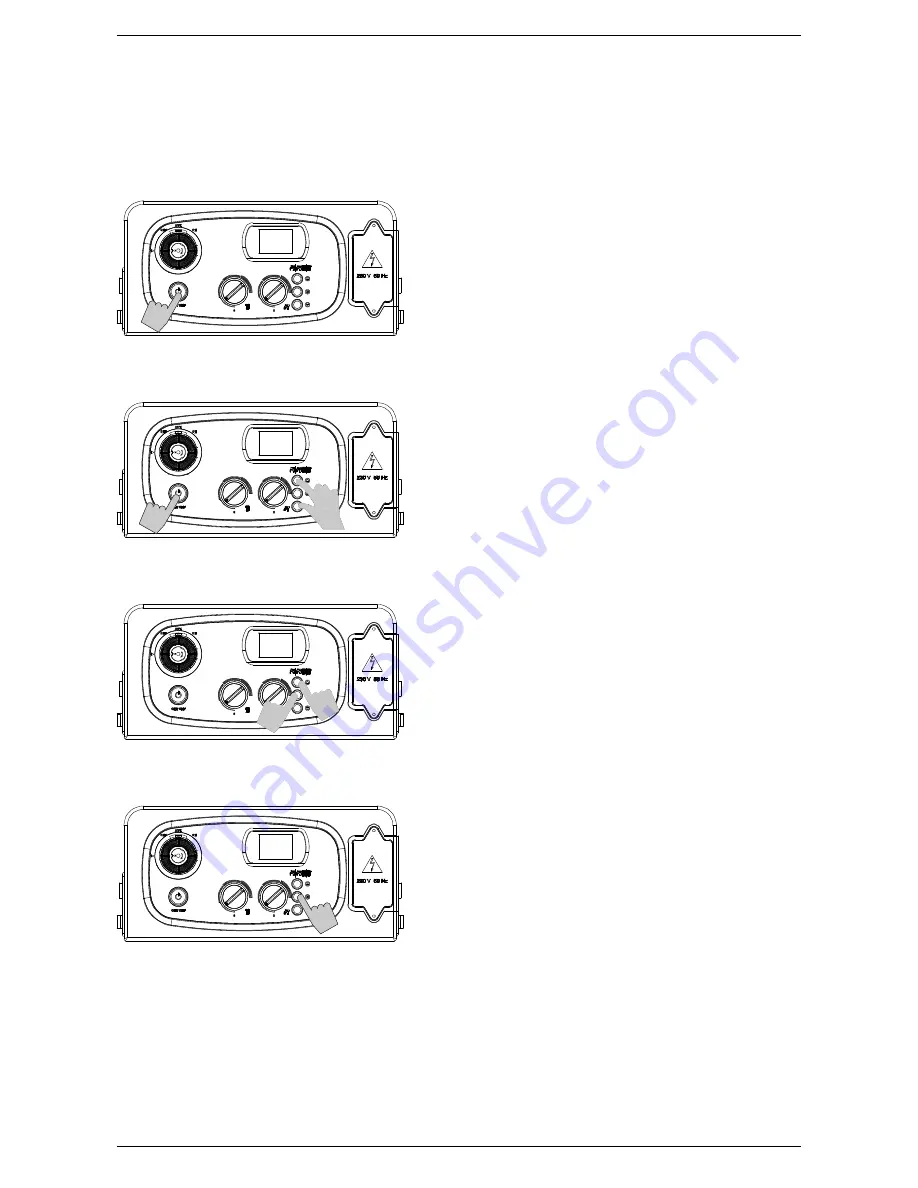
REGULATION INSTRUCTIONS
32
5.2 Setting the parameters
To modify the preset values of the parameters reported in the previous table, open the parameter
settings menu as follows:
1. Place the On/Off switch in the OFF
position.
2. Activate the On/Off switch while keeping
buttons ‘+’ and “-“ pressed. Wait for “P 00” to
appear on the display.
3. Release buttons ‘+’ and ‘-’.
4. Keep button ‘S’ pressed and use button
‘+’ to select the parameter to modify.
5. Release button ‘S’, then re-press and
release it. The display will indicate the value
of the parameter to modify.
Adjust the value of the parameter using the
procedure described in the following pages.
To enter the parameters menu, follow the previously described procedure (steps 1-5).
OFF
P 00
P 00
P 01