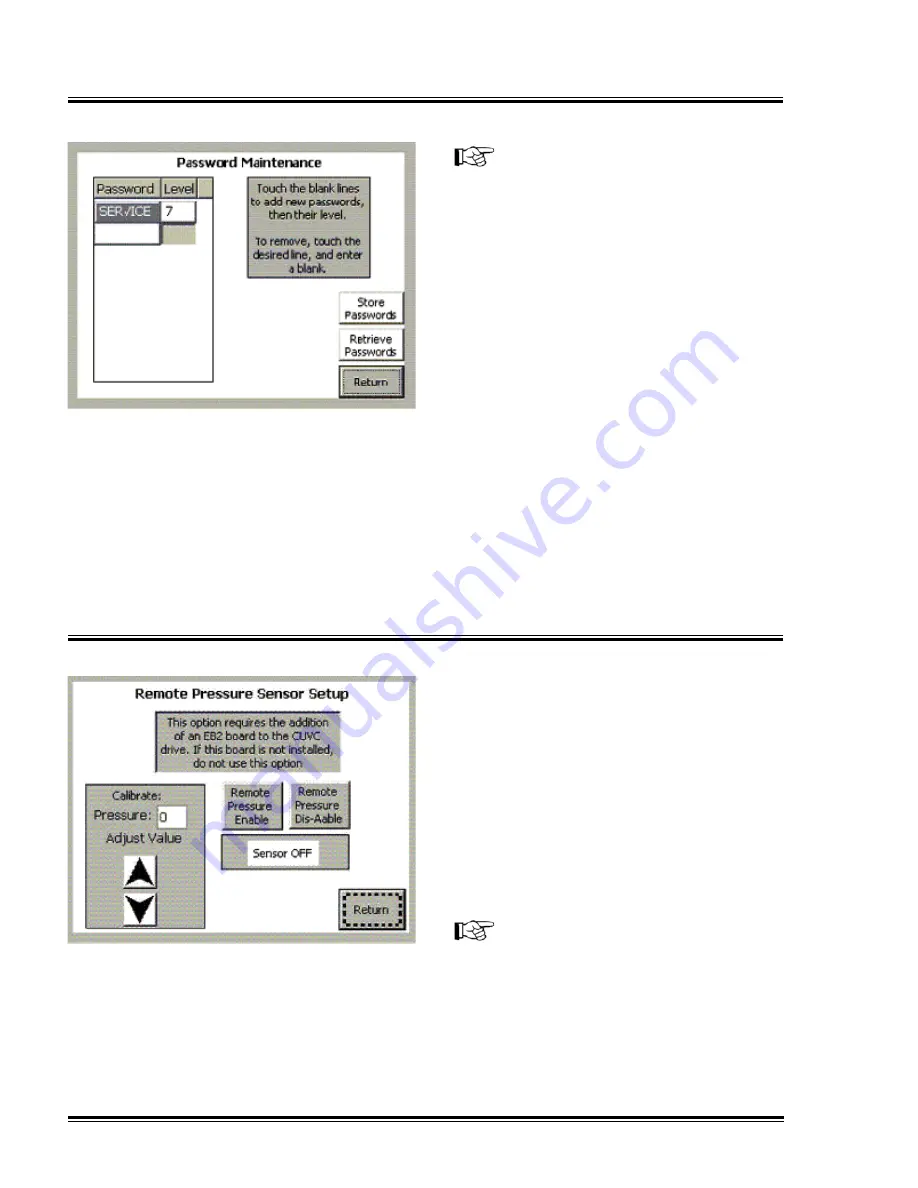
Section IV - Operating Procedures
Password Setup -
To access ‘Password Maintenance’, touch
‘Password Setup’ at the ‘Menu Selection’
screen.
To prevent casual alterations in the settings
several entry points in the menu selections
are password protected. Since all
passwords are maintained here, ‘Password
Maintenance’ requires a password level of
7 to access.
notiCe!
The default password is ‘quincy’ which
has an access level of 7.
Each unit may be assigned up to eight
passwords with access levels from 0 to 7.
Level 0 is the lowest level (the public level),
level 7 is the highest (provides access to all
password protected menus).
Certain menu selections require a minimum
access level to enter, thereby providing
strict control over who can change the
settings of the compressor. Passwords
can be set using any combination of up to
eight characters (letters and numbers).
The password list is stored on the Compact
Flash card. Touch ‘Retrieve Passwords’
to display a list of current passwords. To
reset the passwords, follow the instructions
on the ‘Password Maintenance’ screen and
touch ‘Store Passwords’ to save.
Touch ‘Return’ to return to the ‘Menu
Selection’ screen.
Remote Pressure Sensor Setup -
This option can be used to add an
additional pressure sensor to the system,
typically located on the storage tank,
to assist the compressor in adapting to
pressure changes.
As indicated on the screen, this option
requires the installation of an EB2 board in
the drive.
Access this screen to enable or disable the
sensor and to display the current status.
The remote sensor may be calibrated as
well.
notiCe!
This is only to ZERO pressure offsets,
and not for scales, which are assumed
to be fixed at 300 psig.
28
Quincy Compressor-QGV Series
Summary of Contents for QGV Series
Page 2: ......
Page 6: ......
Page 17: ...Section II Description This page intentionally left blank Quincy Compressor QGV Series 11...
Page 74: ...Appendix A Dimensional Drawings QGV 50 air cooled 68 Quincy Compressor QGV Series...
Page 75: ...Appendix A Dimensional Drawings QGV 50 water cooled Quincy Compressor QGV Series 69...
Page 76: ...Appendix A Dimensional Drawings QGV 75 100 air cooled 70 Quincy Compressor QGV Series...
Page 77: ...Appendix A Dimensional Drawings QGV 75 100 water cooled Quincy Compressor QGV Series 71...
Page 78: ...Appendix A Dimensional Drawings QGV 150 200 air cooled 72 Quincy Compressor QGV Series...
Page 79: ...Appendix A Dimensional Drawings QGV 150 200 water cooled Quincy Compressor QGV Series 73...
Page 89: ......