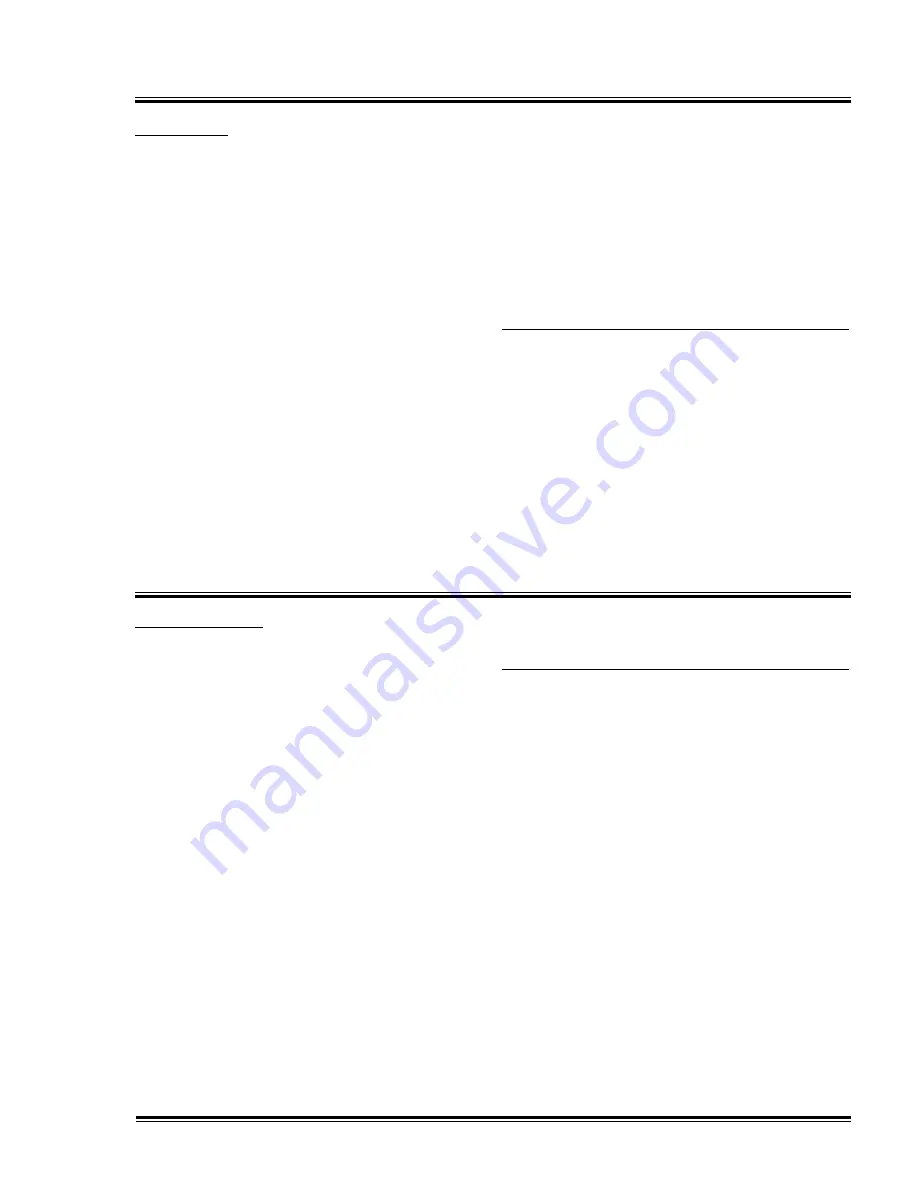
Section VI - Compressor Fluids
QuinSyn-F
QuinSyn-F is Quincy’s food grade fluid,
suitable in applications where there may
be incidental food contact. Compliant with
FDA 2 CFR 78.3570 (Lubricants With
Incidental Food Contact), QuinSyn-F is
authorized by the USDA with an H- rating
for use in federally inspected meat and
poultry plants. Since the fluid is viewed as
a possible indirect food additive, the limit
for food contact is 0 PPM. Near white in
color and low in volatility, QuinSyn-F is
ideal for clean service.
Fluid Life
QuinSyn-F provides an expected life
of 4,000 hours under normal operating
conditions.
Disposal
QuinSyn products are considered
nonhazardous under the OSHA Hazard
Communication Standard 2 CFR
90.200. They carry no hazardous labels
or warnings under that standard.
T
ypical
p
roperTies
of
Q
uin
s
yn
-f
v
iscosity
@ 100°f astm d445
43.0
c
s
t
.
v
iscosity
@ 210°f astm d445
7.5
c
s
t
.
v
iscosity
i
ndex
astm d2270
139
f
lash
p
oint
astm d92
495°f
f
ire
p
oint
astm d92
560°f
p
our
p
oint
-76°f
s
pecific
g
ravity
60/60
0.83
c
olor
* w
ater
white
/w
hite
*Changes to color will occur during
operation.
QuinSyn Flush
QuinSyn Flush is a specially formulated
synthetic fluid capable of dissolving varnish
and solubilizing sludge from lubricating
systems while they are operating.
QuinSyn Flush contains oxidation and rust
inhibitors, and can be used as a short-
term fluid (for a maximum of 500 hours).
It is fully compatible with mineral oils and
QuinSyn synthetic fluids, and is highly
recommended for use as a flushing fluid
when converting to QuinSyn-PG from
QuinSyn or QuinSyn-IV.
applications
Cleaning fluid for removal of varnish, dirt
and oxidized fluid from compressor fluid
systems.
Flushing fluid when changing from other
fluids to QuinSyn fluids.
T
ypical
p
roperTies
of
Q
uin
s
yn
f
lush
v
iscosity
@ 100°f astm d445
43.3
c
s
t
.
v
iscosity
@ 210°f astm d445
5.6
c
s
t
.
v
iscosity
i
ndex
65
f
lash
p
oint
astm d92
444°f
f
ire
p
oint
astm d92
520°f
p
our
p
oint
–45°f
s
pecific
g
ravity
60/60
0.965
Quincy Compressor-QGV Series
53
Summary of Contents for QGV-100
Page 2: ......
Page 6: ......
Page 17: ...Section II Description This page intentionally left blank Quincy Compressor QGV Series 11 ...
Page 74: ...Appendix A Dimensional Drawings QGV 50 air cooled 68 Quincy Compressor QGV Series ...
Page 75: ...Appendix A Dimensional Drawings QGV 50 water cooled Quincy Compressor QGV Series 69 ...
Page 76: ...Appendix A Dimensional Drawings QGV 75 100 air cooled 70 Quincy Compressor QGV Series ...
Page 77: ...Appendix A Dimensional Drawings QGV 75 100 water cooled Quincy Compressor QGV Series 71 ...
Page 78: ...Appendix A Dimensional Drawings QGV 150 200 air cooled 72 Quincy Compressor QGV Series ...
Page 79: ...Appendix A Dimensional Drawings QGV 150 200 water cooled Quincy Compressor QGV Series 73 ...
Page 89: ......