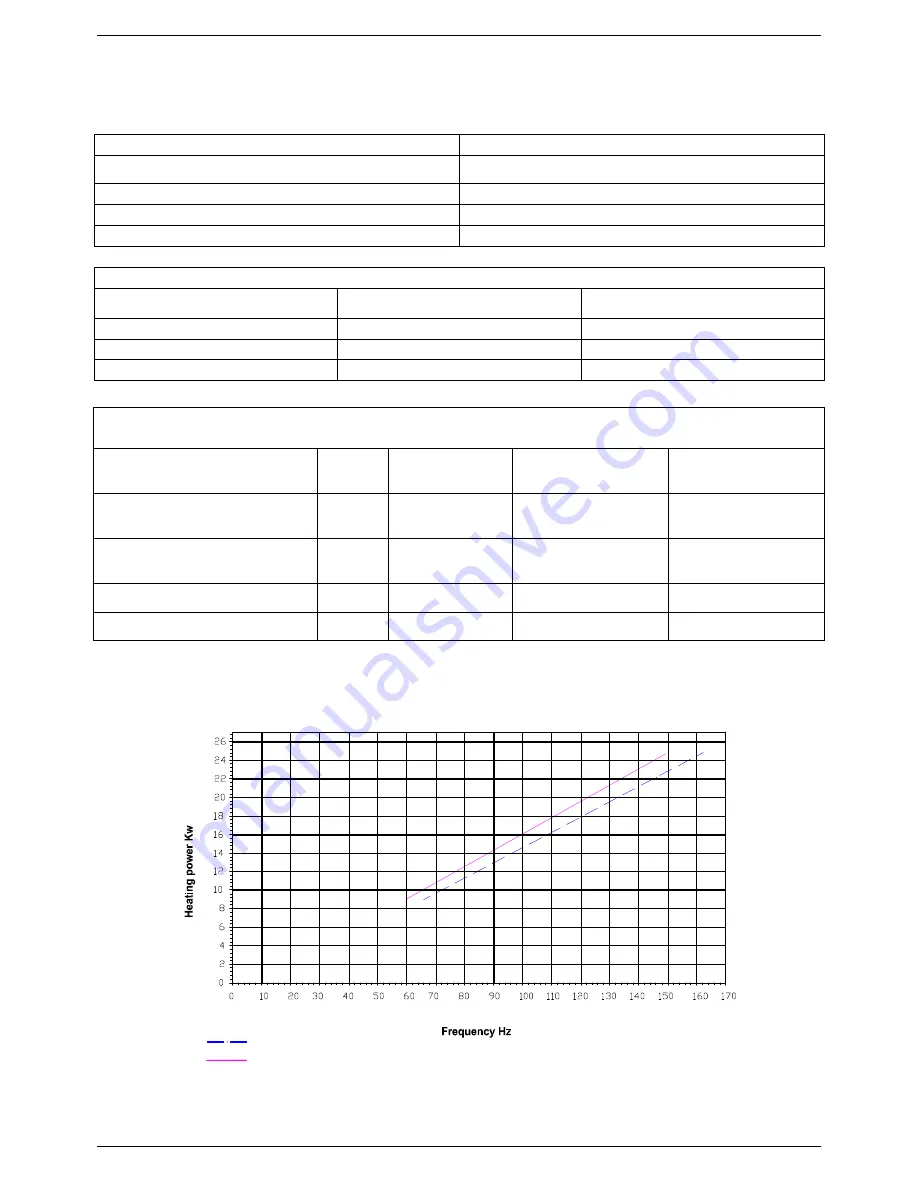
REGULATION INSTRUCTIONS
37
Technical data tables - RK 25 OV
Heating Power (kW) – Fan frequency (Hz) diagram
G20
G30 / G31
Table no.2 - Frequency
Gas type
Minimum (Hz)
Maximum (Hz)
Natural gas - G20
66
162
Liquid Butan Gas - G 30
60
149
Liquid Propane Gas - G 31
60
149
Table no.3 - Gas data table
NATURAL GAS
G20
LIQUID BUTANE GAS
G30
LIQUID PROPANE
GAS G31
Indice di Wobbe inferiore
(15°C; 1013 mbar)
MJ/Nm
3
45.67
80.58
70.69
Pressione nominale di
alimentazione
mbar
20
30
37
Consumi (15°C; 1013 mbar)
m
3
/h
2.64
-
-
Consumi (15°C; 1013 mbar)
kg/h
-
1.97
1,94
Table no.1 - CO
2
Values
Gas type
CO
2
%
Natural gas - G20
9.4
Liquid Butan Gas - G 30
10.9
Liquid Propane Gas - G 31
10.96