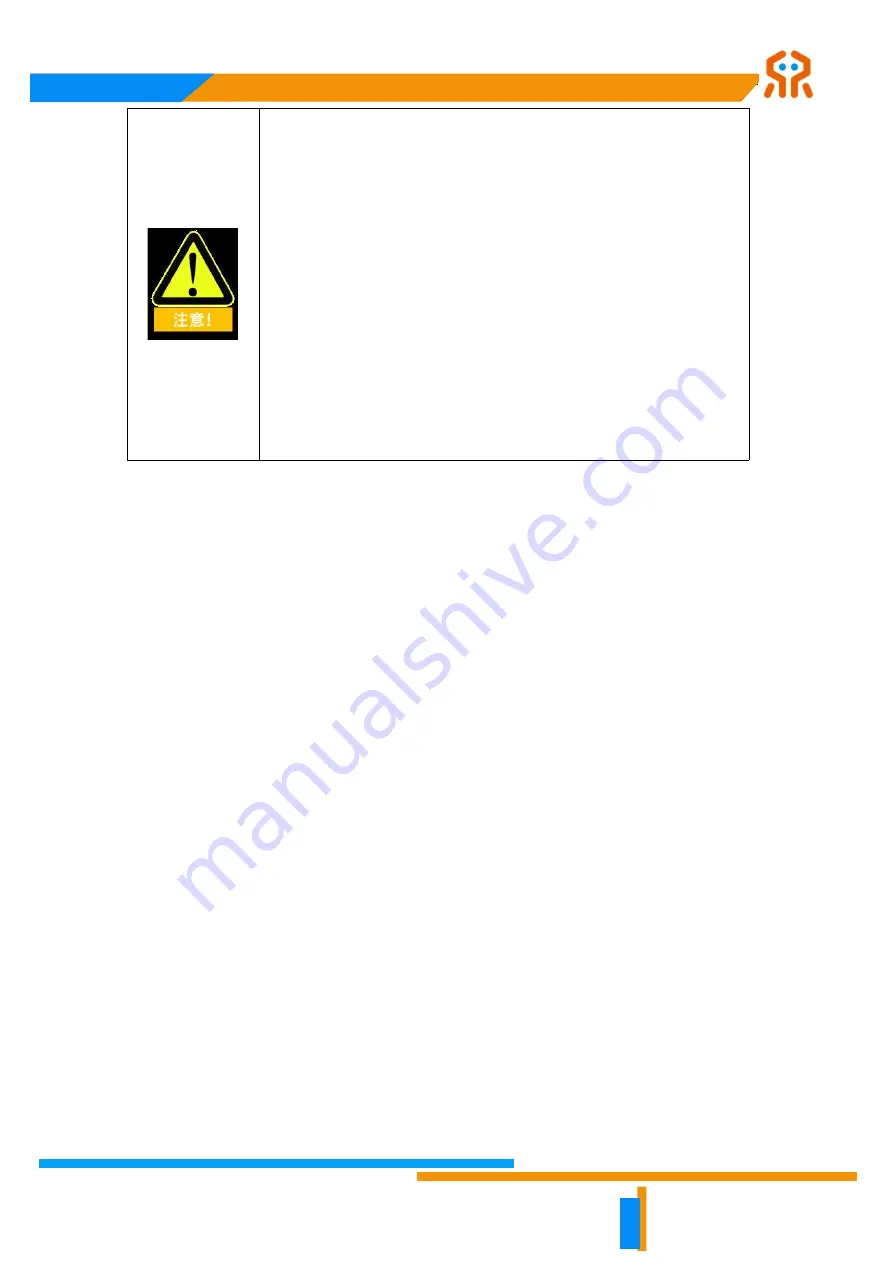
生活美好,臂不可少
http://www.realman-robotics.com
10
1. When a robot is connected to or collaborating with machinery
that can cause damage to the robot, it is highly recommended that
all functionalities and procedures of the robot should be checked
separately. It is recommended to use a temporary workspace outside
of the workspaces of other machinery to inspect the robot program.
2. We, as RealMan Intelligent Technology (Beijing) Co., Ltd., will
not be responsible for the damage to the robot or personal injury
caused by human reason.
3. Do not expose the robot to permanent magnetic fields. Strong
magnetic fields can damage the robot.
1.4 Responsibility and Regulation
RML63 robots itself is not complete to accomplish certain tasks but can be combined
with other peripheral equipment to achieve that. Therefore, the information contained
in this manual does not indicate the design, installation, and operation of a complete
robot, nor does it include all the possibilities that may affect the safety of the
peripheral equipment of such a complete system. The safety of a complete robot
installation depends on how the robot is ensembled. The integrator is required to
conduct a risk assessment for the design and installation of the complete system in
accordance with the laws, regulations and safety codes and standards of the host
country or region. Risk assessment is one of the most important tasks that must be
performed by an integrator. An integrator can perform the risk assessment process by
referring to the following standards. Risk assessment is one of the most important
tasks that must be performed by an integrator. An integrator can perform the risk
assessment process by referring to the following standards.
ISO 12100:2010 Machinery Safety-General Design Principles-Risk
Assessment and Risk Reduction.
ISO 10218-2:2011 Robots and Robotic Equipment-Safety Requirements-Part
2: Industrial Robot System and Integration.