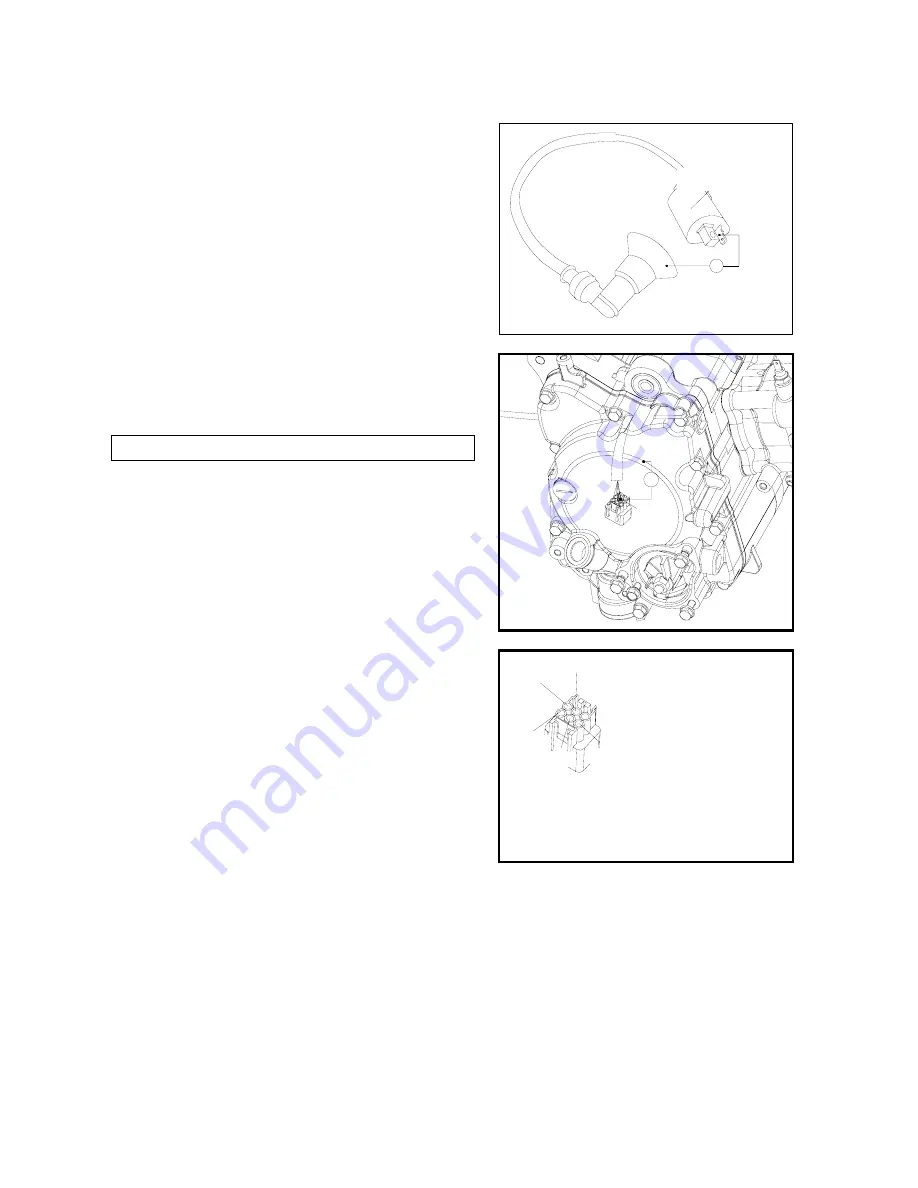
- 46 -
2.5.3 Secondary coil
Measure the resistance value between the wire of spark
plug cover (with the spark plug) and the terminal.
Standard value
:
8-11K
Ω
(
20
℃
)
If the resistance value is within standard value range, the
primary coil is good.
The resistance value "
∞
" stands for broken line in the coil.
Remove the spark plug cover and measure the resistance
value between the primary wire of ignition coil and the
negative terminal.
Standard value
:
4.5-5.5K
Ω
±10
%(
20
℃
)
2.6 Trigger
*Note
Inspection of the trigger can be conducted on the engine.
Inspection
Disassemble the body guard.
Disassemble the lead connector of the trigger.
Measure the resistance value between the blue/white
terminal at the engine side and the body ground.
Standard value
:
100-200
Ω
(
20
℃
)
If the measured value exceeds the standard value, replace
the alternator.
点火线图
Ω
ignition line figure
蓝/白
Ω
防水栓:MFD004-2
铜件:DJ621-2.3A
插件:DJ7061Y-2.3-21总成
白
白
白
白/绿 蓝/白
White/
Green
Blue/White
plug-in assembly:
copper parts:
waterproof-bolt:
Assembly
Blue/White
White
White
White
Summary of Contents for QJ150T-10
Page 15: ... 14 QJ150 10 ...
Page 73: ... 72 Rear wheel rear suspension ...
Page 78: ... 77 Lubrication system figure engine oil strainer oil pump bent axle camshaft piston ...
Page 87: ... 86 ...
Page 97: ... 96 ...
Page 104: ... 103 ...
Page 113: ... 112 Output axle Middle axle Input axle ...
Page 116: ... 115 The assembly of bearings and oil seal should use special tools to prevent damage ...
Page 125: ... 124 Muffler ...
Page 131: ... 130 ...