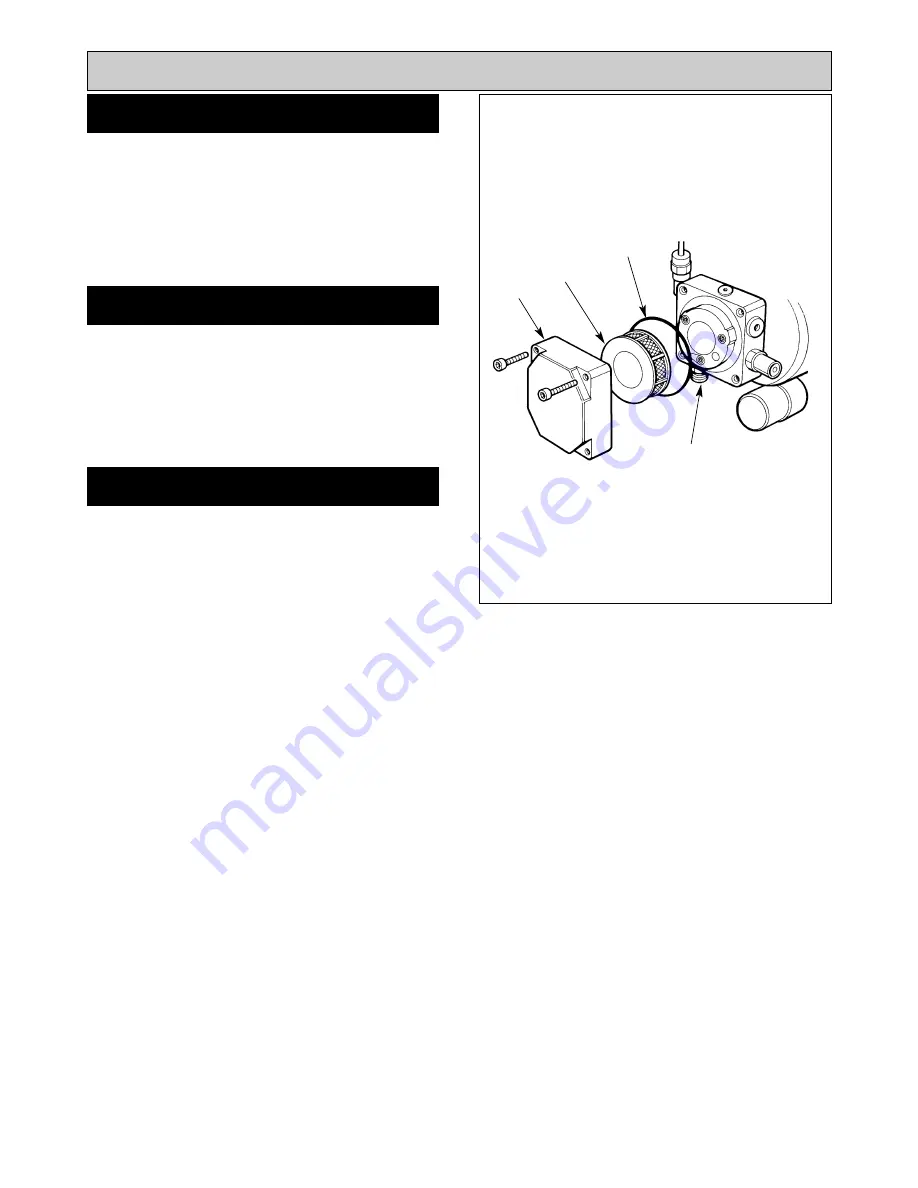
To carry out any servicing on the oil pump. Turn off the oil
line isolating valve near to the appliance.
SEE FIG. 15
1.
Remove 4 socket head screws.
2.
Remove filter.
3.
Wash with clean petrol or paraffin.
4.
Re-assemble in reverse order.
1.
Turn OFF the line isolating valve fitted prior to the oil
line filter.
2.
Follow manufacturer’s instructions to remove filter
element from the housing, taking care to collect
Kerosene residue from the filter housing.
3.
Wash filter thoroughly in clean petrol or paraffin.
4.
Re-assemble in reverse order.
NOTE:
Flexible fuel hose (s) must be replaced at each
service.
14
INTRODUCTION
OIL PUMP STRAINER CLEANING
Oil Pump Servicing
OIL LINE FILTER CLEANING
Fig. 15
DESN 512002
COVER
STRAINER
FUEL INLET
SEAL
Summary of Contents for Heatranger 440
Page 9: ...Cleaning Fig 6A 9...
Page 22: ...22 Fig 28 DESN 513150 Replacement of parts Electrical controls...
Page 30: ...30 Electrical Controls CONTROL CIRCUIT BOILER Fig 37 L1...
Page 31: ...31 Electrical Controls CONTROL CIRCUIT COOKER Fig 38 L2 L2 KB MODEL ONLY...
Page 32: ...32 Fault Finding WIRING DIAGRAM APPLIANCE 440 460 480K 499K Fig 39...
Page 37: ...Fault Finding 37 Fig 41A DESN 516838...
Page 38: ...38 Fault Finding...
Page 39: ...39 Fault Finding...
Page 40: ...40 Fault Finding...
Page 41: ...41 Fault Finding...
Page 43: ...43...