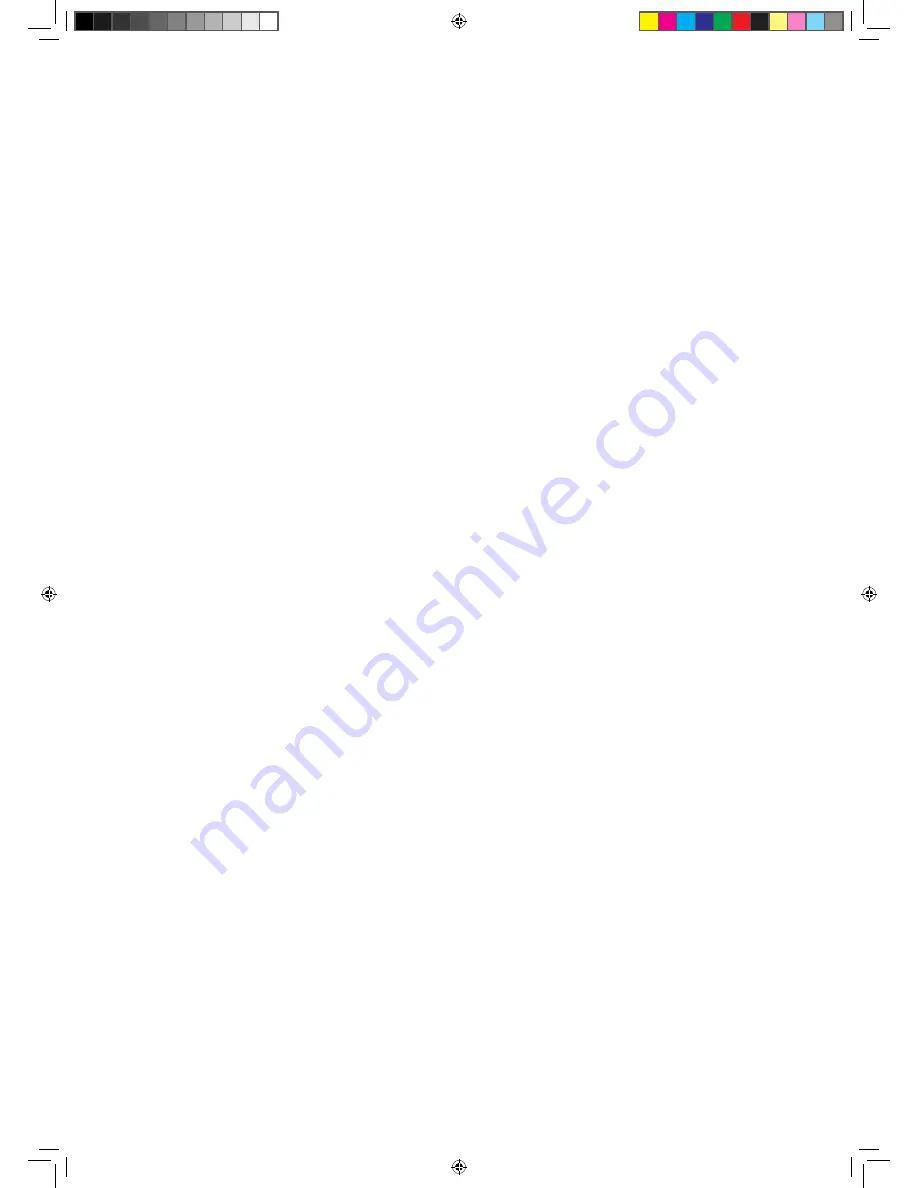
6
OPERATION AND INDICATORS
The SUPPLY indicator (green) will remain illuminated whenever the supply is present to the boiler.
The DEMAND indicator (amber) will illuminate on demand from the programmer and thermostats. It will flash (amber) for 1 to 2 minutes during which
it automatically carries out self-tests before allowing the boiler to produce heat. At the end of this period it will remain on steady (amber), until the
heating demand is satisfied.
The HEAT indicator (green bar graph) will illuminate when the boiler actually produces heat when the DEMAND indicator (amber) is steady. The
gradual build up in heating power of the boiler can be seen on the front panel. The HEAT indicator (green bar graph) also shows the boiler modulating
when it reaches operating temperature.
The FAULT indicator (red) will only illuminate if there is a fault. The DEMAND indicator (amber) will turn off and the HEAT indicator (green bar graph)
will flash a fault code to assist with fault diagnosis. The boiler will remain in this tripped state until it is reset. To reset a FAULT follow the ‘Fault Reset’
procedure (see page 15).
Minimum operating temperature setting for the boiler is approximately 65
o
C Maximum operating temperature setting is approximately 80
o
C.
CLEANING
Use only a damp cloth and mild detergent to clean the boiler outer casing. Do not use abrasive cleaners. Do not allow water inside the boiler. Do not
immerse in water.
INSTALLATION
Care must be taken when handling and connecting the boiler not to damage or stress it in any way. Prior to installation the boiler must be stored in a
dry safe place.
FITTING
The boiler must be mounted in an UPRIGHT position only with the electrical connections uppermost. Any deviation from vertical is unacceptable. The
boiler must be fixed to a wall before connecting pipework. When choosing the position for the boiler, ensure sufficient clearances to house the unit
and for servicing, 50mm minimum clearance each side of the boiler is required. A drain valve at the base of the boiler is strongly recommended. It
must be sited in a dry, ventilated position, frost free and not subjected to extremes of temperature.
PLUMBING / HEATING INSTALLATION
IT IS THE INSTALLER’S RESPONSIBILITY TO ENSURE THE INSTALLATION DOES NOT CONTRAVENE THE
REQUIREMENTS OF THE WATER BYLAWS OR LOCAL AUTHORITY REGULATIONS.
The boiler must be installed by a qualified, competent tradesman who is aware of and will comply with all relevant standards that are applicable: e.g.
Building Regulations, the Local Building Regulations, the Bylaws of the Local Water Authority and Undertaking and the relevant codes of practice, the
system must be flushed in accordance with BS.7593 and in accordance with the supplied instructions and drawings to ensure correct operation.
In operation, the boilers contain a very small amount of water in relation to the power input and so require a good flow rate of water to ensure correct
operation. Six Kilowatt models require a minimum flow of 6 litres/minute, and nine to twelve Kilowatt models require a minimum flow of 12 litres/
minute. Insufficient flow of water through the boiler will cause nuisance trip outs. The maximum temperature differential between input and output of
the boiler must not exceed 20
o
C. If the temperature across the boiler exceeds this then the flow rate is too low and could cause permanent damage
to the boiler.
All Flow and Return pipework to be 22mm to ensure minimum flow rate.