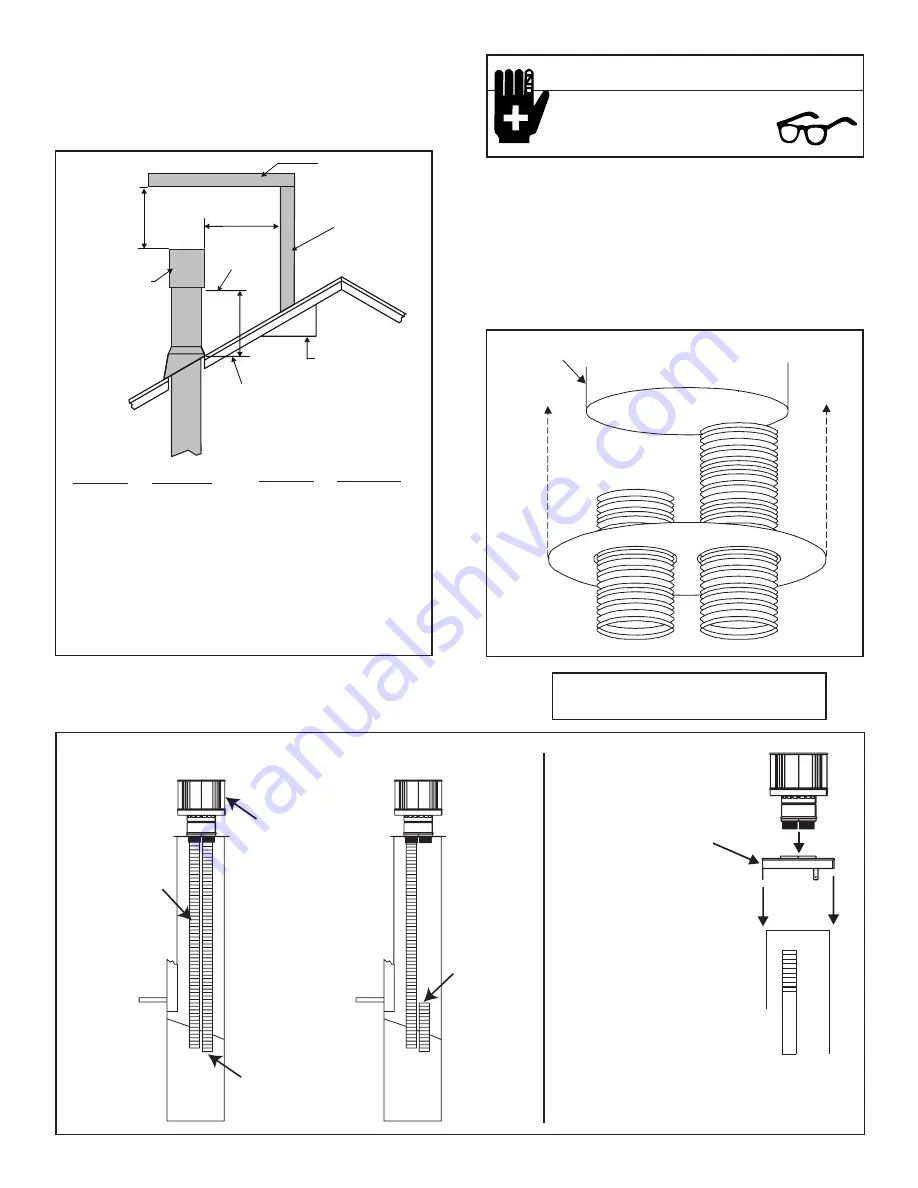
13
Quadra-Fire • QVI30S, QVI35S • 340-901 Rev. i • 6/09
D. Installing Adaptor and Termination Cap
For installation of termination cap see minimum vent
heights for various pitched roofs (see Figure 7.2) .
To install adaptor see Figure 7.3.
Roof Pitch H (Min.) Ft.
Flat to 6/12....................1.0*
Over 6/12 to 7/12 ........1.25*
Over 7/12 to 8/12 ..........1.5*
Over 8/12 to 9/12 ..........2.0*
Over 9/12 to 10/12 ........2.5*
Over 10/12 to 11/12 ..... 3.25
Figure 7.2 Minimum Height from Roof to Lowest Discharge
Opening
* 3 foot minimum in snow regions
Roof Pitch H (Min.) Ft.
Over 11/12 to 12/12 ....... 4.0
Over 12/12 to 14/12 ....... 5.0
Over 14/12 to 16/12 ....... 6.0
Over 16/12 to 18/12 ....... 7.0
Over 18/12 to 20/12 ....... 7.5
Over 20/12 to 21/12 ....... 8.0
CLASS A PIPE
Figure 7.3
Damper Flashing Kit
(Optional)
For use with LINK-DV4-30B Liner Kit.
Note
: Damper may have to be removed to use this kit.
• Run fl ex liners through 3” holes in damper fl ashing.
• Attach damper fl ashing to fi rebox roof with self tapping
screws included in kit.
Figure 7.4
To help eliminate cold air drafts, it may be necessary to place non-
combustible insulation around the fl ues as they go though the damper.
Note
: The LINK-DV4-30B
system REQUIRES this insulation.
Masonry
Factory Built
Wood Burning
EXHAUST
AIR
VENT PIPE
TERMINATION
CAP
LINK-DV30B
Installation
LINK-DV4-30B
Installation
INLET AIR
VENT PIPE
WARNING:
DO NOT BLOCK
THIS PIPE END!
Note: Untwist
the pipe while
extending it, to
achieve full 30’
length.
Remove 18 inch x 18 inch fl ashing on cap by removing
3 screws. Connect both the LINK-ZC-ADPB to Class
A Pipe and the termination cap to the LINK-ZC-ADPB
with the self tapping screws provided.
OPTIONAL LINK-ZC-ADPB
FOR USE WITH CLASS A
WOODBURNING PIPE
Í
OR
Î
CAUTION
Sharp Edges
• Wear protective gloves and safety
glasses during installation.
HORIZONTAL
OVERHANG
VERTICAL
WALL
GAS DIRECT VENT
TERMINATION CAP
12
X
ROOF PITCH
IS X/ 12
LOWEST
DISCHARGE
OPENING
2 FT.
MIN.
20 INCHES MIN.
H (MIN.) - MINIMUM HEIGHT FROM ROOF
TO LOWEST DISCHARGE OPENING