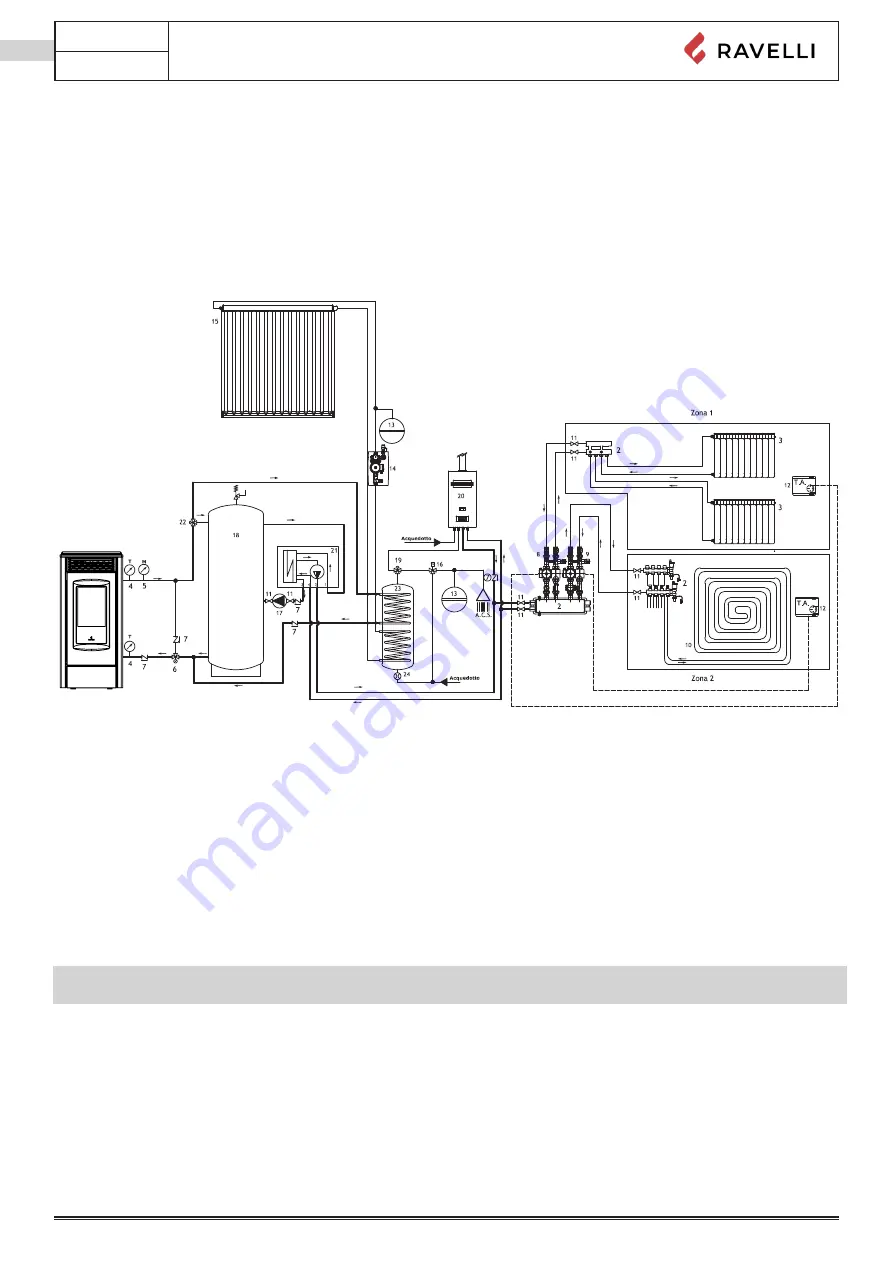
Use and maintenance manual Touch Radio Hydro
Pag.28
Rev.0 18/05/2021
EN
Diagram 3 (boiler buffer tank sensor)
Diagram 3 is to be used in a system where both a water buffer tank for the heating system and a DHW boiler are present.
The operating logic is similar to that of Diagram 1. Also in this type of circuit, the boiler water temperature is managed by the stove
and room temperature by a control unit (not supplied) that controls the buffer tank and any zone valves. The buffer tank temperature
is controlled by the thermo-stove through a sensor.
The diagram shown here is indicative and may not display all the components required to properly operate the system. Rely on a
qualified thermal technician for the hydraulic system design.
System water characteristics
The chemical-physical characteristics of the system and replenishing water are important for the proper operation and service life
of the thermo-stove; in fact, with the use of low quality water the most frequent problem is due to scale, which causes a reduction in
heat exchange and generates corrosion.
Therefore, we invite you to check the quality and hardness of the water with your supplier.
We recommend the installation of a softener (limescale filter) in correspondence with the system loading. This precaution becomes
essential in the conditions listed below:
•
medium and high water hardness (> 15 ° f)
•
considerable quantities of make-up water or subsequent fillings
•
plants of a certain complexity and size.
⚠
National and local laws may require the use of water softening systems. The technician responsible for the plumbing
installation is invited to check what is reported in the regulations in force.
System water load
Once the plumbing connections have been completed, the appliance and its system can be LOADED.
To facilitate the escape of air, unscrew the cap of the automatic vent valve (Jolly valve) of the thermo stove and open the vent valves
in the system. Bleed the air even after the first hours of operation and, if necessary, also periodically (for example in the event of
noises and gurgling).
The filling pressure of the COLD system must be 1 bar (100 kPa). In order to ensure correct operation of the thermo stove, the HOT
pressure must be approximately 1.5 bar (150 kPa).
If during operation the system pressure drops to values below the minimum indicated above, the user must bring it back to the initial
value by acting on the filling tap.
It is possible to load the system and keep it at the correct pressure also by means of a special automatic filling unit.
Periodically check the system water pressure, using the appropriate function on the display.
Stufa a Pellet
LEGEND
1- Pellet stove
2- Distribution manifolds
3- Radiators
4- Thermometer
5- Pressure gauge
6- Anti-condensation valve
7- Check valve
8- Group of direct distribution
9- Thermostatic distribution unit
10- Radiant panel (underfloor heating)
11- Shut-off valve
12- Thermostat
13- Expansion vessel (tank)
14- Pump station for solar thermal system
15- Solar thermal collector
16- Thermostatic mixing valve
17- Booster pump
18- Buffer tank
19- Motorised three-way valve with spring return
20- Gas boiler
21- Power separation system
22- Motorised three-way valve
23- DHW storage
24- Flow switch
Summary of Contents for Hydro
Page 1: ...USE AND MAINTENANCE MANUAL HYDRO Handheld Touch Radio Hydro...
Page 2: ......
Page 53: ......
Page 54: ......
Page 55: ......