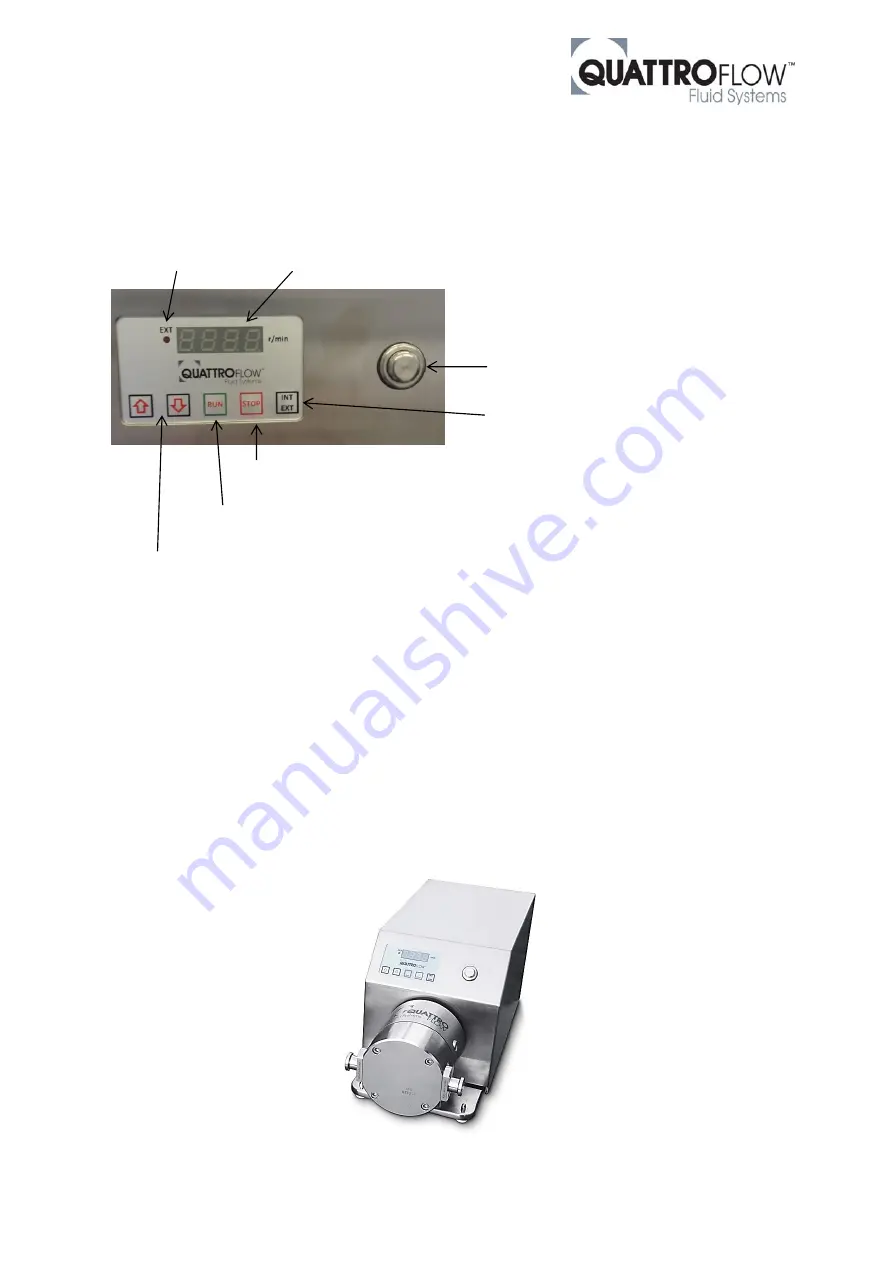
QF1200S; edition 2016-05; page 7 of 24
2.4.2. HT – Compact model (100-240V)
The compact model HT (100-240V) is equipped with a 5° eccentric shaft and achieves a flow rate of
6 – 1200 l/h (1.6 – 317 gph).
Operation of a QF1200S-CV via the control panel:
Attention: The optimal motor parameter are set by the factory.
Only authorized and qualified personnel should change the parameter of the control panel (on
the back of the panel via DIP switches)!
Attention!
Pay attention to the separate operating instructions of the ENGEL–Motor!
QF1200S-HT Pumpe
Motor: Engel, 485 W, 48VDC
Speed control: Digital control panel or analog input 4-20mA
LED EXT
Display rpm (max. 2.400)
Main switch. Push to start.
Shift control source
INT = Panel
EXT = Analog signal
Push the button RUN, to start the
pump
Push the button STOP to stop the
pump.
Push to speed up (arrow bottom-up)
or to speed down (arrow top down)