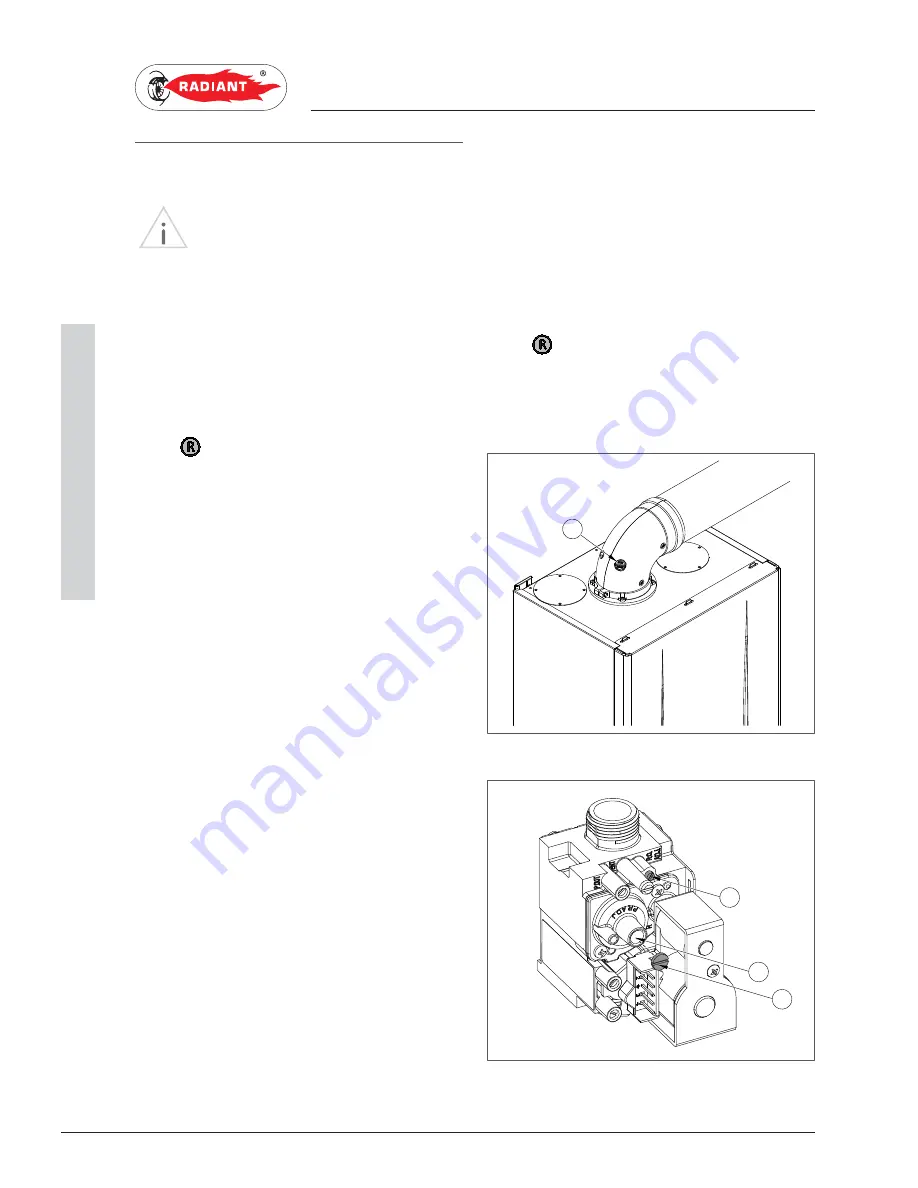
32
R1K 24 /B - RAD - ING - Manuale - 1507.1 - R2 G
2 Ve
rif
ic
a
e t
a
ra
tur
a del
va
lo
re
di
CO
2
_
M
IAH
4
_
R2
K
_
E
N
2. FIRST START-UP
SUPPOR
T
C
ENTRE
2.1.3. CO2 VALUE CHECK AND
CALIBRATION
WARNING
The CO
2
value should be checked with
the casing assembled, while the gas valve should be
adjusted with the casing open.
To check and calibrate the CO
2
value to minimum
and maximum heating power proceed as follows:
FOR MAXIMUM HEATING POWER
› Activate the chimney sweep function holding the
key ‘
’ for 7 seconds.
› Insert the fumes analyser probe in the suitable
‘PF’ fumes inlet (fig. 1), then make sure that
the CO
2
value complies with the requirements
indicated in chapter “Technical data”, otherwise
adjust using screw ‘1’ (fig. 2) of the gas flow
adjuster. To increase the CO
2
value, turn the
screw anti-clockwise and vice-versa if you want
to decrease it.
› After each adjustment variation on screw ‘1’
(fig. 2) of the gas flow adjuster you have to wait
for the boiler to stabilize itself to the set value
(about 30 seconds).
FOR MINIMUM HEATING POWER
› Access parameter ‘P10’ following the procedure
described in chapter “Parameters accessing
and programming” and stay in edit mode until
the calibration is completed (the maximum time
before forced exiting the edit mode is 7 minutes.
› Make sure that the CO
2
value complies with
the indications in “Technical data”, otherwise
unscrew the protection screw ‘A’ (fig. 2) and
adjust using a 4 Allen wrench the screw ‘2’ (fig.
2) of the Off-Set adjuster. To increase the CO
2
value, turn the screw clockwise and vice-versa
if you want to decrease it.
› Once completed the adjustment, tighten the
protection screw ‘A’ (fig. 2) on the Off-Set
adjuster.
› Exit parameter ‘P10’ following the procedure
described in chapter “Parameters accessing
and programming”.
› Activate the chimney sweep function holding the
key ‘
’ for 7 seconds.
› Make sure that the CO
2
value did not change
to maximum, if changed repeat the calibration
described in the previous paragraph.
PF
1
2
A
fig. 1
fig. 2