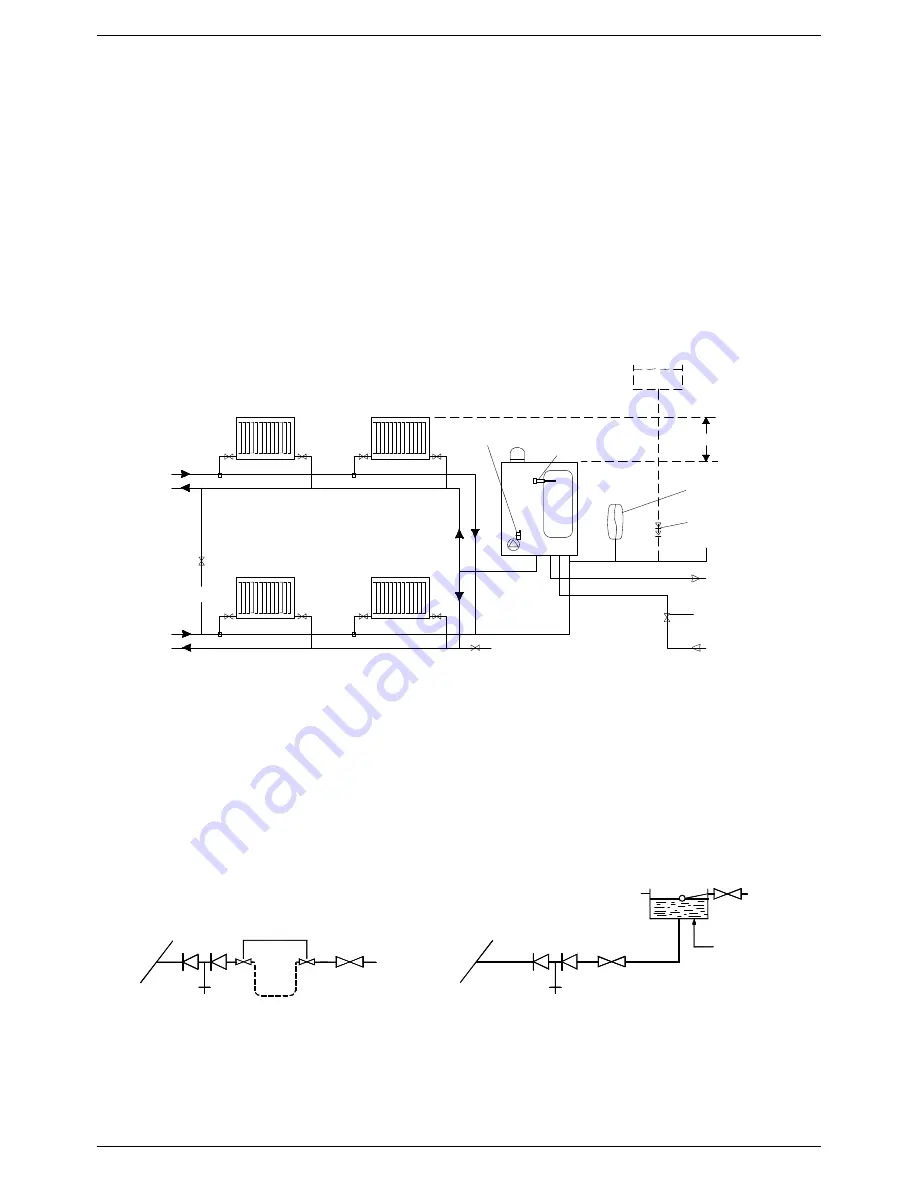
INSTALLATION INSTRUCTIONS
16
3.6 Central heating circuit
The boiler is designed for use in a sealed central heating system in accordance with the requirements of BS 5449 and BS 6798.
The system should be designed to operate with flow temperatures of up to 82°C. When designing the syst em, the pump head,
expansion vessel size, mean radiator temperature, etc. must all be taken into account. Refer to the pump performance table
for guidelines.
System volume -The 7 litre expansion vessel incorporated into the boiler is generally suitable for most sealed heating
systems however if the system has a larger volume of water it may be necessary to provide extra capacity for expansion.
The boiler is supplied with the following components built in:-
Pressure relief valve -complying with BS 6759 and set to operate at 3 bars. The outlet connection of the boiler safety valve
must terminate to atmosphere in accordance with current regulations. The manufacturer will not be held responsible for
flooding caused by the operation of the safety valve in the case of system overpressure..
Pressure gauge -To indicates the system pressure to be maintained.
Expansion vessel – Volume 7 litre. Conforming to BS 7074:1 for GB,
By-pass -The boiler incorporates a by-pass, however where all radiators are fitted with thermostatic radiator valves it is
recommended an automatic system by-pass is fitted.
Additional expansion
vessel (if required)
Double check valve assy
Temperature/pressure
relief valve
Boiler
Automatic air vent
Heating return
System
drain tap
Note: A drain tap should be installed at the lowest point of the
heating circuit and beneath the appliance
Note: If required, an automatic
by-pass is preferred
Radiator
valve
Filling point
DHW outlet
Pressure reducing
valve (supplied)
Mains water
inlet
Static head of system
Make up vessel
Heating by-pass
(if required)
Lockshield valve
Filling the central heating system – figs. 2-3
The system design pressure (cold) should be set to 1.5 bar. This pressure is equivalent to a static head of 15.4 metres of
water.
Provision should be made to replace water lost from the system during servicing etc. as shown in Figs. 2 and 3. The position
for connecting an alternative make-up vessel is indicated in Fig. 1. A double check valve assembly must be used. as shown in
Fig. 3.
Filling of the system must be carried out in a manner approved by the local Water Undertaking (GB: Guidance G24.2 and
Recommendation R24.2 of the Water Regulation Guide). Where allowed the system may be filled via a temporary connection
as shown in Fig. 2. After filling, always disconnect the flexible hose of the filling loop.
All fittings used in the system must be able to withstand pressures up to 3 bar.
Drain taps (to BS 2879) must be used to allow the system to be completely drained.
Double
check valve
assembly
Test
cock
Feed cistern to be
located above highest
point in the system
Overflow
Heating
circuit
return
Test
cock
Double
check valve
assembly
Stop
valve
Mains water
supply
Mains
water
supply
Stop
valve
Filling loop
temporarily
connected
Hose
unions
Heating
circuit
return
In
order to prevent scaling or deposits in the primary heat exchanger, the water in the heating circuit must be treated
according to the requirements of standard.
This treatment is indispensable in the case where the circuit is frequently topped-up or when the system is often either partially
or fully drained. Frequent topping-up of the system should be avoided and normally indicates a leak within the heating system.
Fig. 1
Fig. 2
Fig. 3