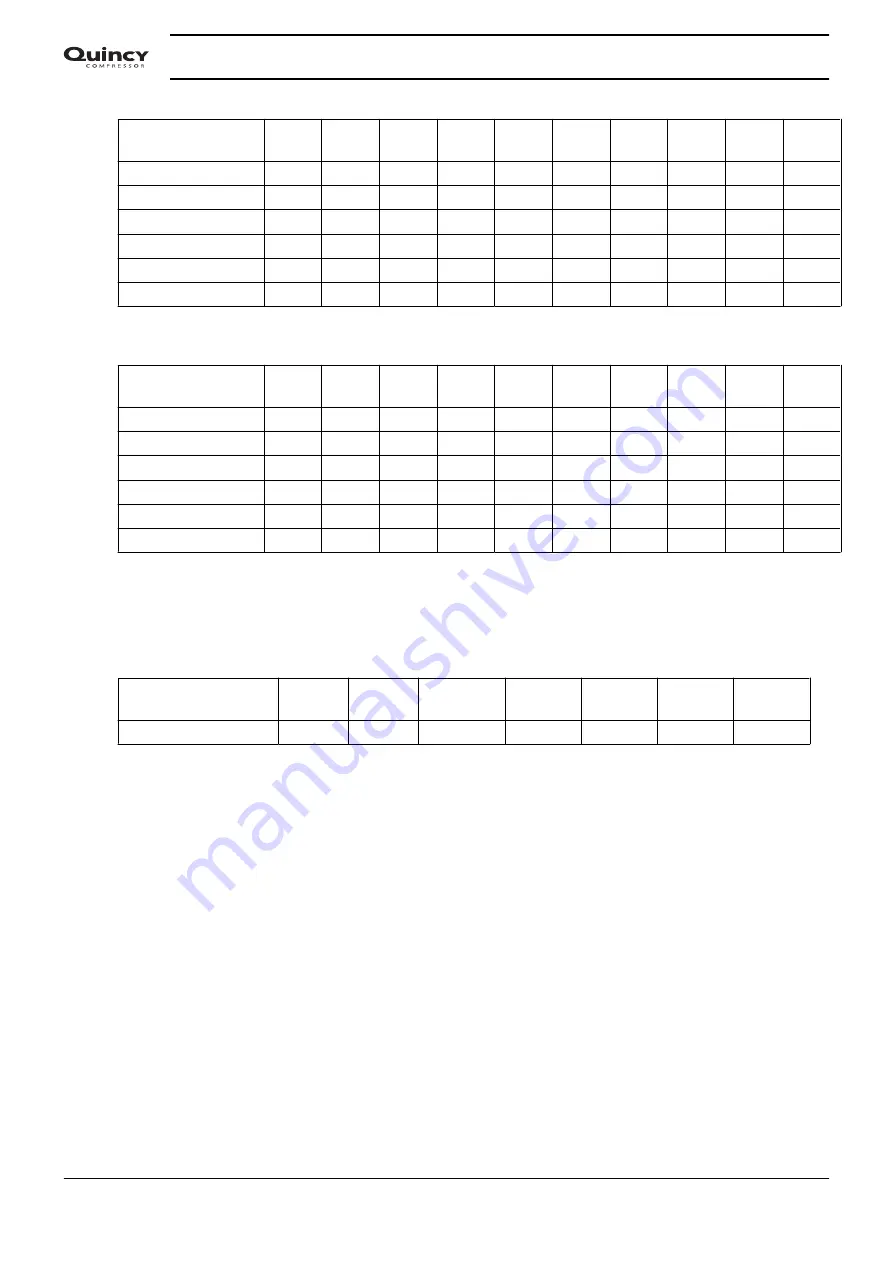
Models
QOCS
25
QOCS
53
QOCS
106
QOCS
180
QOCS
360
QOCS
636
QOCS
1325
QOCS
2650
QOCS
5300
Cold climate
l/s
16
33
67
113
227
400
833
1666
3332
Cold climate
cfm
34
71
141
240
480
848
1766
3532
7065
Mild climate
l/s
12
25
50
85
170
300
625
1250
2500
Mild climate
cfm
25
53
106
180
360
636
1325
2650
5300
Hot climate
l/s
6
12
24
41
83
146
304
608
1216
Hot climate
cfm
13
26
52
88
175
309
645
1289
2578
Installation with compressors, air receivers and filters:
Models
QOCS
25
QOCS
53
QOCS
106
QOCS
180
QOCS
360
QOCS
636
QOCS
1325
QOCS
2650
QOCS
5300
Cold climate
l/s
20
42
83
142
283
500
1042
2083
4167
Cold climate
cfm
42
88
176
300
601
1060
2208
4417
8833
Mild climate
l/s
15
31
63
106
213
375
781
1563
3125
Mild climate
cfm
32
66
133
225
451
795
1656
3313
6625
Hot climate
l/s
9
17
34
57
114
201
420
839
1678
Hot climate
cfm
18
36
71
121
242
427
890
1779
3558
Correction factors
For operation in conditions other than reference conditions, multiply the compressor capacity
(FAD) in the tables above with the corresponding correction factors.
Running hours per
day
12
14
16
18
20
22
24
Correction factor
1.00
0.86
0.75
0.67
0.6
0.55
0.5
The condensate treatment device is designed to operate 12-hour duty cycles or less. If the
compressor is running more than 12 hours per day, the appropriate correction factor must be
considered.
Example
Working condition:
• Ambient temperature = 25 °C (77 °F)
• Relative humidity = 60%
• Compressor running hours = 24
• Correction factor = 0.5 (see table above)
QOCS 360 at reference conditions (with dryer): 170 l/s (360 cfm)
QOCS 360 at working condition: 170 x 0.5 = 85 l/s (180 cfm)
Max Compressor FAD of 85 l/s (180 cfm) can be connected to a QOCS 360 unit at above
working conditions.
Instruction book
24
2920 7197 51
Summary of Contents for QOCS 25
Page 2: ......
Page 16: ...QOCS 25 QOCS 53 QOCS 106 QOCS 1325 QOCS 2650 Instruction book 14 2920 7197 51...
Page 28: ......
Page 29: ......