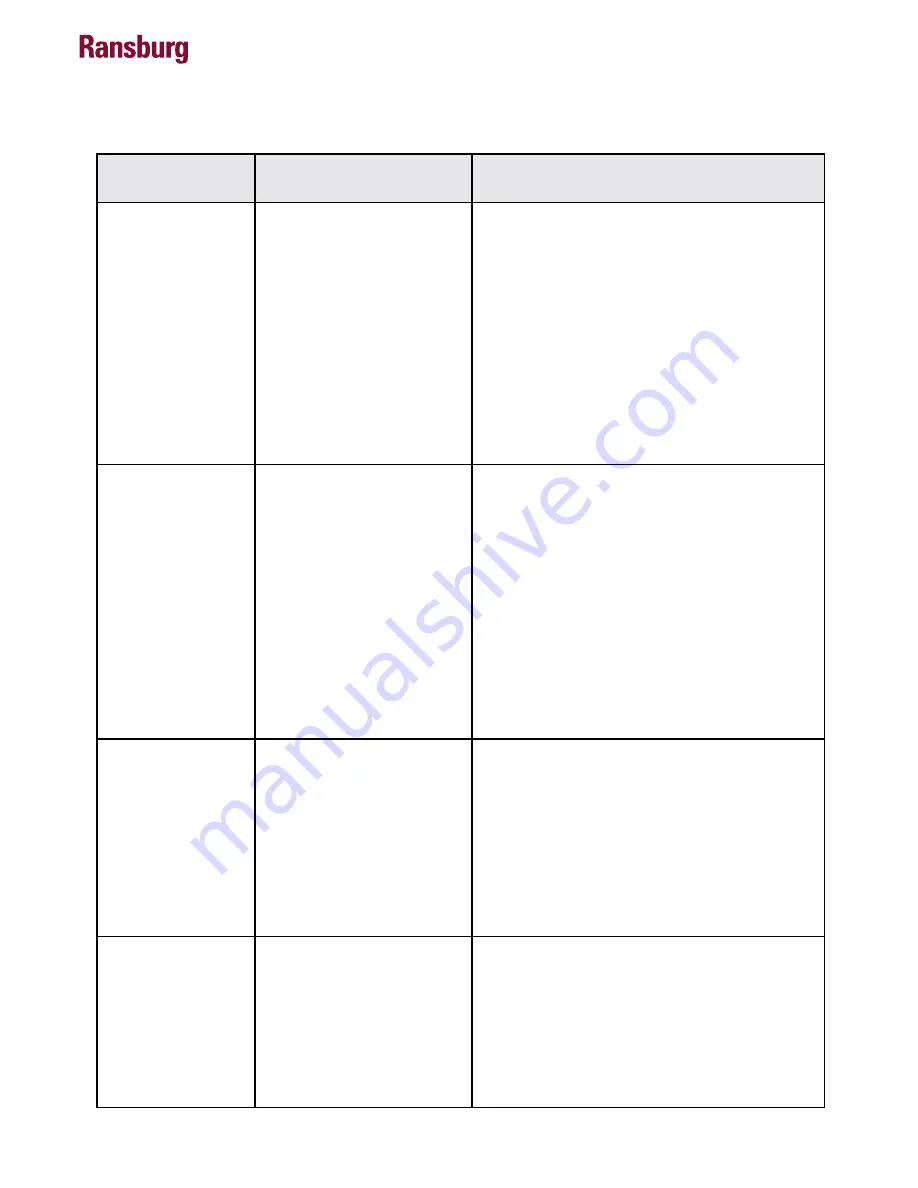
TROUBLESHOOTING GUIDE
General Problem
Possible Cause
Solution
Poor Atomization
and Distribution
Poor Wraparound
Paint Wraps Back On
Operator
No Paint Delivery
1. Partially clogged nozzle
2. Low fluid pressure
3. Viscosity too high
4. Improper nozzle
5. Badly worn nozzle
6. High voltage electrode bent
7. Low shaping air pressure
1. Poor atomization
2. Excessive exhaust veloc-
ity
3. Excessive fluid pressure
4. Applicator held too close
to target
5. Paint too conductive
6. Poor target ground
1. Poor ground on parts
2. Applicator held too far
from parts
3. Booth exhaust insufficient
or improperly routed
4. Improper spray technique
1. Clogged nozzle
2. Clogged hose or filters
3. No pressure at paint pump
1. Clean out.
2. Increase pump air pressure.
3. Try nozzle with narrower fan or smaller orifice.
4. Try nozzle with narrower fan or smaller orifice.
5. Replace.
6. Straighten electrode or replace nozzle
assembly.
7. Readjust shaping air pressure.
1. See "Poor Atomization and distribution".
2. Reduce (with code limits).
3. Reduce air pressure to pump.
4. Hold applicator further back.
5. Consult Ransburg technical assistance.
6. Check ground integrity from target through
support to ground.
1. Check that parts are fully grounded, strip
workholders.
2. Hold applicator closer.
3. Increase, or adjust direction, change booth
filter.
4. Keep applicator directed at work.
1. Blow out nozzle.
2. Clean.
3. If pump air supply OK, consult pump manual.
Vector AA90 Applicators - Maintenance
43
AH-07-01.10