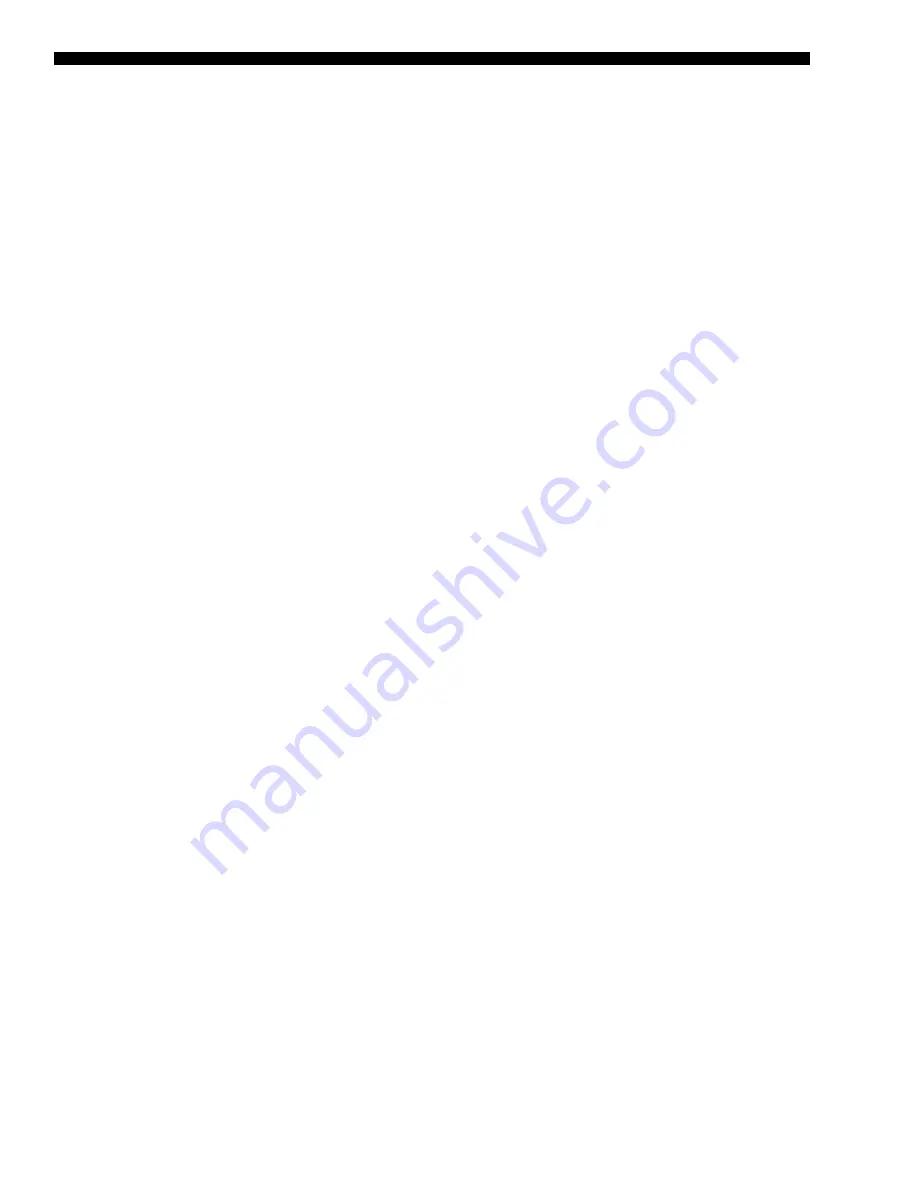
QUANTECH
FORM QTC3-EG6 (1118)
58
6. A 20 mesh, serviceable wye-strainer and mechanical couplings shall be provided for
field installation on evaporator inlet prior to startup.
[Option]
Evaporator shall be provided with piping extension kit and mechanical
couplings to extend liquid connection from evaporator to edge of unit. Thermal
dispersion type flow switch shall be factory installed in the evaporator outlet pipe
extension and wired to the unit control panel. Extension kit nozzle connections shall
be ANSI/AWWA C-606 (grooved) Extension kit pipe insulation and heat trace to be
field provided (if required).
B. Air Cooled Condenser:
1. Coils: Condenser coils shall be constructed of a single material to avoid galvanic
corrosion due to dissimilar metals. Coils and headers are brazed as one piece. In-
tegral subcooling is included. Coils shall be designed for a design working pressure
of 650 PSIG (45 bar). Condenser coil shall be washable with potable water under
100 psi (7 bar) pressure.
2. Low Sound Fans: Shall be dynamically and statically balanced, direct drive, corro-
sion resistant glass fiber reinforced composite blades molded into a low noise, full-
airfoil cross section, providing vertical air discharge and low sound. Each fan shall
be provided in an individual compartment to prevent crossflow during fan cycling.
Guards of heavy gauge, PVC (polyvinyl chloride) coated or galvanized steel shall
be factory installed.
[
Option
]: Ultra-Quiet Fans
3.
Fan Motors: High efficiency, direct drive, 6 pole, 3 phase, insulation class “F”, cur
-
rent protected, Totally Enclosed Air-Over (TEAO), rigid mounted, with double sealed,
permanently lubricated, ball bearings.
2.05 CONTROLS
A. General: Automatic start, stop, operating, and protection sequences across the range
of scheduled conditions and transients.
B. Power/Control Enclosure: Rain and dust tight NEMA 3R powder painted steel cabinet
with hinged, latched, and gasket sealed door.
C. Microprocessor Control Center:
1. Automatic control of compressor start/stop, anti-coincidence and anti-recycle tim-
ers, automatic pumpdown at system shutdown, condenser fans, evaporator pump,
evaporator heater, unit alarm contacts, and chiller operation from 0°F to 125°F
(-18°C to 52°C) ambient. Automatic reset to normal chiller operation after power
failure.
2. Remote water temperature reset via 0-10 VDC or 4-20 mA input signal or up to two
steps of demand (load) limiting.
3. Software stored in non-volatile memory, with programmed setpoints retained in lith-
ium-battery-backed real-time-clock (RTC) memory for minimum 5 years.
4. Forty character liquid crystal display, descriptions in English (or Spanish, French,
Italian, or German), numeric data in English (or Metric) units. Sealed keypad with
sections for Setpoints, Display/Print, Entry, Unit Options & clock, and On/Off Switch.
Guide Specifications (Cont'd)