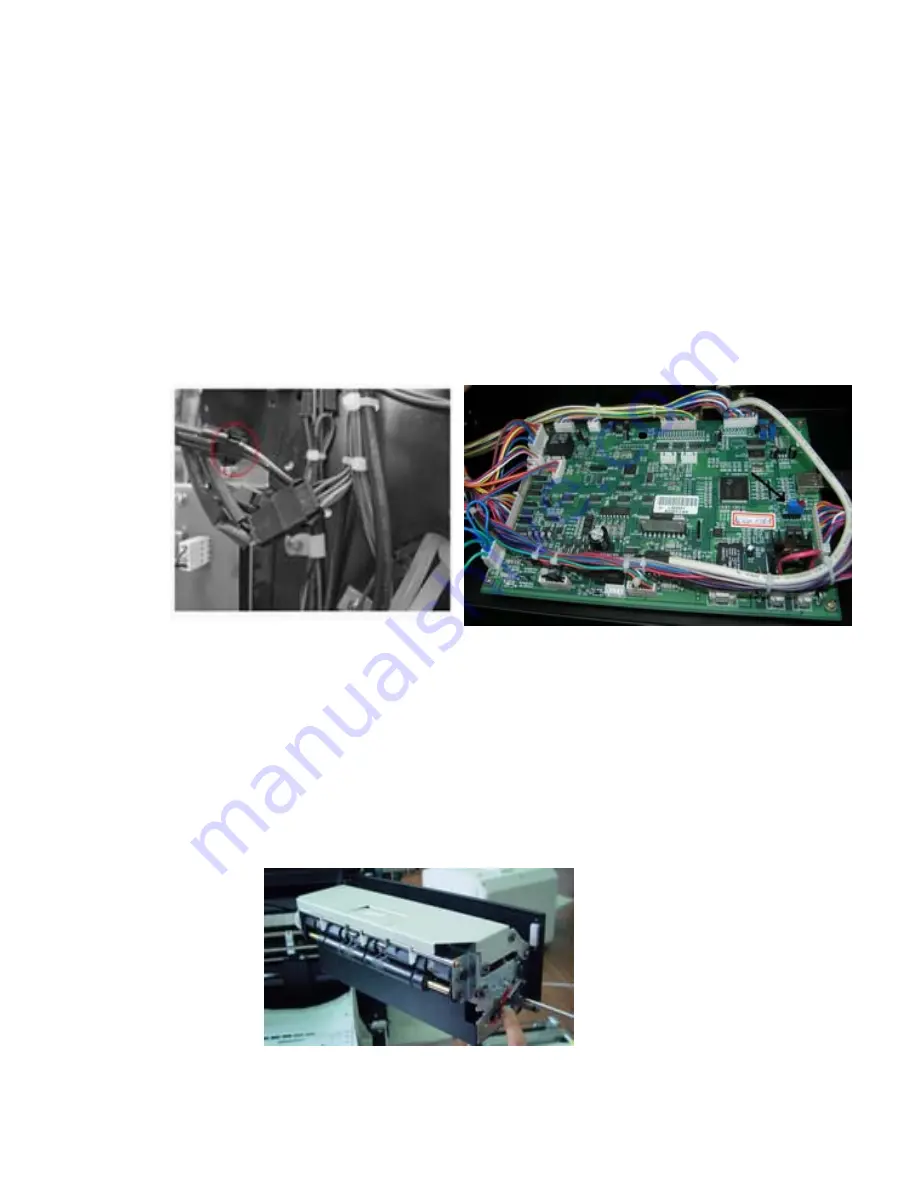
Section 4. Master eject unit
1. Outs Error
Solution: a. Take out the drum and insert the drum,press master-making to start.
try again if fail to clear the error.
b. Test the signal voltage of the master eject sensor (send and receive),make sure there
is no master blocking the send and receive sensor.
c. Enter unit test and check the clamper drive position sensor, see if the sensor is ok.
d. Enter unit test and check the master eject motor ( conntector wire, power 24V)
e. Check the clamper drive part..If it is wrong, adjust (Page 20)
2. Master disposal box full
Solution: a. Check if there is the master disposal core in the box and empty the
b. Check the Master disposal box mirco switch(enter unit test and test).
Standard:
sensor unblocked : 0-0.2v
sensor blocked : 3-3.3v
master disposal box.
- 42-