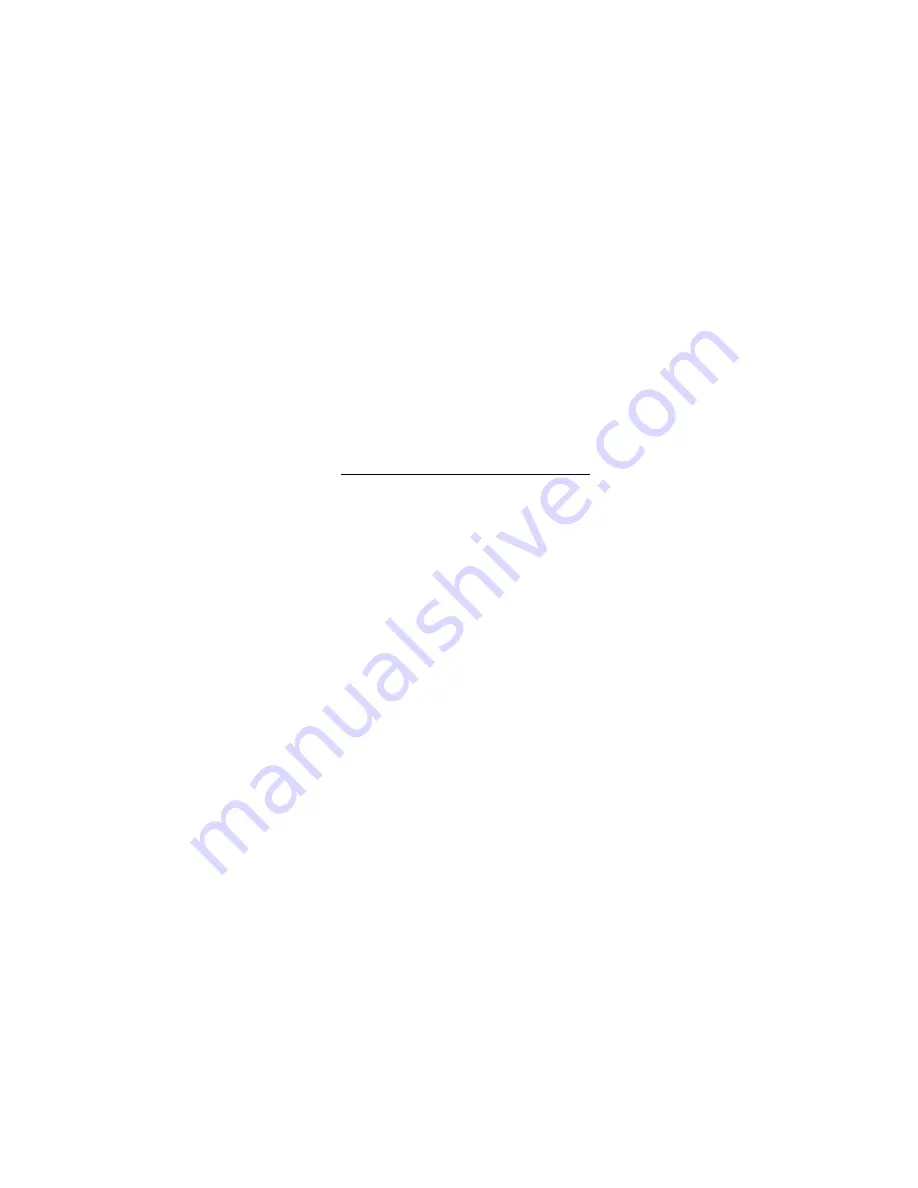
22
•
HF spark is present at the tungsten electrode but unable to start welding arc,
Machine has normal welding output
1 Tungsten may be contaminated - replace or sharpen
2 The current may be set too low
3 Tungsten may be to large for process
4 Gas flow may be insufficient, increase gas flow, reduce tungsten stick out from ceramic
•
No HF when torch trigger pressed, no blue spark between HF points
Examine and clean HF points with clean dry low pressure air line
HF PCB faulty – Contact R-Tech for repair
MMA Stick welding problems
•
Stick electrode ‘blasts off’ when arc is struck
Welding current set to high, reduce amperage or use thicker electrode
Contaminated electrodes or material
•
Electrode sticks in weld puddle
Welding current is set too low
Arc is too short, keep electrode further away from work
•
Excessive splatter
Too long an arc, keep electrode closer to work
•
Poor penetration
Travel speed too fast
Too much welding current, reduce welding amperage
•
Porosity in weld
Electrodes are damp
Arc too long, get electrode closer to work
Summary of Contents for TIG315
Page 1: ...TIG315 AC DC TIG WELDER OPERATION INSTRUCTIONS www r techwelding co uk...
Page 2: ...2...
Page 23: ...23...
Page 24: ...24...
Page 25: ...25...