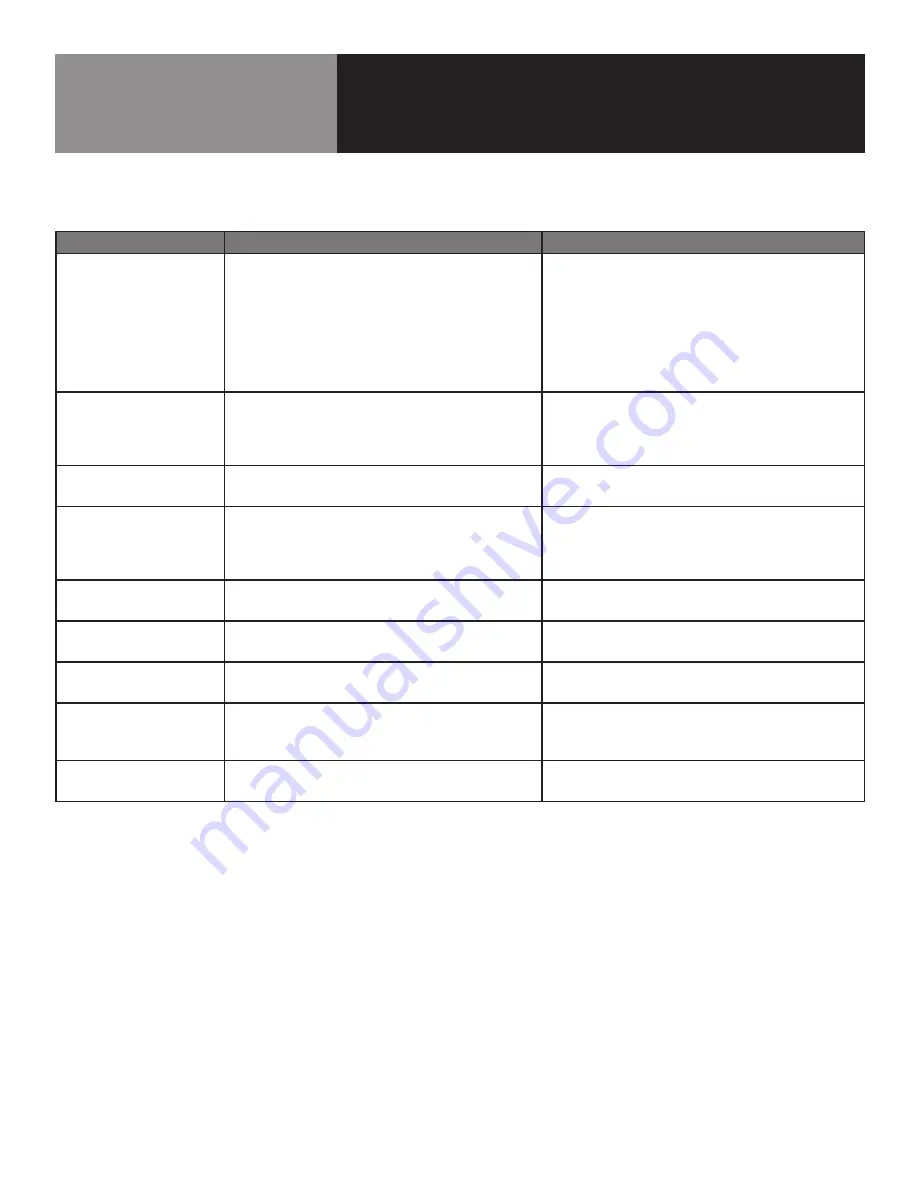
OM-51000 & 53000 SERIES 13
Troubleshooting
This unit is designed to operate smoothly and efficiently if properly maintained. However, the following is a list of checks to make in
the event of a problem. Wiring diagrams are found at the end of this manual.
SYMPTOM
POSSIBLE CAUSE
PROCEDURE
Unit does not run
1. No power to unit
2. Temperature control turned off
3. Temperature control faulty
4. Compressor overheated
5. Condenser fan faulty
6. Overload protector faulty
7. Compressor relay faulty
8. Compressor faulty
1. Plug in unit
2. Check temperature control
3. Test temperature control
4. Clean condenser coil
5. Service condenser fan
6. Test overload
7. Test relay
8. Call for service at 888-994-7636
Unit short cycles
1. Condenser coil dirty
2. Condenser fan faulty
3. Compressor faulty
4. Overload repeatedly tripping
1. Clean coil
2. Service fan and motor.
3. Call for service at 888-994-7636
4. Check outlet voltage
Unit runs constantly
1. Condenser coil dirty
2. Condenser fan faulty
1. Clean coil
2. Service condenser motor
Unit not cold enough
1. Temperature control set too high
2. Temperature control faulty
3. Condenser coil dirty
4. Refrigerant leaking or contaminated
1. Adjust control to lower setting
2. Test control
3. Clean coil
4. Call for service at 888-994-7636
Unit too cold
1. Temperature control set too low
2. Temperature control faulty
1. Adjust control to raise setting
2. Test control
Drawer Issues
1. Drawer tracks backwards
2. Roller bearings loose
1. Check installation of drawer track – page 12
2. Tighten bearings
Unit noisy
1. Compressor mountings loose or hardened
2. Condenser fan damaged or hitting fan shroud
1. Tighten or replace compressor mountings
2. Inspect condenser fan
Moisture around door or
frame
1. Breaker strip faulty
2. Frame heater faulty
3. Temperature control set too low
1. Inspect strips
2. Call for service at 888-944-7636
3. Adjust control to raise setting
Ice in drain pain or water
in bottom of unit or floor
1. Drain tube clogged
2. Unit not level
1. Clean drain
2. Adjust leveling feet
When in doubt, turn unit off and call for service and call for service at 888-944-7636.
Summary of Contents for 51000 Series
Page 22: ...22 OM 51000 53000 SERIES Electrical Schematic MODELS 51386 51395 ...
Page 25: ...OM 51000 53000 SERIES 25 ...
Page 26: ......
Page 27: ......