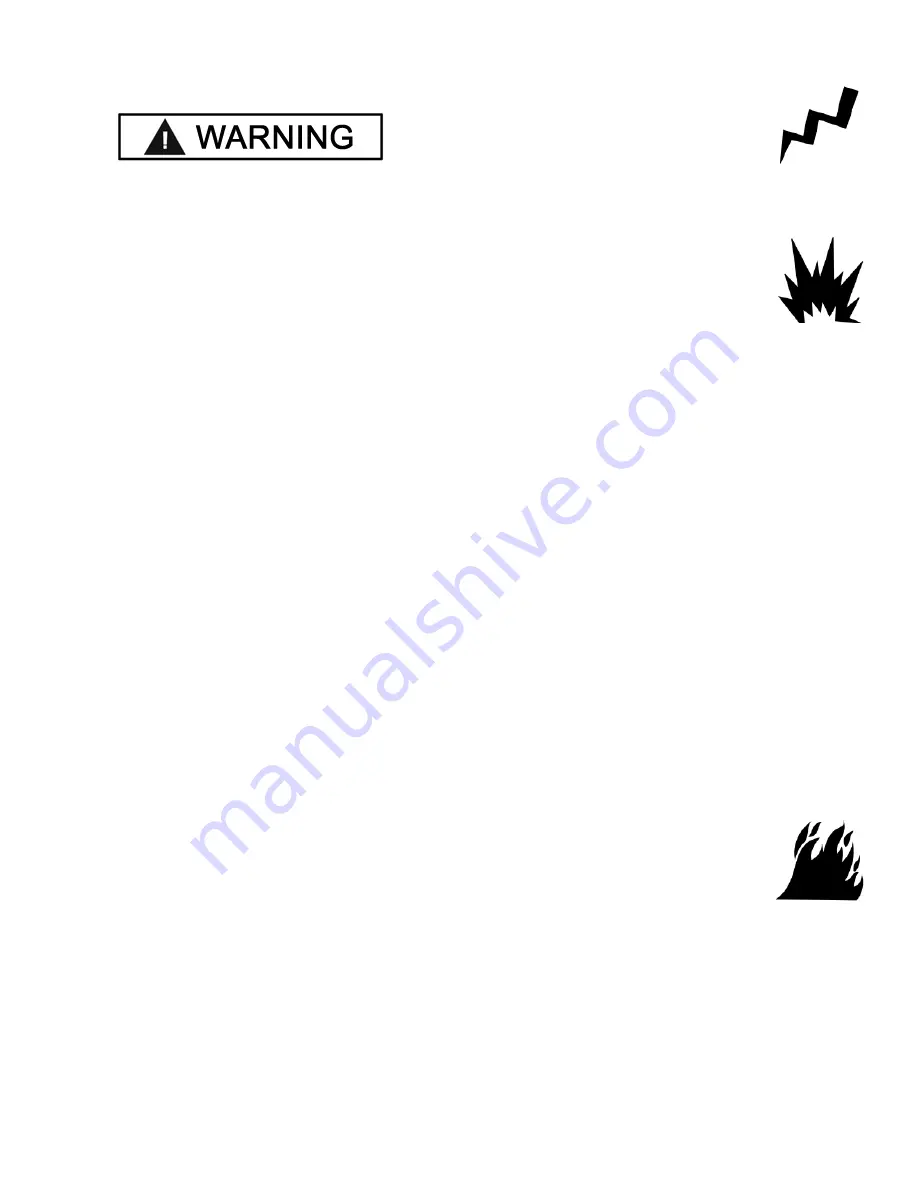
6
IMPORTANT SAFETY INSTRUCTIONS!
Read these safety instructions entirely!
1.
READ AND UNDERSTAND
all safety warning
procedures before operating lift.
2.
KEEP HAND AND FEET CLEAR
Remove hands
and feet from any moving parts.
3.
KEEP WORK AREA CLEAN
. Cluttered work areas
invite injuries.
4. Consider work area environment. Do not expose
equipment to rain.
DO NOT
use in damp or wet
locations. Keep area well lighted.
5.
ONLY TRAINED OPERATORS
should operate
this equipment. All non-trained personnel should be
kept away from work area. Never let
non-trained
personnel come in contact with, or operate machine.
6.
USE MACHINE CORRECTLY
. Use machine in the
proper manner. Never use adapters other than what is
approved by the manufacturer.
7.
DO NOT
override or disable safety valves and/or
devices.
8.
ALWAYS INSURE
that the safeties are engaged
before any attempt is made to work on or near
vehicle.
9.
DRESS PROPERLY
. Non-skid steel-toe footwear
is recommended when operating machine.
10.
GUARD AGAINST ELECTRIC SHOCK
. This
equipment must be grounded while in use to protect the
operator from electric shock. Never connect the green
power cord wire to a live terminal. This is for ground
only.
11.
DANGER!
The motor on this machine contains high
voltage. Disconnect power at the
receptacle before performing any
electrical repairs. Secure plug so that it
cannot be accidentally plugged in during
service.
12.
WARNING! RISK OF EXPLOSION
. This
equipment has internal arcing or sparking
parts which should not be exposed to flam-
mable vapors. This machine should not be
located in a recessed area or below floor
level.
13.
MAINTAIN WITH CARE
. Keep unit clean for
better and safe performance. Follow manual for proper
lubrication and maintenance instructions. Keep control
pedals and/or buttons dry, clean and free from grease
and oil.
14.
STAY ALERT
. Watch what you are doing. Use
common sense. Be aware.
15.
CHECK FOR DAMAGED PARTS
. Check for
condition of all moving parts, breakage of parts or any
condition that may affect the machines operation. Do
not use if any component is broken or damaged.
16.
NEVER
remove safety related components or
device from the machine. Do not use if safety related
components are damaged or missing.
17. To reduce fire hazard, keep engine/
motor exterior free of oil, solvent, or
excessive grease.
18. Unreadable and missing warning labels must be
replaced immediately. Do not use the tire changer
if one or more labels are missing. Do not add any
object that could prevent the operator from seeing
the labels.
Summary of Contents for R23
Page 25: ...25...
Page 26: ...26 R23 00 00 REVISION A 22 Tire changer...
Page 44: ...44 3 7 3 5 66 0 PL330B 00 00 REVISION A 04...