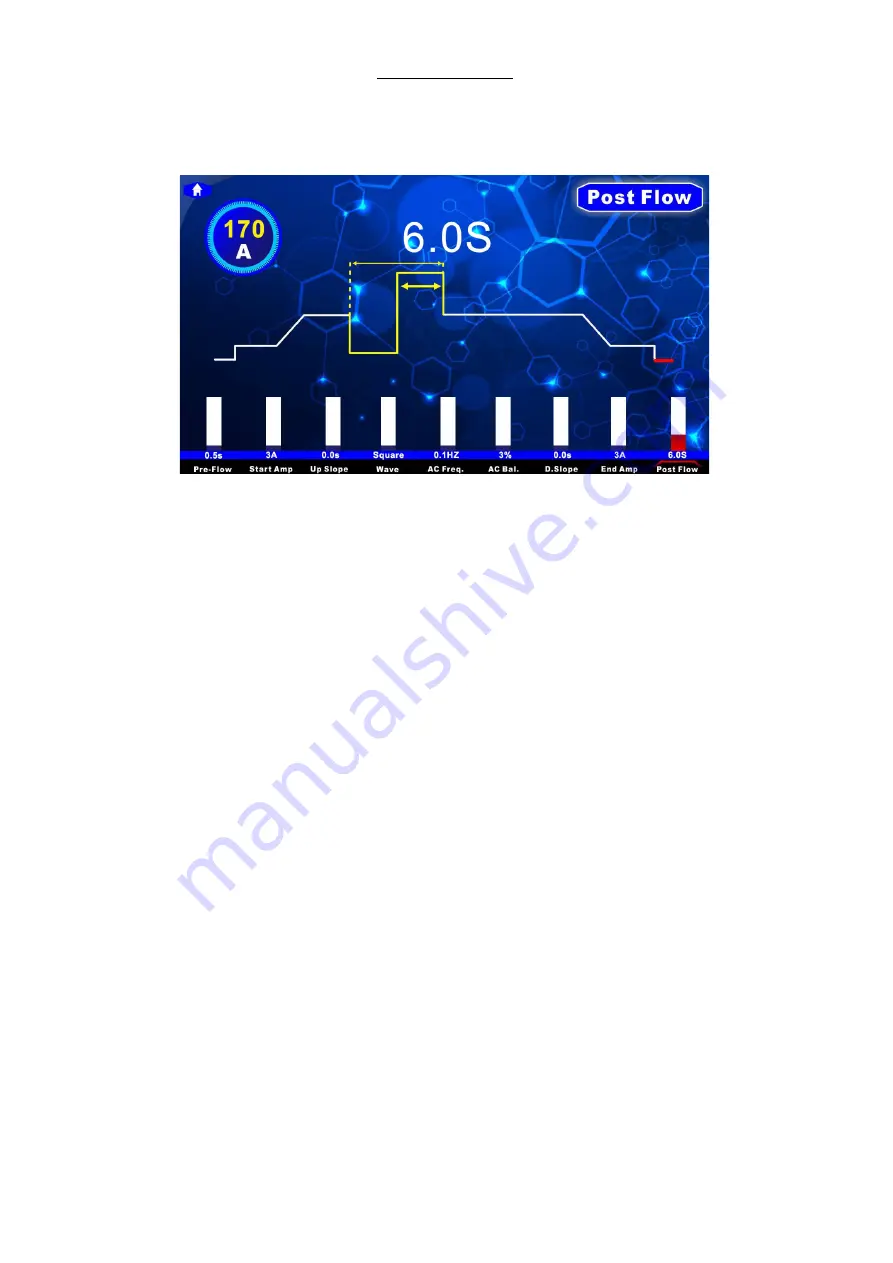
42
Post flow gas time
Use control knob to adjust post flow gas time then press arrow button to move to next setting.
Adjustable between 0.0
-
60 seconds
Once all settings have been set, you can start welding immediately or return to home screen by pressing
home button and then you can adjust amperage or other settings if required.