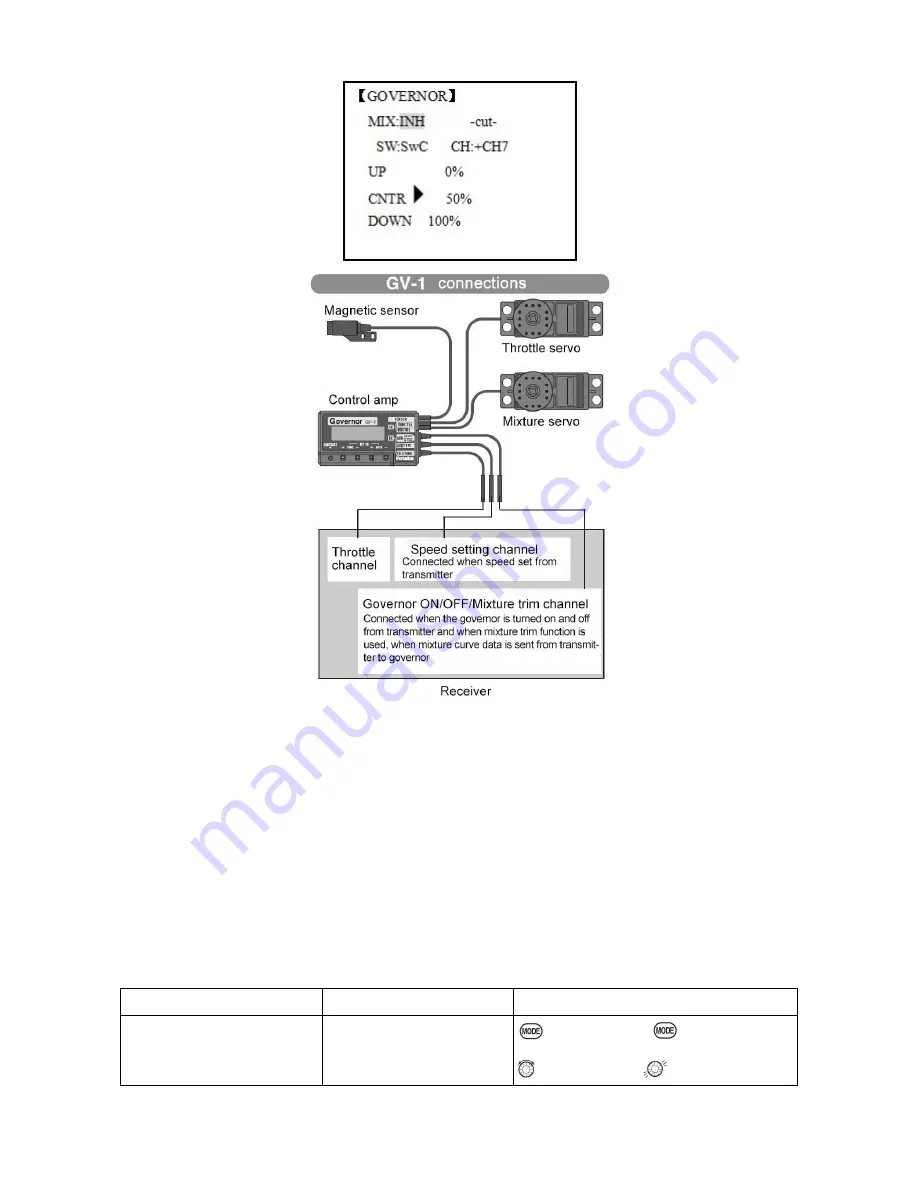
73
ADJUSTABILITY:
•
On/off may be separate from speed switching by plugging governor on/off into CH8 and changing
CUT-CH setting.
•
If using separate on/off, switch assignment is totally adjustable. Be careful not assign governor off to a
condition switch if you want the governor to function in that condition.
•
Speed switching and governor ON/OFF may be together using one switch or ON/OFF switching may be
performed using an independent switch/channel.
•
When speed setting control uses CH7 and separate ON/OFF switch is not used, CH8 can be used for other
functions.
•
In-flight adjustment of the head speed (for easy adjustment during turning) may be created using an
additional channel and a programmable mix.
The GV-1 controls throttle when it is active, so the throttle will not obey any FailSafe settings preset for
throttle in the transmitter. Always set the FailSafe setting for the GV-1's on/off channel to OFF. This way
the governor is shut off and the throttle obeys the FailSafe throttle commands.
Goals
Steps
Inputs
Set up a governor to use
both channels into the receiver
and switch between the
Open and activate the
GOVERNOR
Function.
to BASIC menu,
again to
ADVANCE
to GOVERNOR