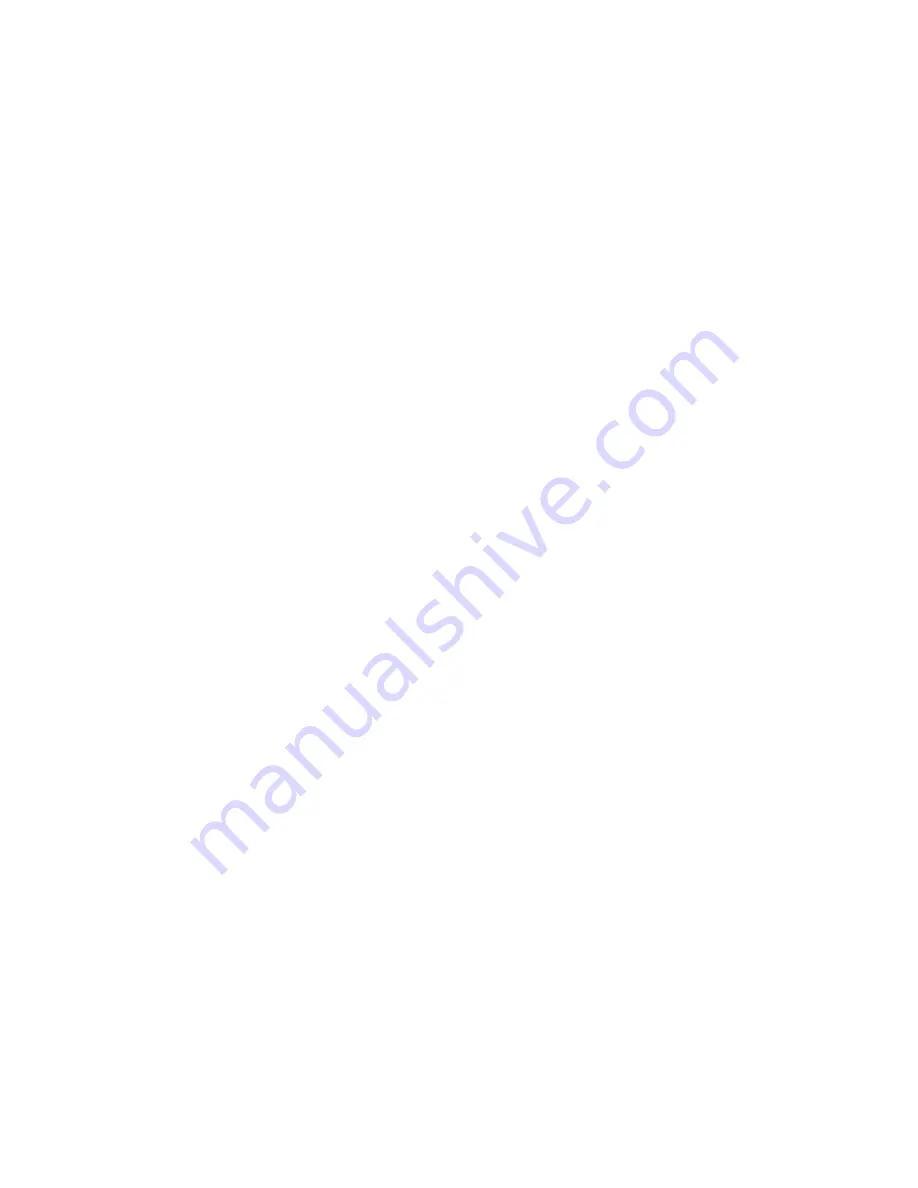
8. Mounting of Wheels
• Check the wheel dimensions: the outer diameter must not exceed recommended measurement and the
hole must be correct as specified on the machines specification plate. The wheel should easily slide on to the
spindle shaft and must never be forced on with pressure.
• Before mounting a wheel, it must be checked for flaws and damage. Test wheel by letting it hang
freely and hitting it lightly with a piece of wood. A good wheel should make a clean clear metallic
sound, while a defective wheel will sound “dead”.
• If reduction bushes for wheel’s hole size are used, check that they do not protrude over the sides of
the wheel.
• The wheel must be supplied with washers of paper or compressible material placed around the hole on
each side of the wheel. If these are missing or damaged, new ones must be put on.
• The inner and outer flanges, which are delivered with the machines, must always be used. They have and
must retain the same diameter and must be kept clean and undamaged. The inner flange is secured to the
spindle shaft.
• Place the wheel between the two flanges and fasten the nut. Note, there are left and right hand threads in
the left and right sides, respectively. The nuts must be tightened enough to hold the wheel securely but avoid
over tightening as this can cause damage to the wheel.
9. Wheel Care
Store spare grinding wheels flat on a firm surface with a layer of compressible material between the wheels
and the storage surface. Similar material should be placed between them when a number are being stored.
As the grinding wheel is used it will wear. It is recommended that the wheel is replaced when the diameter
has been reduced approximately 25% below its original size (e.g 300mm to 225mm : 200mm to 150mm :
150mm to 112mm : 125 to 94mm).
Wear on the wheel can cause eccentricity leading to machine vibration and “bouncing of workpiece”.
Unless this condition is corrected it can result in further damage to the wheel and possible harm to the
motor bearings.
To obtain wheel balance and good efficient grinding action the wheel must be re-dressed. We recommend
the
use of Record Power dressing sticks, use the coarse grey stick (Part no: SDS-1) to remove imperfections
and debris to ensure a true running circular stone. Then use the fine textured white stick
(Part no: SDS-2) to clean your grindstone back to its original condition. Use fine and coarse dressing
sticks in conjunction with each other to prolong the life of your grindstones.
10. General Care
IMPORTANT - THIS MACHINE MUST BE EARTHED
Always disconnect the machine from the power supply before making any adjustment to the wheels or any
other attachment. Check the supply cable and replace if damaged. Replacement of the power cable should
only be carried out by a qualified electrician.
The earth wire must always be connected and maintained. Keep the area around the machine as clean as
possible.
Replace damaged tool rests and spark shields. Failure to do this can cause accidents.