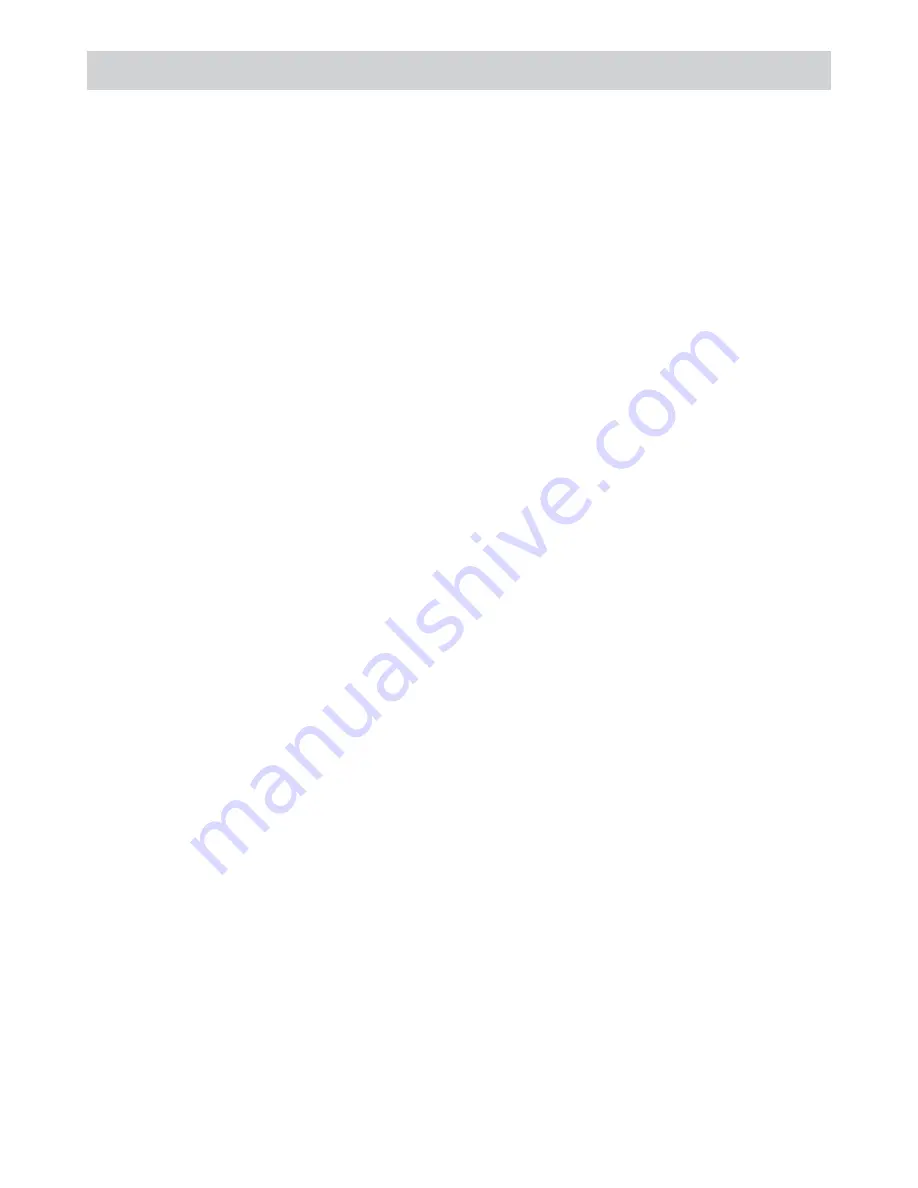
SECTION
CONTENTS
PAGE
CONSUMER PROTECTION
3
HEALTH & SAFETY
3
TECHNICAL DATA
4
SITE REQUIREMENTS
INTRODUCTION
5
IMPORTANT
5
REGULATIONS
5
GAS SUPPLY
5
LOCATION 5
ELECTRICAL SUPPLY
6
FLUE SYSTEM
7-9
FLUE TERMINAL LOCATION
10
INSTALLATION
11
PCB CONNECTIONS
12
INSTALLATION REQUIREMENTS
CLEARANCES
13
PRELIMINARY INSTALLATION
13
SITE LOCATION
14
SETTING COMBUSTION
15
INSTALLATION INSTRUCTIONS
BURNER ACCESS
16
ELECTRICAL CONNECTION
16
BOILER CONTROL (BURNERTECH BURNER)
17
ELECTRICAL CHECK (BURNERTECH BURNER)
17
COMBUSTION DISCHARGE DEVICE (BURNERTECH
17
BURNER)
OVERHEAT SAFETY THERMOSTAT
17
BURNER CONTROL (ECOFLAM BURNER)
18
ELECTRICAL CHECK (ECOFLAM BURNER)
18
COMBUSTION DISCHARGE DEVICE (ECOFLAM
18
BURNER)
ANCILLARY CONTROLS CHECK
19
INSTRUCT THE USER
19
WIRING DIAGRAM
WIRING DIAGRAM - APPLIANCE
20
SINGLE CHANNEL PROGRAMMER
SINGLE CHANNEL PROGRAMMER
21
Contents
2
Summary of Contents for XT
Page 20: ...20 Wiring Diagram FIG 21 WIRING DIAGRAM APPLIANCE ...
Page 22: ...22 ...
Page 23: ...23 ...