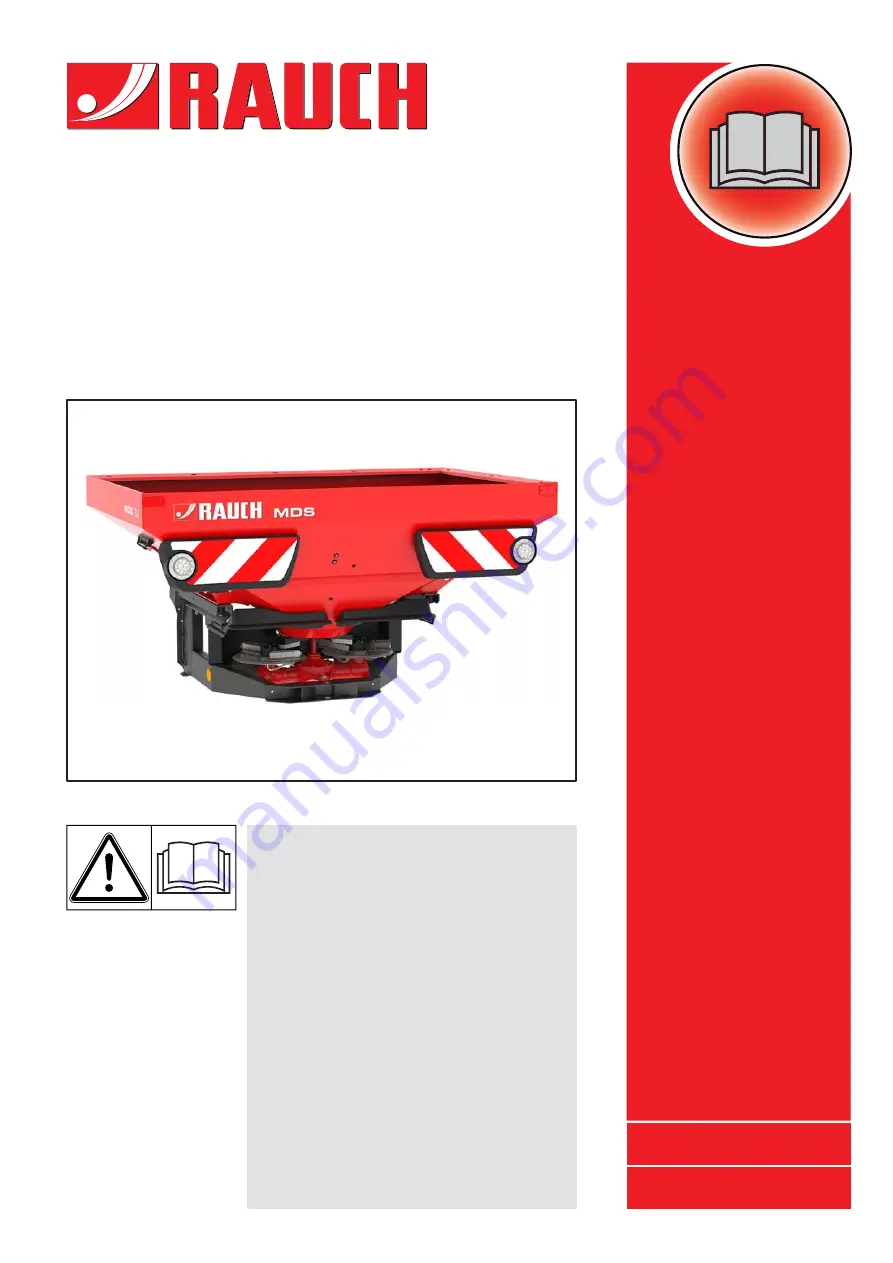
INSTRUCTION MANUAL
MDS
8.2/14.2/18.2/20.2
5902916-
a
-en-0819
Please read carefully be-
fore using the machine.
Keep for future reference.
This instruction manual/assembly instruc-
tion is to be considered as part of the ma-
chine. Suppliers of new and second-hand
machines are required to document in wri-
ting that the instruction manual/assembly
instruction was delivered with the machi-
ne and handed over to the customer.
Original instructions
Summary of Contents for MDS 14.2
Page 8: ...Intended use 1 2...
Page 28: ...Safety 3 22...
Page 38: ...Technical data 4 32...
Page 42: ...Axle load calculation 5 36...
Page 44: ...Transportation without tractor 6 38...
Page 86: ...Machine settings 8 80...
Page 96: ...Calibration and discharging residual material 9 90...
Page 110: ...Important information on spreading 10 104...
Page 114: ...Faults and possible causes 11 108...
Page 146: ......