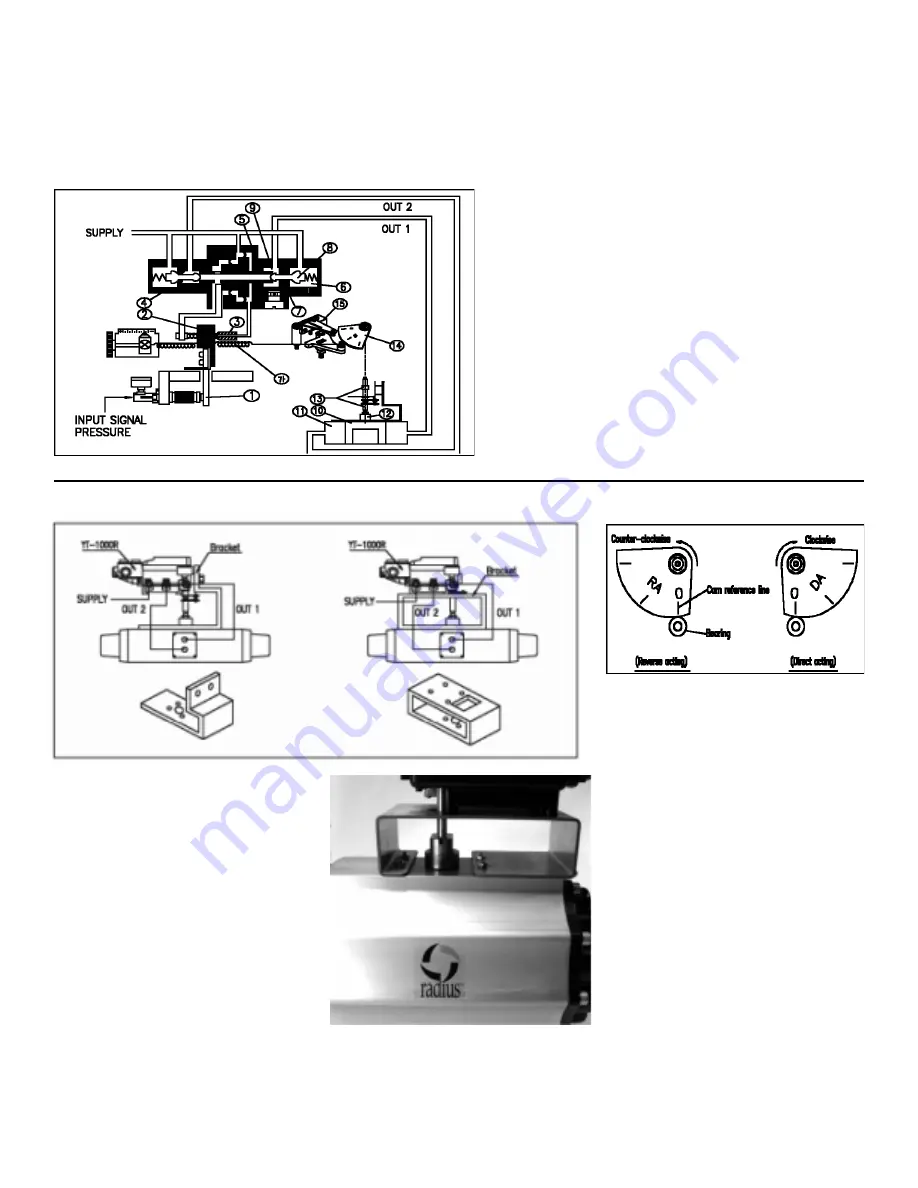
The movement of Actuator stem exerted force to the
Feedback Spring through Feedback Shaft connections.
Then Actuator will stop at the point of force balance
exerted by the input current signal and the feedback
spring.
Increase the input signal to change in lift position of
valve.
Force exerted by Torque Motor reduces Nozzle Back
Pressure with increase in gap between Flapper and
Nozzle. Then Spool moves upward and the Seat opens
simultaneously. Air pressure of OUT1 pipe is discharged
to Actuator. As pressure in the actuator chamber goes
up, Actuator stem start to move.
4. OPERATING PRINCIPLES
2) Cam attaching procedure
(1) Use the DA face of cam to turn
the actuator main shaft clockwise
(viewed from the positioner front cover
side) at the time of input feedback
shaft. Use the RA face to turn it
1 Example of attaching to actuator
Radius provides a stamped stainless
steel bracket (above right) for mount-
ing to the bottom of the positioner.
However the RX-1000 is drilled and
tapped on the side for side mounting
of a custom fabricated bracket (above
left).
5-2 Connection with feedback shaft.
All Radius brand positioners come
with the standard NAMUR type
spaded shaft for direct interface to all
Radius actuators and most all other
brands of rack and pinion actuators
manufactured with the NAMUR type
slotted top shaft. Because all Radius
positioners are supplied with a
stainless steel mounting bracket,
attachment to these types of actua-
tors is very simple.
counterclockwise (reverse action).
Correctly attach the cam to the flange
part of feedback shaft.
(2) Attach the cam in the procedure
of loosening the hexagonal nut with
flange first, setting the using actuator
to the starting position and then
setting the cam reference line and the
bearing contact point of span adjust-
ing arm unit to the matching position.
(3) Do not apply the supply pressure
when attaching the cam as otherwise
it is very dangerous.
(4) When the positioner is shipped out
of our plant, the cam is tentatively
tighened to the shaft. Be sure to firmly
lock the cam the lock nut [tightening
torque 2.0~2.5Nm(20~25kgfcm)].
5. INSTALLATION