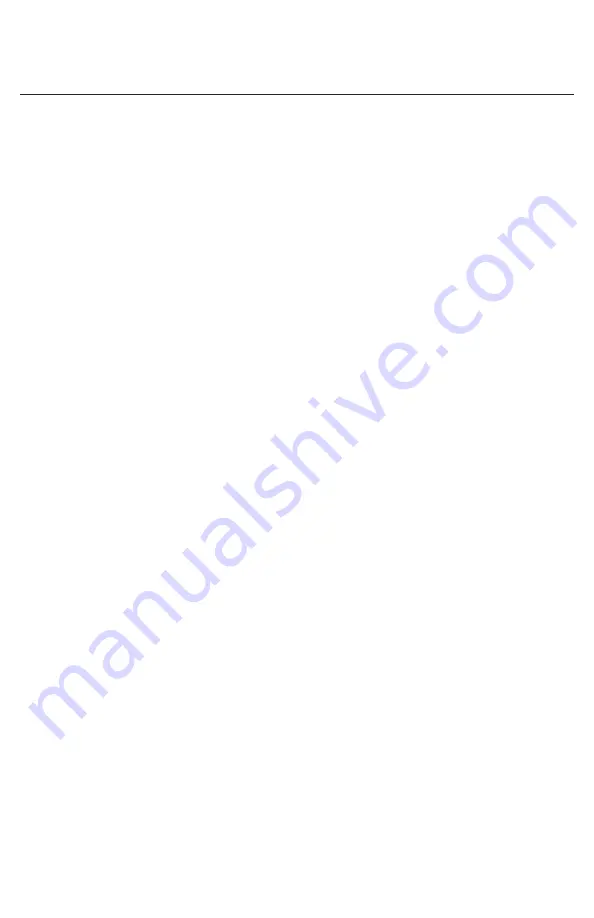
T415 Operation & Service Manual
800.392.2686
19
Safety
Sound Level Information
The operator Equivalent Sound Pressure Level is used to
measure a work cycle sound exposure level
Hearing protection may be needed when the machine is
operated with an open operator station for extended periods
in a noisy environment. Hearing protection may be needed
when the machine is operated with a cab that is not properly
maintained or when the doors and windows are open for
extended periods or in a noisy environment.
Vibration Data Information concerning
hand/arm vibration level
When the machine is operated according to the intended
use, the hand/arm vibration of this machine is rated by meter
per second squared.
Note: Vibration levels are influenced by many different
parameters listed below.
• Operator training, behavior, mode, and stress
• Job site organization, preparation, environment,
weather and material
• Machine type, quality of the seat, quality of the
suspension system, attachments, and condition of the
equipment.
Guidelines for Reducing Vibration Levels
on Equipment
Properly adjust machines. Properly maintain machines.
Operate machines smoothly. Maintain the conditions of the
terrain. The following guidelines can help reduce the whole
body vibration level:
1. Use the right type and size of machine, equipment,
and attachments.
2. Maintain machines according to the manufacturer’s
recommendations.
a: Tire pressures
b: Brake and steering systems
c: Controls, hydraulic system and linkages
3. Keep the terrain in good condition.
a. Remove any large rocks or obstacles.
b. Fill any ditches and holes.
c. Provide machines and schedule time in order to
maintain the conditions of the terrain.
4. Use a seat that meets “ISO 7096”. Keep the seat
maintained and adjusted.
a. Adjust the seat and suspension for the weight
and the size of the operator.
b. Inspect and maintain the seat suspension and
adjustment mechanisms.
5. Perform the following operations smoothly.
a. Steer
b. Brake
c. Accelerate
d. Shift the gears
6. Move the attachments smoothly.
7. Adjust the machine speed and the route in order to
minimize the vibration level.
a. Drive around obstacles and rough terrain.
b. Slow down when it is necessary to go over rough
terrain.
8. Minimize vibrations for a long work cycle or a long
travel distance.
a. Haul the machines between workplaces.
9. Less operator comfort may be caused by other risk
factors. The following guidelines can be effective in
order to provide better operator comfort:
a. Adjust the seat and adjust the controls in order to
achieve good posture.
b. Adjust the mirrors in order to minimize twisted
posture.
c. Provide breaks in order to reduce long periods
of sitting.
d. Avoid jumping from the cab.
e. Minimize repeated handling of loads and lifting
of loads.
f. Minimize any shocks and impacts during sports
and leisure activities.
Guards (Operator Protection)
There are different types of guards that are used to protect
the operator. The machine and the machine application
determines the type of guard that should be used.
A daily inspection of the guards is required in order to check
for structures that are bent, cracked or loose. Never operate
a machine with a damaged structure.
The operator becomes exposed to a hazardous situation if the
machine is used improperly or if poor operating techniques
are used. This situation can occur even though a machine is
equipment with an appropriate protective guard.
Follow the established operating procedures that are
recommended for your machine.
Rollover Protective Structure
(ROPS), Falling Object Projective
Structure (FOPS) or Tip Over
Protection Structure (TOPS)
The TOPS/FOPS Structure (if equipped) on your machine is
specifically designed, tested and certified for that machine.
Any alteration or any modification to the ROPS/FOPS
Structure could weaken the structure. This places the
operator into an unprotected environment. Modifications or