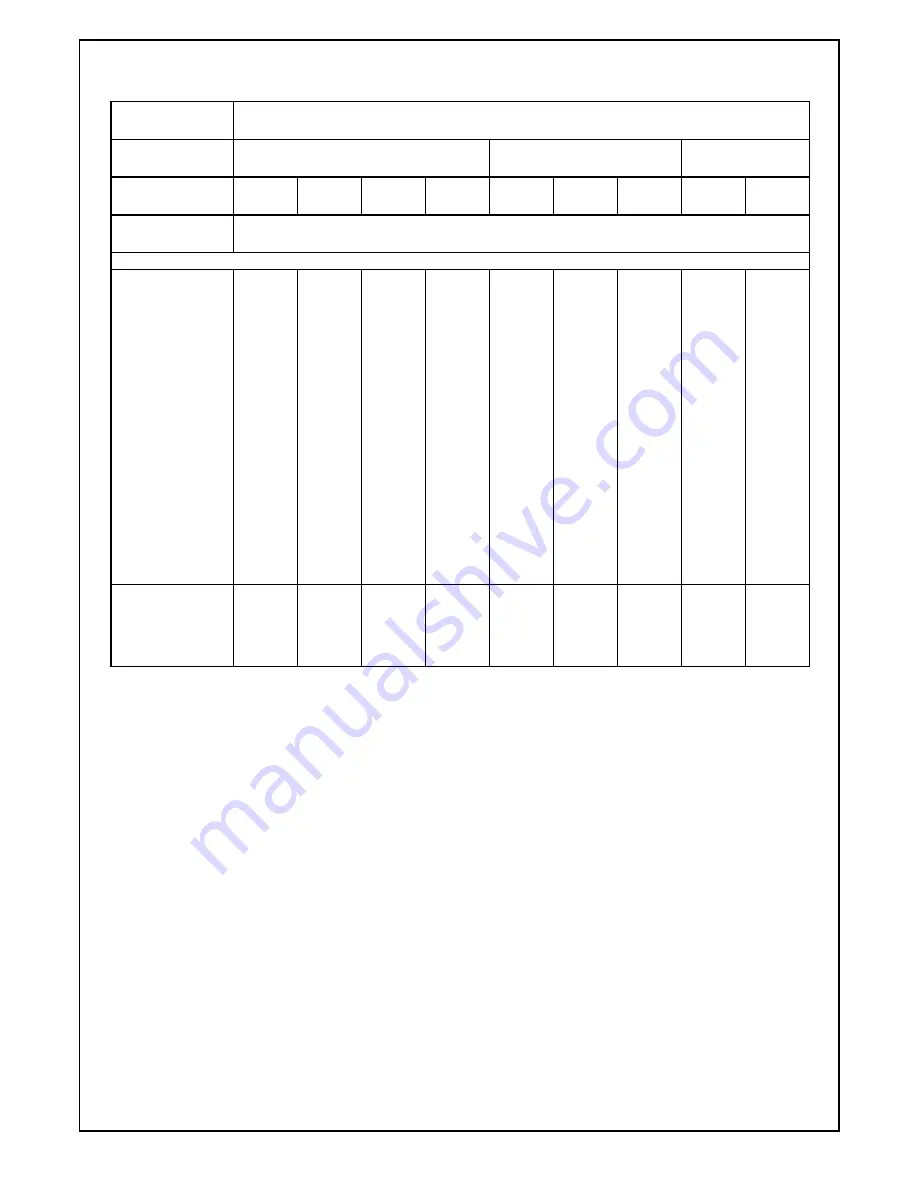
14
B) Where fitting of a make up vessel would
be difficult, RE-PRESSURING of the system
can be done. See section on FILLING. If the
capacity of the central heating system should
exceed 110 Litres, an additional vessel should
be installed on the return to the combination
boiler from the heating system (Fig. 7).
Guidance on vessel sizing is given in (Table
3).
Reference should be made to British Gas
Publications, «Material and Installation
Specifications for Domestic Central Heating
and Hot Water». Draining taps should be
at least 1/2” in BSP nominal size and be in
accordance with BS 2879.
4.8.8
Installation to an existing central heating
system.
The combination boiler is designed to operate
on a sealed system only. Therefore if the
existing system is of the open water type it will
have to be modified to comply with BS 5376
Part 2.
Before installing a new combination boiler to
an existing system, flush out the old system
with a recommended descaling agent.
