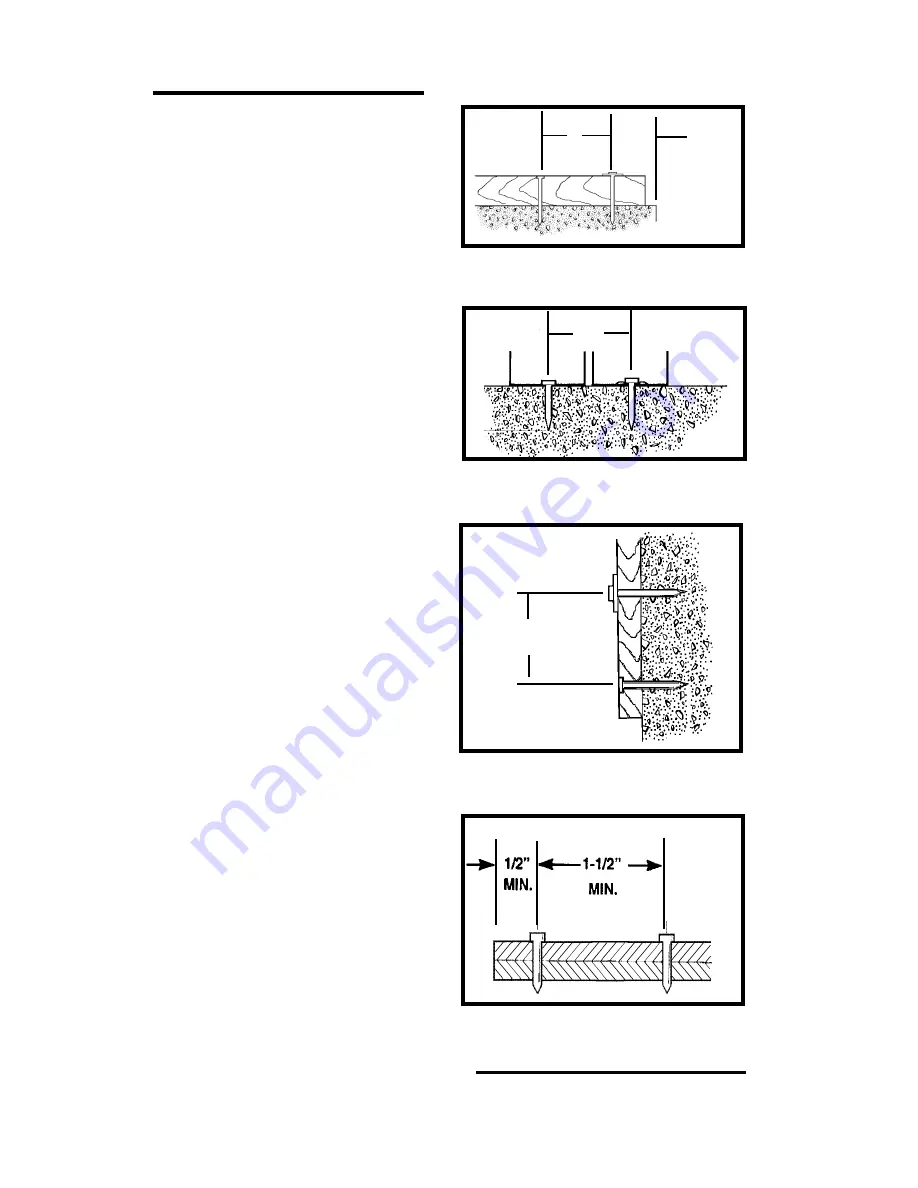
FASTENING APPLICATIONS
FASTENING APPLICATIONS
8
FASTENING APPLICATIONS
Your Ramset tool can be used for a wide
range of fastening needs in a variety of
base materials. Reading and following
these important fastening guidelines will
help you get the best results from your
tool, fasteners, and powder loads, as
well as help you perform these fastening
operations safely and effectively.
Powder actuated fastenings are perm-
enant fastenings so attempting to
remove a fastener from concrete or
steel may result in a serious injury.
Fastening to Concrete
When fastening into concrete, always
maintain a minimum spacing of 3"
between fastenings and 3" from any
free edge. Concrete thickness should
be at least three times the intended
penetration depth into the concrete. The
primary exception to the 3" edge
distance can occur in a sill plate
application where, by necessity, the
edge distance is reduced.
Driving fasteners too close to an edge
or too close to each other can cause
the concrete edge to fail or fasteners to
fly free.
Fastening to Concrete Block or
to Masonry Walls
While this application is not recom-
mended, when used, it is necessary to
take care to observe a 3” edge distance
to avoid cracking the block and over
penetration of the fastener to avoid a
loss of holding value. Fastenings may be
made into the horizontal joint but not into
the vertical joint.
SPACING
WOOD TO CONCRETE
PENETRATION - THIN GAUGE
METAL TO CONCRETE
➤
➤
➤
➤
➤
➤ ➤ ➤ ➤ ➤
➤➤➤➤➤
➤➤➤➤➤
3" MIN.
3" MIN.
➤
➤
➤
➤
➤
➤ ➤ ➤ ➤ ➤
➤ ➤ ➤ ➤ ➤
3" 3"
MIN. MIN.
SPACING - FURRING
STRIP TO CONCRETE
Fastening to Steel
Your Ramset tool can be used for
fastening on the flat surfaces of
structural steel. When fastening into
steel, always maintain a minimum
spacing of 1-1/2" between fastenings
and 1/2" from any edge.
SPACING
STEEL TO STEEL