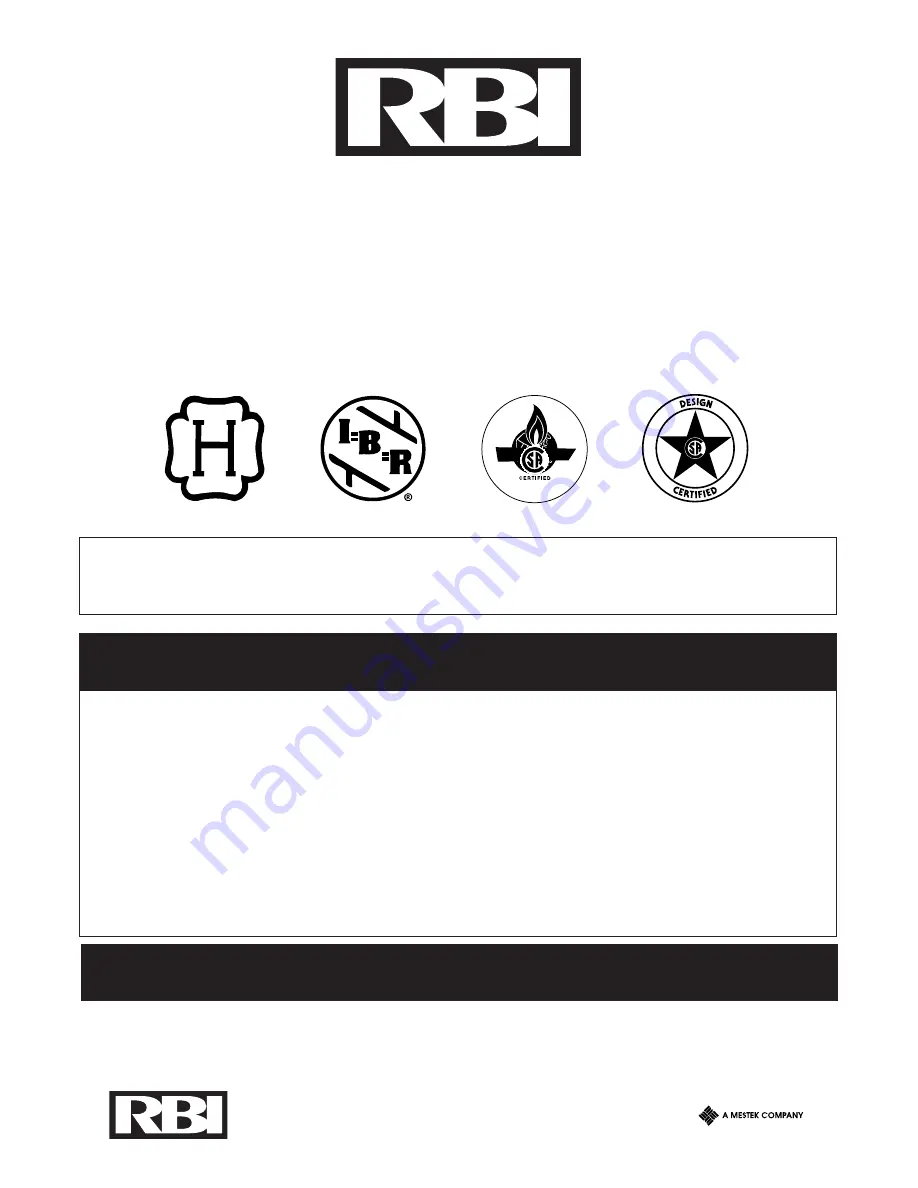
FUTERA II SERIES FINNED COPPER
GAS BOILERS (MODEL FB) &
WATER HEATERS (MODEL FW)
INSTALLATION & OPERATION MANUAL
INSTALLER, THESE INSTRUCTIONS TO BE AFFIXED ADJACENT TO THE BOILER / WATER HEATER.
CONSUMER, RETAIN THESE INSTRUCTIONS FOR FUTURE REFERENCE PURPOSES.
WARNING: If the information in this manual is not followed exactly, a fire
or explosion may result causing property damage, personal injury or loss of life.
Do not store or use gasoline or other flammable vapors and liquids in the vicinity of
this or any other appliance.
WHAT TO DO IF YOU SMELL GAS:
• Do not try to light any appliance.
• Do not touch any electrical switch. Do not use any phone in your building.
• Immediately call your gas supplier from a neighbor’s phone. Follow the gas
supplier’s instructions.
• If you cannot reach your gas supplier, call the fire department.
Installation and service must be performed by a qualified installer, service agency or
the gas supplier.
DESIGNED AND TESTED ACCORDING TO A.S.M.E. BOILER AND PRESSURE
VESSEL CODE, SECTION IV FOR A MAXIMUM ALLOWABLE WORKING PRESSURE
OF 160 PSI,
1103 kPa
, WATER.
FTII-IOM-5
260 North Elm Street
1300 Midway Boulevard
Westfield, MA 01085
Mississauga, Ontario L5T 2G8 Canada
Phone: (413) 568-9571
Phone: (905) 670-5888
Fax: (413) 568-9613
Fax: (905) 670-5782
www.rbiwaterheaters.com
WARNING: Failure to properly vent this unit can cause excessive amounts of carbon
monoxide resulting in severe personal injury or death!