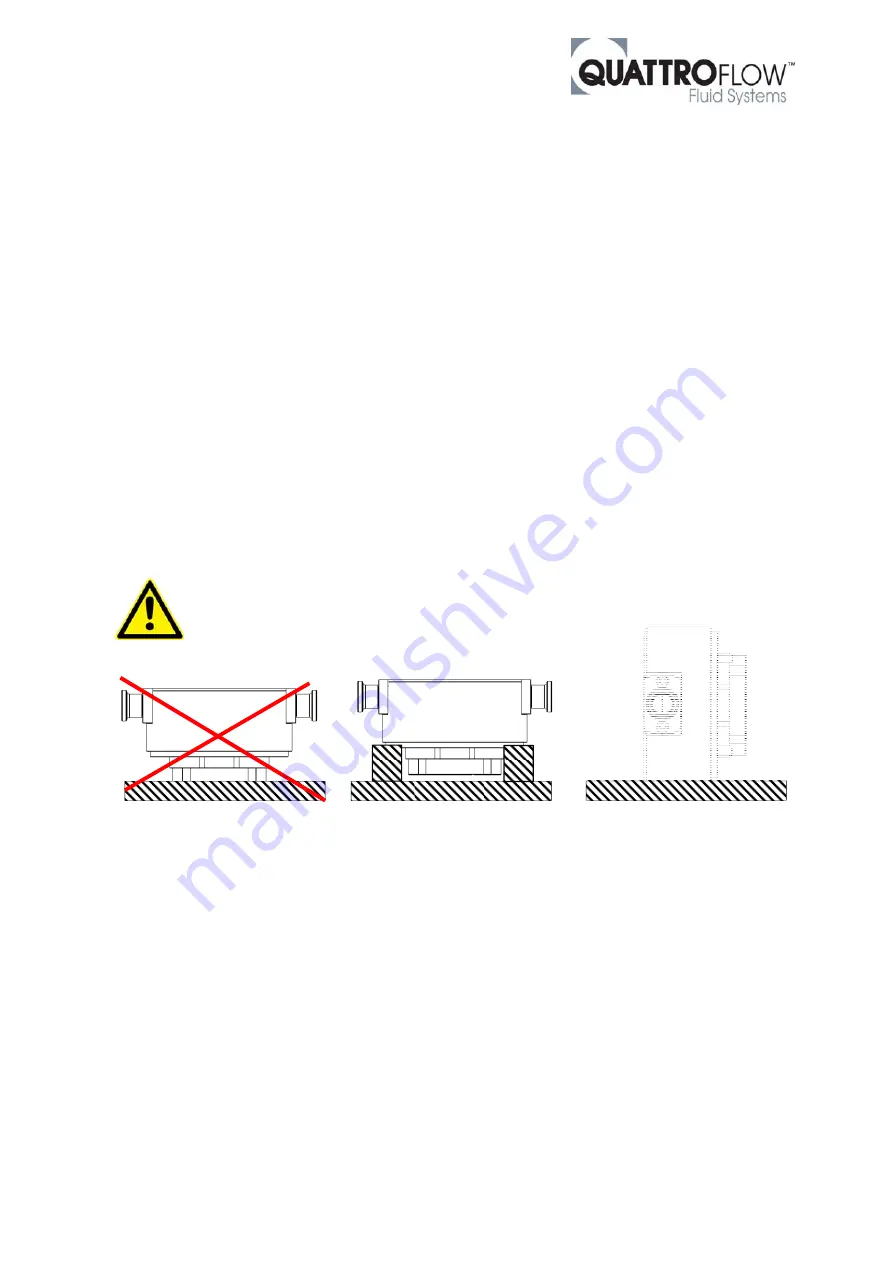
QF1200S; edition 2016-05; page 8 of 24
2.5. Cleaning (CIP)
Depending on the products in contact with the pump and given requirements the cleaning procedure
needs to be adapted accordingly. It is the responsibility of the user to verify the cleaning efficiency.
Safety rules and safety measures like protective glasses, gloves and protective clothing have to be
followed and used when working with chemicals like sodium hydroxide (NaOH).
As a general rule we recommend to clean the pump according to the following procedure.
1. Pre rinse the pump with pure water, until residual amounts of product have been removed.
2. Cleaning step with 0.5 M NaOH (ca. 50°C) at 80% of the maximum RPM for
approximately 30 min. Check before, if surrounding conditions (e.g. pipe diameter, system
pressure rating) allow to operate the pump at this speed.
3. Final rinse with pure water, until neutrality has been achieved (e.g. by measuring
conductivity or pH of the rinse water).
2.6. Autoclave
For autoclaving of the pump chamber we recommend the following steps.
1. CIP of the pump chamber according to 2.4 or any other suitable process
2. Empty the pump
3. Remove the pump chamber from the pump drive (see 4.1.1.)
4. Close in and outlet of the pump e.g. by connecting hoses. Ensure that a free interchange of
gas and steam over a sterile barrier (e.g. sterile filter) at in- and outlet is available.
5. Autoclaving of the prepared pump chamber in a vacuum autoclave at max. 130°C (266°F) for
max. 30 min. Follow instructions of the autoclave manufacturer.
Please make sure that the pump chamber is not placed on the clamp ring during the
autoclave process. The clamp ring should not be loaded during autoclaving.
2.7. Steaming in place (SIP)
For steaming in place the pump chambers needs to be installed on the pump drive. During the
steaming process, the temperature in the pump must not exceed 130°C (266°F) and should not last
longer than 30 min. The cooling of the pump chamber should be against air.
Depending on the SIP
conditions it may be necessary to shorten the maintenance intervals for the elastomers significantly.
Tightening torques (10 Nm, 7.4 lb-ft) of the front bolts of the pump chamber have to be verified after
each SIP cycle.