It is important that the correct concentration
of the water treatment product is maintained
in accordance with the manufacturers’
instructions.
If the boiler is installed in an existing system
any unsuitable additives
MUST
be removed by
thorough cleansing.
BS 7593:1992 details the steps necessary
to clean domestic central heating system.
Also check pipework and renew any corroded
pipework or fittings. Valve glands must be
repacked or replaced wherever necessary and
any defective controls exchanged.
4.8.9
WATER TREATMENT
This boiler has a secondary ALUMINIUM alloy
heat exchanger Ravenheat recommended only
the use of FERNOX- COPAL or SENTINEL
X100 water treatment products, which must
be used in accordance with the manufacturers
instructions. For further information contact:
Fernox Manufacturing Co. Ltd.
Tel 01799 550811
Sentinel Division Betz Dearborn Ltd.
Tel. (0151) 424 5351
Safety
valve setting (bar)
3.0
Vessel charge
pressure (bar)
0.5
1.0
1.5
Initial system
pressure (bar)
0.5
1.0
1.5
2.0
1.0
1.5
2.0
1.5
2.0
Total water
content of system
EXPANSION VESSEL VOLUME (LITRES)
Litres
25
50
75
100
125
150
175
200
225
250
275
300
325
350
375
400
425
450
475
500
2.1
4.2
6.3
8.3
10.4
12.5
14.6
1 6 . 7
1 8 . 7
2 0 . 8
2 2 . 9
25.0
2 7 . 0
2 9 . 1
31 .2
33.3
3 5 . 4
37.5
39.6
41.6
3.5
7.0
10.5
14.0
17.5
21.0
24.5
28.0
31 .5
35.0
38.5
42.0
45.5
49.0
52.5
56.0
59.5
63.0
66.5
7 0 . 0
6.5
12.9
19.4
25.9
32.4
38.8
45.3
51 .8
58.3
64.7
71 .2
7 7 . 7
84.1
90.6
97 .1
103.6
110.1
116.5
123.0
125.9
13.7
27.5
41.3
55.1
68.9
82.6
96.4
110.2
124.0
137.7
151 .5
165.3
179 .1
192.8
206.6
220.4
239.2
247.9
261 .7
275.5
2.7
5.4
8.2
10.9
13.6
16.3
19.1
21.8
24.5
27.2
30.0
32.7
35.7
38 .1
40.9
43.6
46.3
49.0
51 .8
54.5
4.7
9.5
14.2
19.0
23.7
28.5
33.2
38.0
42.7
47.5
52..2
57.0
61 .7
66.5
71 .2
7 6 . 0
80.7
85.5
90.2
95.0
10.3
20.6
30.9
41.2
51.5
61.8
72.1
82.4
92.7
103.0
113.3
123.6
133.9
144.2
154.5
164.8
175.1
185.4
195.7
206.0
3.9
7.8
11.7
15.6
19.5
23.4
27 .3
31.2
35 .1
39.0
42.9
46.8
50.7
54.6
58.5
62.4
66.3
70.2
74.1
7 8 . 0
8.3
16.5
24.8
33.1
41.3
49.6
57.9
66.2
74.5
82.7
91.0
99.3
107.6
115.8
124.1
132.4
140.7
148.9
157.2
1 6 5 . 5
For system volumes
other than those given
above, multiply the
system volume by
the factor across
0.0833
0.140
0.259
0.551
0 .109
0.190
0.412
0.156
0.331
SIZING OF ADDITIONAL EXPANSION VESSEL: TABLE 3
Deduct from the value given in the table the 7 litre vessel supplied.
Note: This pressure can be increased up to 1.5 bar to suit high static head situations, see item 10, other appliance components in the
SERVICING INSTRUCTIONS.
Summary of Contents for 780 Series
Page 2: ......
Page 7: ...7 Fig 3 OVERALL DIMENSION ...
Page 34: ...34 Fig 45 Fig 44 Fig 46 ...
Page 36: ...36 Fig 48 Fig 47 Fig 49 Fig 50 Fig 51 ...
Page 42: ...Fig 59 42 SECTION 9 ELECTRICAL SYSTEM DIAGRAM ...
Page 46: ...79 83 105 46 50 27 16 39 17 2 22 100 1 4 5 11 8 SECTION 11 ...
Page 49: ...49 ...
Page 50: ...COD 0017LIB06010 2 03 2010 ...